Table of Contents
When it comes to corrugated packaging, individuals often mistakenly consider cardboard as the only type of packaging material. However, there is more to it than that. Cardboard is one type of material, and corrugated cardboard is another. Both materials are often confused with one another but serve different purposes depending on the product.
In this post, we will explore the differences between cardboard and corrugated cardboard, go in-depth into the various aspects of corrugated material, look into quality control, and discuss the benefits and uses of such material. By the end of this article, we hope to give you a better understanding of corrugated boards so you can make the best decision for your product’s packaging!

Source: PakFactory
What is a Corrugated Box?
A corrugated box is a container made from sheets of packaging material known as corrugated cardboard. Due to its strength and durability, corrugated boxes are widely used for shipping large or heavy products. In fact, 95% of all shipped products in North America use corrugated material!
And, What is Corrugated Cardboard?
Corrugated cardboard, also known as corrugated fiberboard or corrugated cartons, typically consists of three layers of kraft paper: two outer layers of flat linerboard and an inner layer of fluted (wavy) medium. For example, pizza boxes are commonly made from corrugated cardboard.
In some cases, additional layers can be added for extra protection, which we will discuss in more detail later.
Cardboard vs Corrugated – What’s the Difference?
Now that you know what corrugated packaging is and how common it is in shipping, you may wonder what the difference is between corrugated and cardboard. We’ve mentioned briefly that corrugated cardboard differs from cardboard, but let us unpack this topic further.
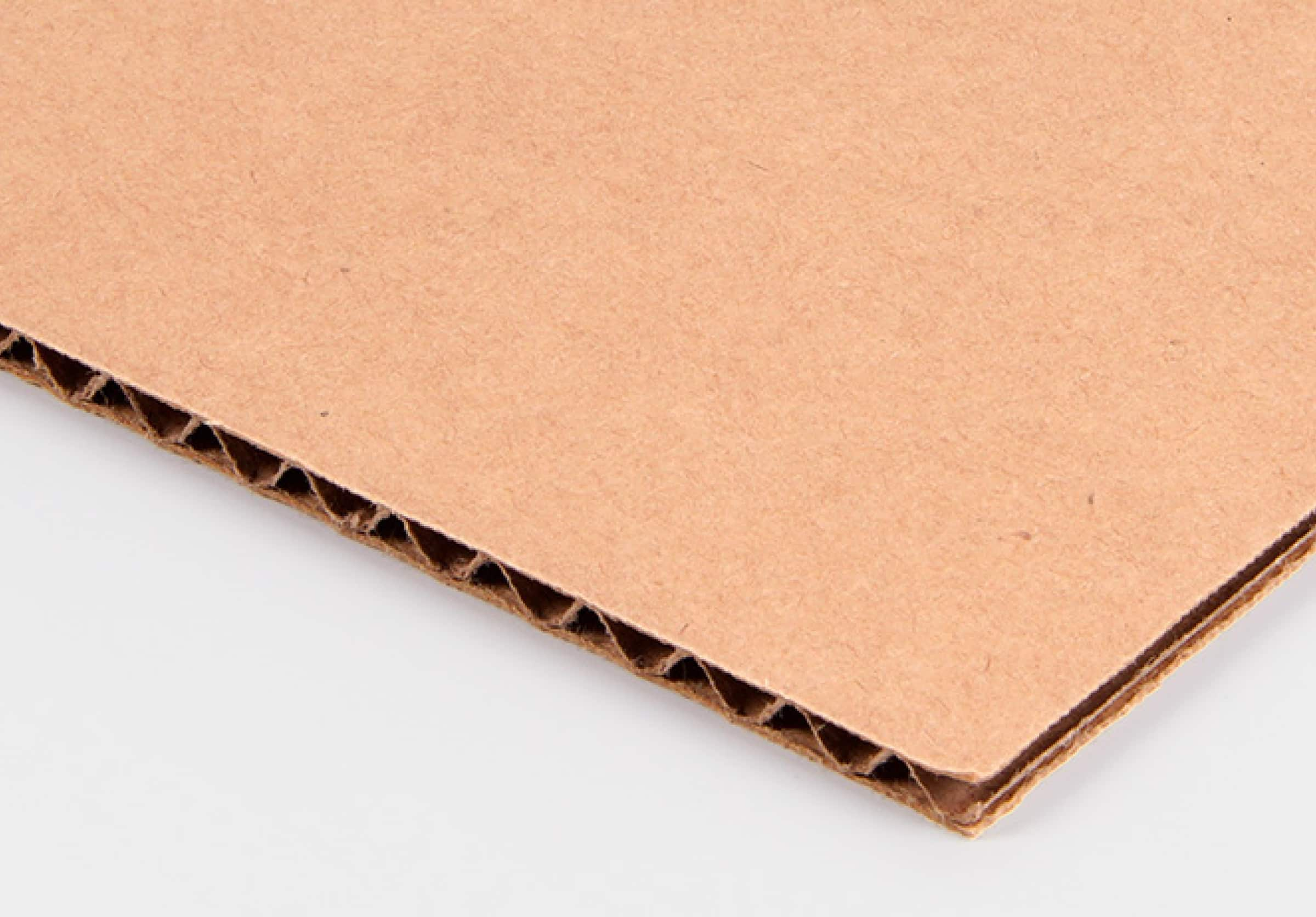
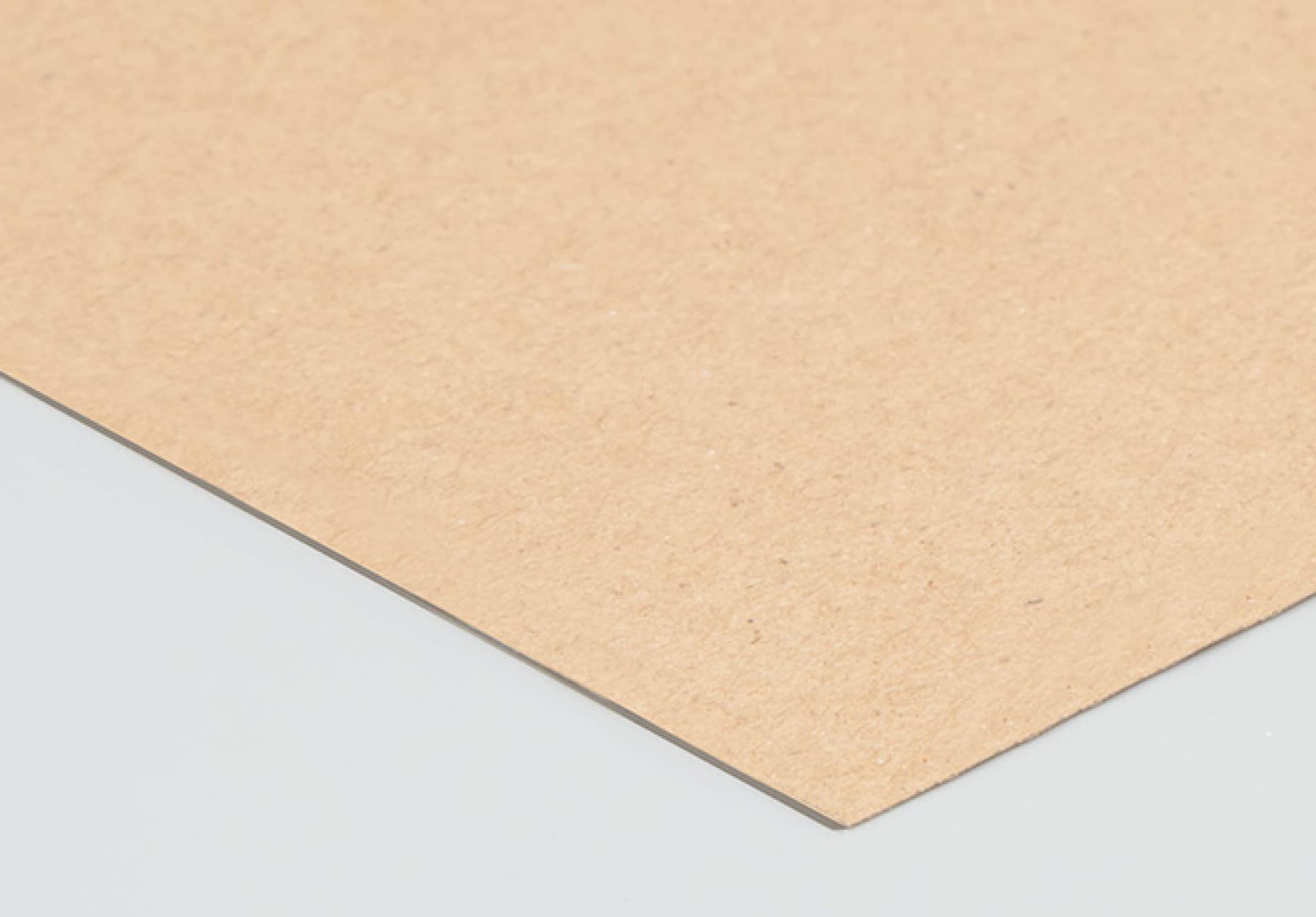
Cardboard is generally made of paper stock or heavy paper pulp. It’s typically used in folded cartons for smaller products but can also be used as structural support inside a box to keep its shape during transit. However, cardboard by itself is not very protective.
Corrugated, on the other hand, is different. It has three fiberboard layers, offering increased durability, protection, and versatility. This material resist bending and is among the best options whether your company is shipping large packages or sending a few products. Still unsure of the difference? Check out the chart below for a comparison!
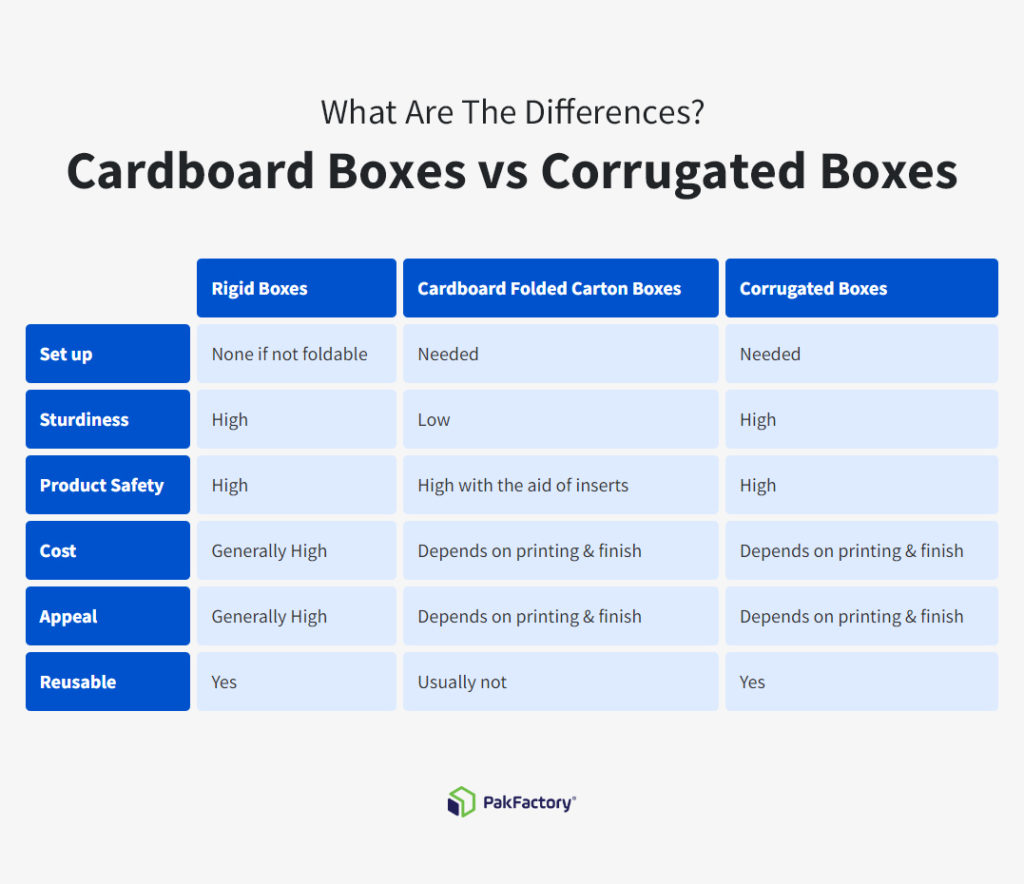
Liners Materials
With a better understanding of corrugated materials, choosing the most commonly used outside liner for manufacturing corrugated boxes should be less daunting.
- Kraft Paper liners consist of 70-80% “virgin” chemical pulp fiber, which results in a top paper grade that is very stiff and durable. It is the most sustainable option out of all the types of corrugated paper materials available, but it is also the most costly.
- Test Paper liners are less expensive than Kraft because they use more recycled fiber content, resulting in less durability. The higher recycled fiber content also makes the paper more difficult to print on, but it is very common to use test paper as the inner linerboard of a corrugated box.
- Flute Paper Liners are available in Semi-Chem and Waste Based Fluting. Semi-Chem uses virgin fibers and a neutral sulphite semi-chemical process, while Waste Based Fluting uses 100% recycled fibers.
But speaking of flute paper, now is a good segue into the different flute grades available, too!
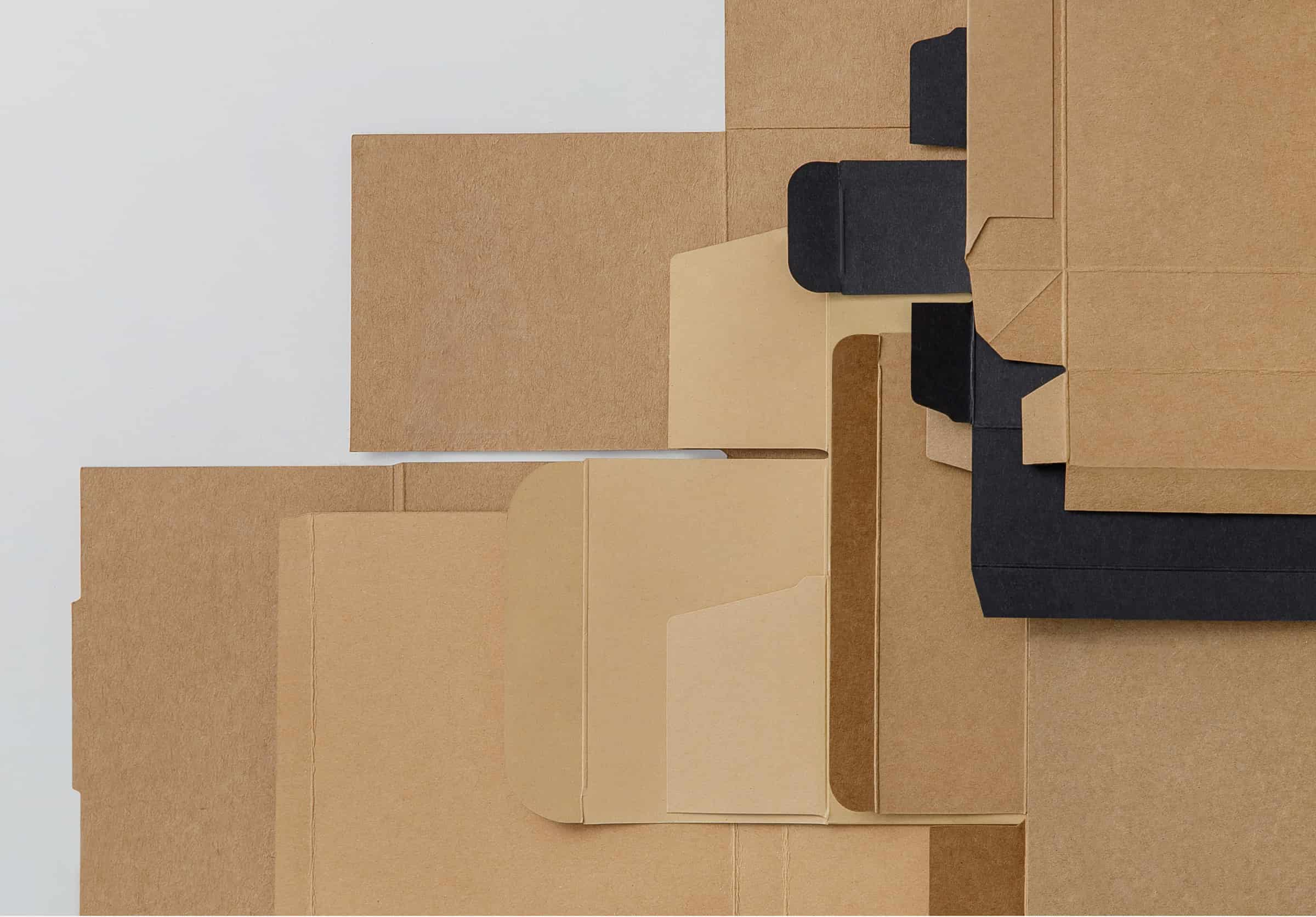
Source: PakFactory
Corrugated Flute Types (Flute Grades)
Corrugated flute provides cushioning, strength, and compression-resistant qualities to your package depending on the different flute grades, allowing for even more customization. But before we examine each flute profiles in detail, look at our corrugated flute chart for a quick visual comparison:
- A-Flute – 1/4” thick is the largest flute size. This flute grade has the highest protection and cushion qualities. It is very good at handling compression and stacking and is often used for packaging fragile items.
- B-Flute – 1/8” thick flute appears much thinner than others but is still quite strong, with excellent puncture and crush resistance. B-flute has outstanding all-around performance for various packaging or as additional material for padding and dividing. It even has a flatter surface for higher-quality printing and easy die-cutting.
- C-Flute – 3/16” thick is flexible and one of the corrugated boxes’ most versatile flute grades. It has average crush resistance, stacking strength, and printing properties. You have likely seen C-Flute corrugated cardboard used for shipping boxes but also for packing glass, dairy, and furniture products.
- E-Flute – 1/16” thick is not typically used for shipping. E-flute thickness is on the thinner side of flute grades, so it is often used as an alternative for paperboard folding cartons. However, you may still use E-Flute for cosmetics, fragile glass, ceramics, and other small and delicate products. E-Flute has excellent compression strength, crush resistance, and a relatively flat surface for high-quality printing applications.
- F-Flute – 1/32” thick has protective qualities similar to E-Flute but with an even smoother surface for high-quality printing. It is common for you to use F-Flute for clamshell packaging in the US fast-food industry, but in Europe, this grade of fluting is a standard option for specialty and retail packaging.
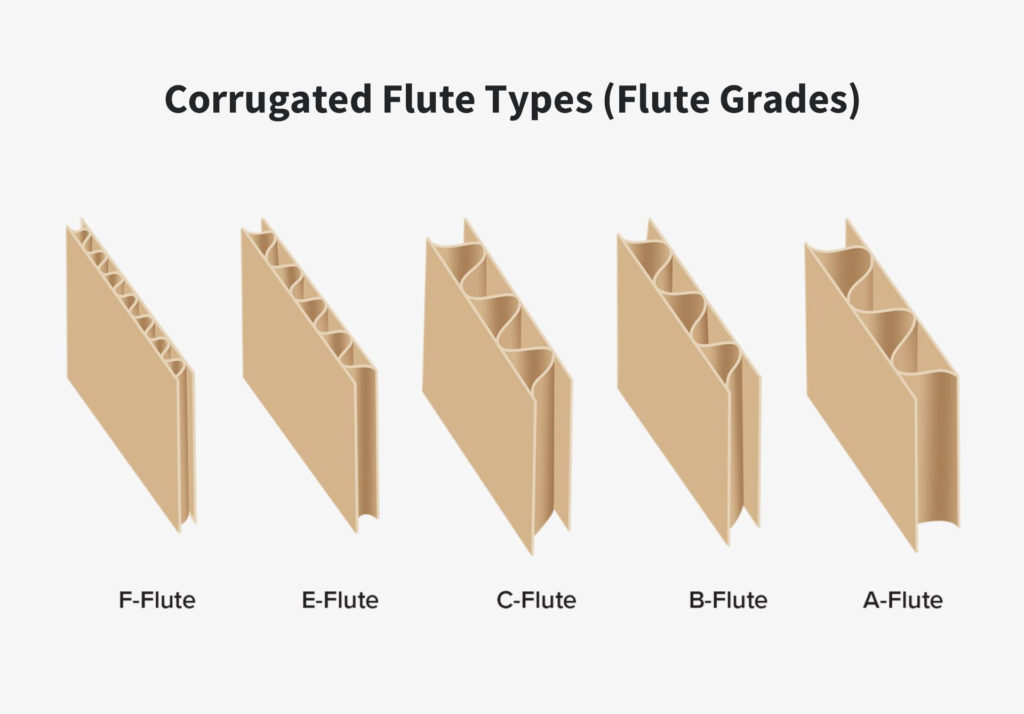
Source: PakFactory
Types of Corrugated
Now that we’ve covered the different types of liners and flute grades, it’s time to look at combined board! Fluting and liners can be combined in different layers to create a variety of flute structures that have different thicknesses.
- Linerboard – The ‘face’ of the fiberboard sheet. You glue the flute onto this board.
- Single Face – Consists of one linerboard with the glued flute visible on one side. It is sometimes called corrugated paper.
- Single Wall – The most common thickness. Two sheets of linerboards with one fluted fiberboard glued in between.
- Double Wall – Three sheets of linerboard and two fluted fiberboards in between.
- Triple Wall – Four sheets of linerboard and three fluted fiberboards in between. This option can withstand heavier weights up to almost 300 lbs but is less flexible.
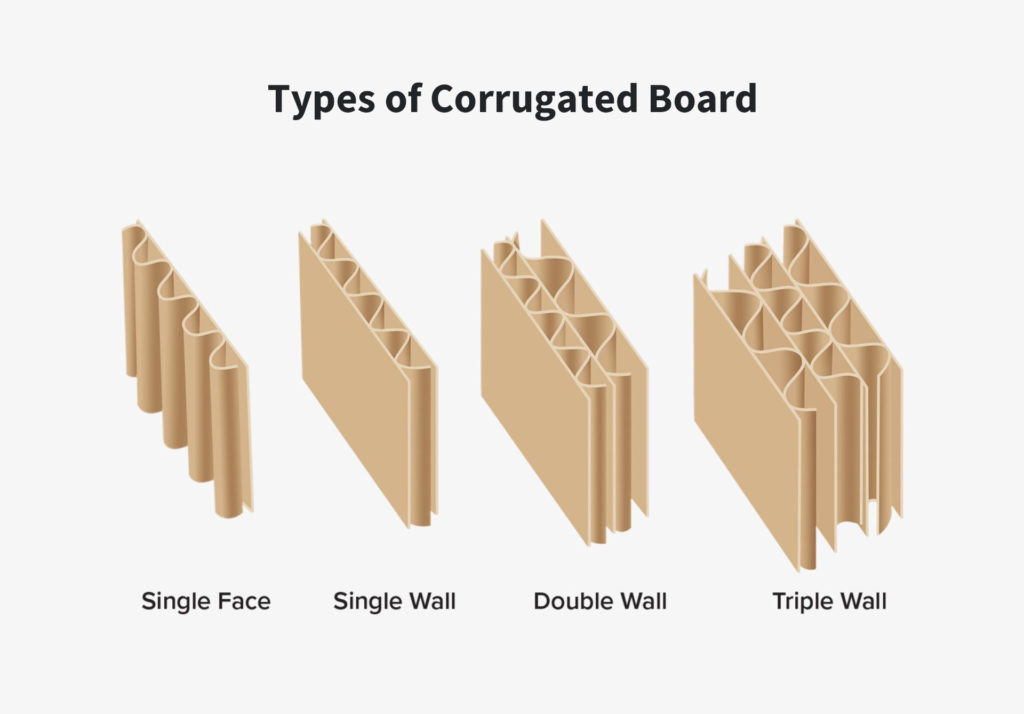
Source: PakFactory
Examining a little further with double and triple walls, different combinations of flute grades are possible with these options. Some industry standard combinations include:
- AC Flute – A mix of the two most protective corrugated grades. AC Flute is excellent if you need extra protection for harsh shipping and handling processes.
- BC Flute – An outstanding all-around performer, this combination provides high-level transit protection and is common for shipping boxes.
- EB Flute – Provides superior transit strength and safety, while the outer E-Flute allows for an excellent, high-quality printing surface.
Corrugated Box Styles
With everything from construction to thickness covered, the corrugated box styles is the last topic to cover before moving on to quality control. By combining layers, customizing flute grades, or adding interior padding, corrigated boxes can fit any packaging need.
Custom corrugated boxes meet any specific requirement of the user. Some common types of corrugated boxes include:
- Tab Lock Roll End
- Roll End 3 Flaps Tuck
- Roll End Tuck Front
- One Piece Folder Box
- Tuck Top Auto Bottom
- Regular Slotted Box
- Full Slotted Box
- Half Slotted Container (HSC Box)
- Gusset Folder
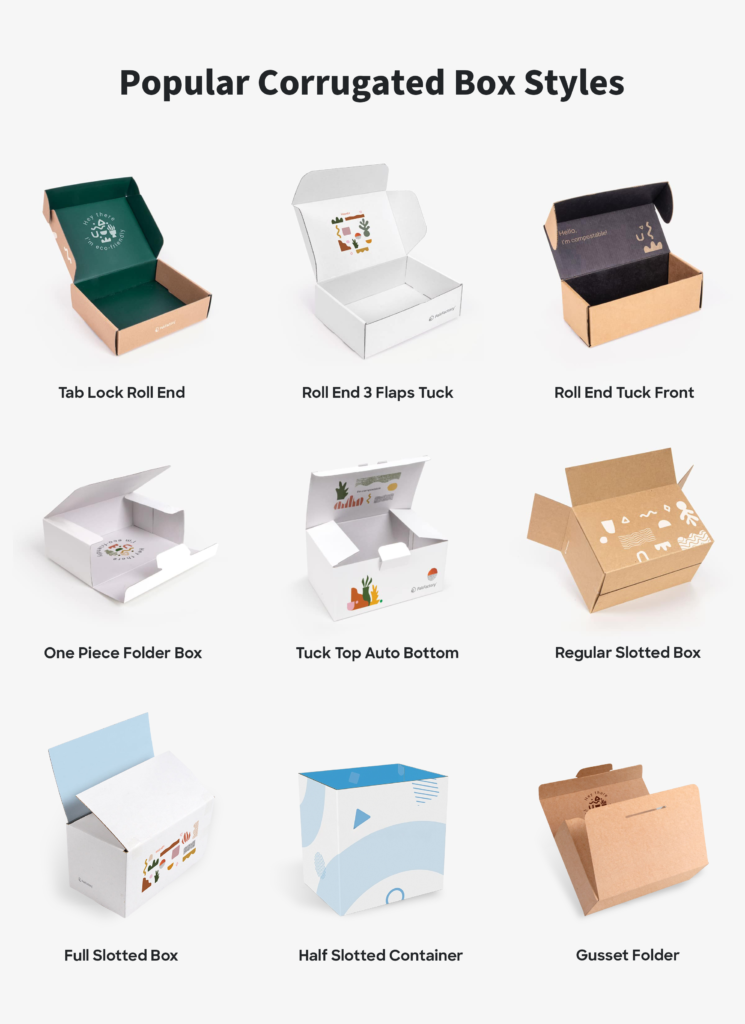
Source: PakFactory
To view more box styles , visit PakFactory’s corrugated box catalog.
Quality Control Tests
With the sheer amount of design and customization options available at your fingertips, there might be many questions about protection. Corrogated boxes are subject to stress and impact during packing, shipping, and storage, so there needs to be ways to test your custom package’s strength.
Some standard tests include the Edge Crush, Flat Crush, and the Burst Test.
- Edge Crush Test is one of the essential tests for corrugated cardboard. As the name implies, force is applied perpendicular to the edge of the corrugated cardboard until it buckles. The results ensure the strength and durability required to handle heavy loads and stack resistance.
- Flat Crush Test is also used and is similar to the Edge Crush Test. Force is applied directly on the surface area of the corrugated cardboard until the flute flattens and compromises its structure. This test similarly determines the compression and stacking resistance of the corrugated cardboard required to carry heavy loads.
- Mullen Test (or Burst Test), is a standard industry measures that challenges the durability of the corrugated cardboard surface by determining the force needed to puncture the board.
All of these tests ensure the quality of custom corrugated packaging so your products have the highest level of safety they need to reach their final destination.
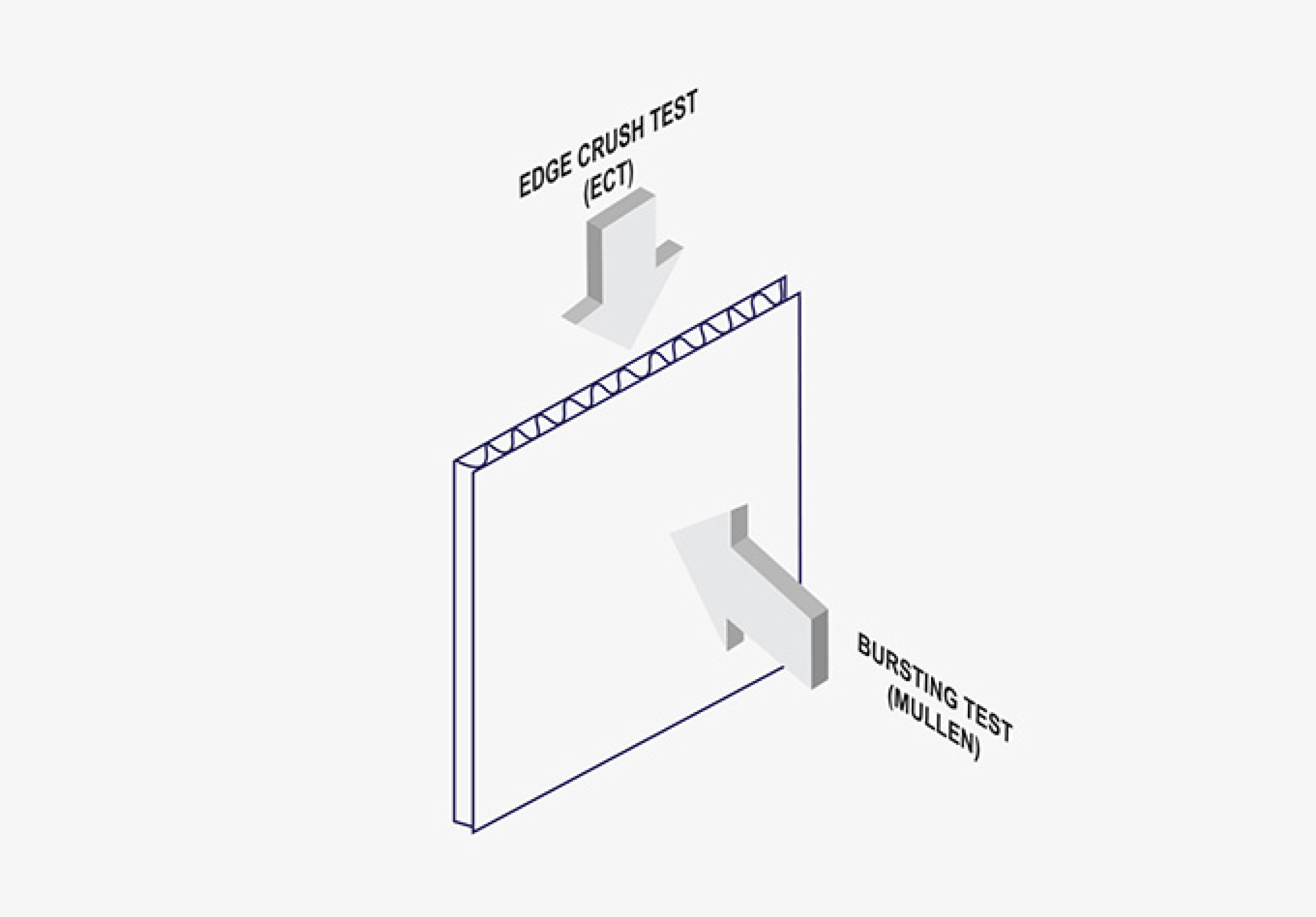
Source: PakFactory
Box Maker’s Certificate
After customization and thorough testing, it’s time to learn about the Box Maker’s Certificate (BMC). The BMC provides quick specifications about the box and comes in two versions: the ECT-rated BMC and the Mullen-rated BMC.
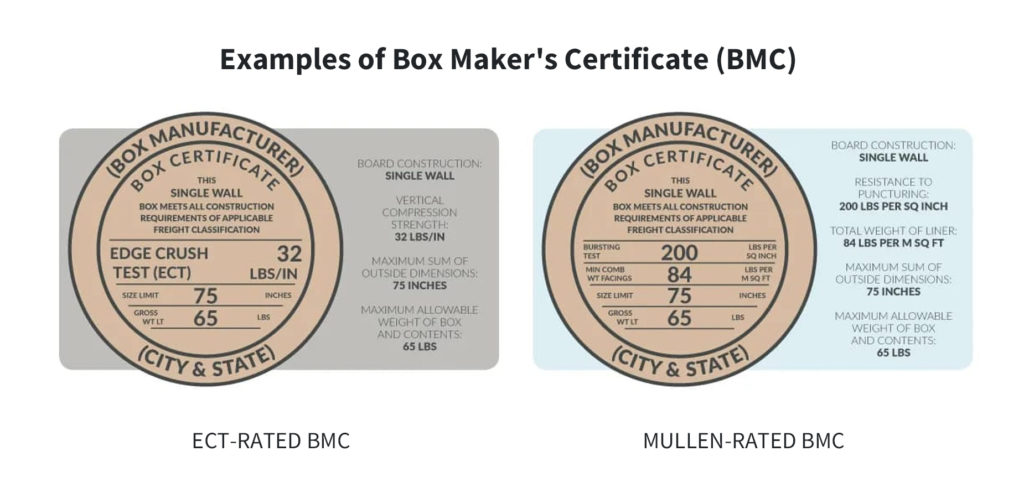
You will notice a few differences, but these box manufacturer certificate provide the same information:
- The Box Manufacturer on the outer ring indicates the company responsible for manufacturing your box.
- Board Construction is the information displayed directly under where it says box certificate. This information tells whether the box is a single, double, or triple wall.
- Minimum Combined Weight Facings is the total weight of the linerboard used before the entire linerboard is cut and made into boxes.
- Size Limit refers to the maximum outer measurements of the box, which are used for storage and shipping purposes.
- Gross Weight Limit is the maximum weight allowed for the box and the items within.
- City and State are located at the bottom of the label. It indicates the location where the box is constructed and shipped.
Benefits of Corrugated Packaging
If you’ve been following along, you probably already know some of the benefits of corrugated packaging. Here are the main reasons why corrugated cardboard is popular:
- Protection and Durability – Corrugated boxes provide excellent protection and durability for items during transit. They can absorb impacts and offer cushioning support, making them ideal for shipping. These boxes withstand harsh conditions without damaging the contents and serve as an effective barrier against the elements, making them best for e-commerce packaging.
- Environmentally friendly – Sustainability is becoming increasingly important, particularly in packaging. Corrugated cardboard is a top choice packaging option for sustainability because it is made from recycled fibers, which makes it easier to recycle.
- Customizable – Because of the many options available for raw materials and their environmental-friendliness, corrugated packaging is the best option for those looking for bespoke packaging, including printing. The shape and thickness are easily customizable alongside graphics and surface printing.
What About the Disadvantages of Corrugated Boxes?
Many industries benefit from using corrugated packaging, especially e-commerce. Depending on the size and shape of the packaging, shipping and mailing can be more manageable. However, there are still some drawbacks to using corrugated boxes.
- Limited Weather Resistance – For starters, corrugated boxes are susceptible to inclement weather, such as rain or snow. The packaging can become deformed or lose its shape.
- Cost Considerations – The main drawback of using corrugated cardboard is its cost. It is relatively more expensive than other options due to supply chain disruptions, such as those caused by COVID-19, and environmental regulations aimed at reducing deforestation and promoting sustainable forestry.
These drawbacks may be disheartening for companies with lower budgets. However, it’s important to weigh these drawbacks against the benefits it offers in terms of protection, recyclability, and versatility. Moreover, there are many ways to reduce costs and create affordable luxury packaging!
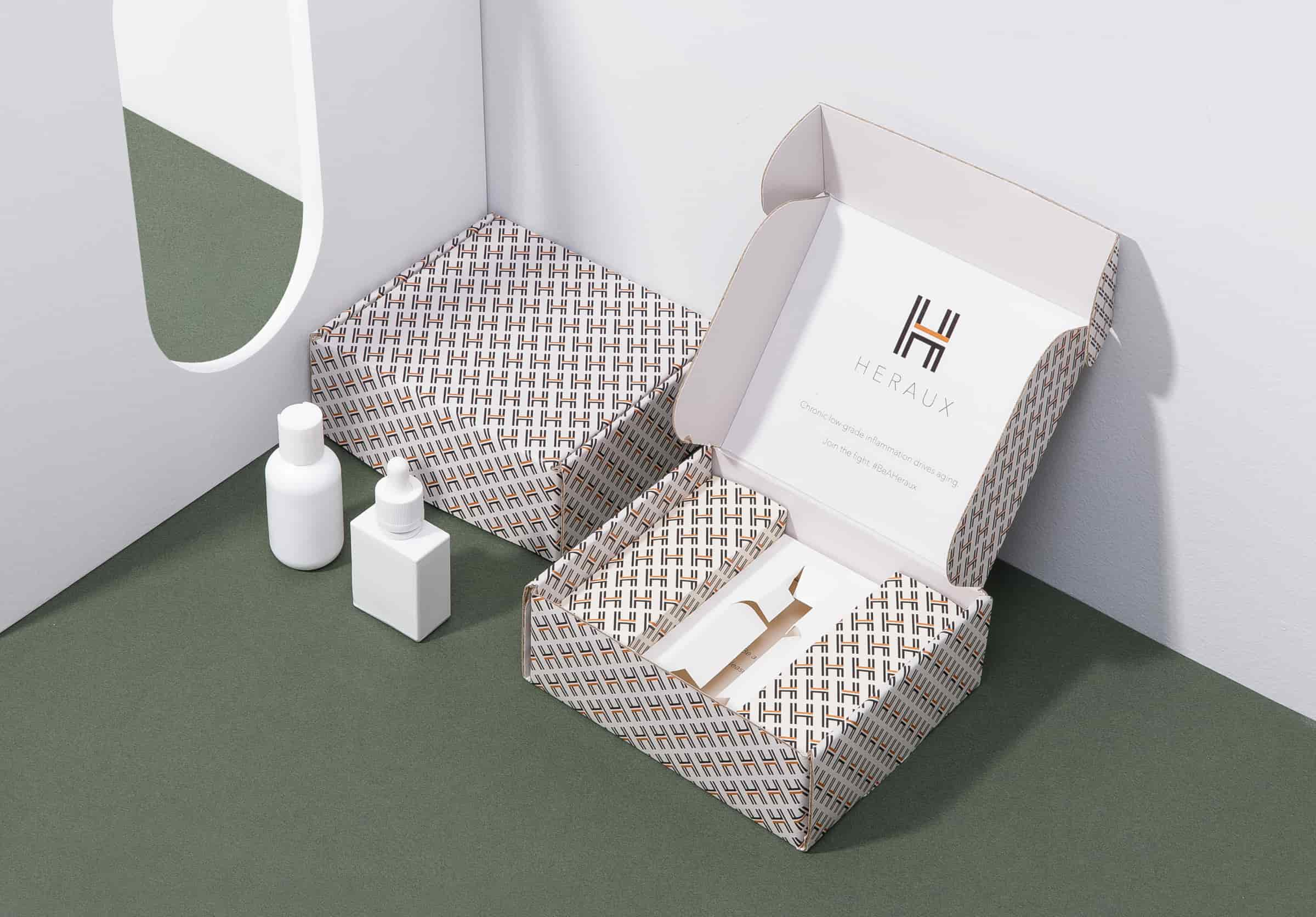
Source: PakFactory
Create Your Custom Corrugated Boxes Today!
Corrugated packaging is durable and customizable, providing creative freedom in corrugated box design to keep your product safe during transport. To learn more and start your project, contact our packaging specialists today!