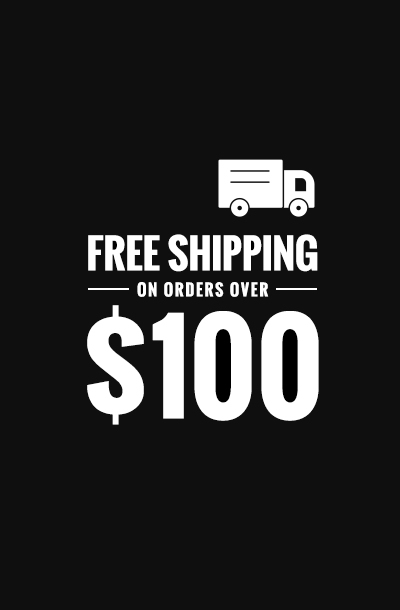
Processed Molded Pulp
Processed molded pulp features secondary special finishes such as hot pressing, coating and dying. The additional process allows for higher quality molded pulp results for box inserts that require a more impactful unboxing experience.
- Available with all molded pulp inserts
- Large range of additional processes available
- Creates higher quality results
Overview
Processed molded pulp refers to any molded pulp box inserts that has gone through any additional processes such as dying, coating or hot pressing. This gives you the opportunity to customize your box inserts with molded pulp and creates more high quality results when used for product packaging. Available for all types of molded pulp inserts, processed molded pulp offers brands the opportunity to enhance the unboxing experience through detailed customization.
Printing
Finishing
Our Ordering Process
Looking for custom packaging? Make it a breeze by following our four easy steps - soon you’ll be on your way to meeting all your packaging needs!
Customize your packaging
Choose from our vast selection of packaging solutions and customize it with our wide range of options to create your dream packaging.
Add to quote and submit
After customizing your packaging, simply add it to quote and submit quotation to be reviewed by one of our packaging specialists.
Consult with our expert
Get expert consultation on your quotation to to save on costs, streamline efficiency and reduce environmental impacts.
Production & shipping
Once everything is ready for production, have us manage your entire production and shipping! Just sit and wait for your order!