Table of Contents
Packaging is essential for many industries, including food, beverage, pharmaceuticals, and retail. It serves the crucial function of protecting products, and the durability of packaging materials is vital to ensure that a package fulfills this role. One critical factor that affects packaging quality and durability is the paper grading.
Different paper grading types have varying characteristics that affect packaging strength, durability, and cost. Understanding the advantages and disadvantages of each option in the paper industry is crucial for businesses to choose the right type of packaging for their products.
This article will explore four types of popular paper grades for packaging: kraft paper, corrugated board, solid bleached sulfate (SBS) paperboard, and coated paper. We will also discuss the advantages of each paper grade and compare their strength, durability, and cost to help businesses make informed decisions when selecting packaging materials.
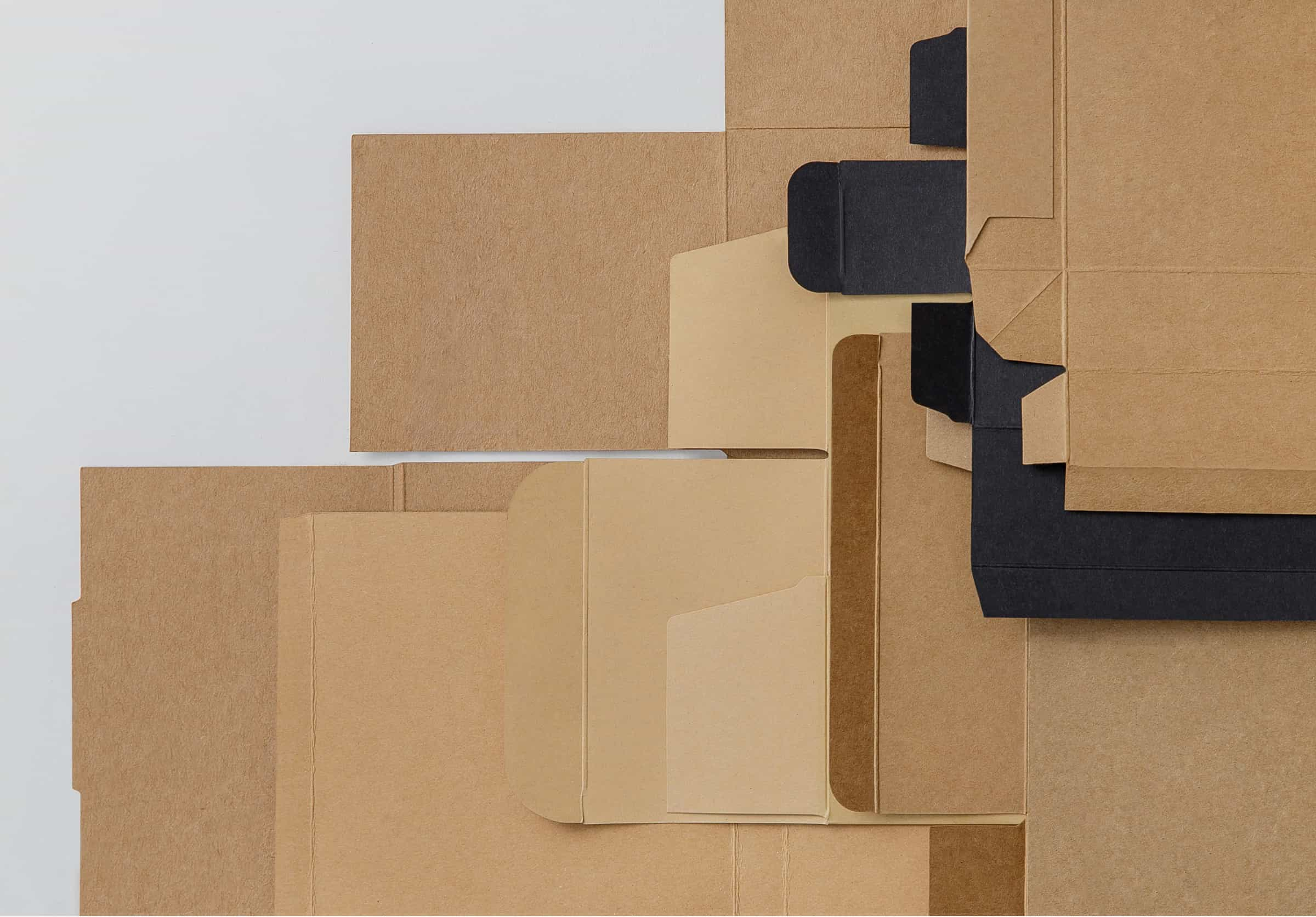
Source: PakFactory
But before we delve into the different types of paper grade for packaging, it’s important to note that choosing the right packaging material can significantly impact a company’s environmental footprint. Sustainable packaging materials like paper can help reduce carbon emissions, waste, and energy consumption compared to plastic or other non-renewable materials.
As such, many companies are increasingly adopting plant-based packaging solutions as part of their sustainability initiatives. So, with this in mind, let’s take a closer look at the most popular paperboard types!
What is Paperboard?
Paperboard is a versatile and durable type of paper-based packaging material made by compressing layers of paper pulp fibers to create a dense and rigid board. Paperboard can be customized to suit various packaging needs, such as food, cosmetics, retail packaging, and more.
Paperboard is eco-friendly and recyclable, making it ideal for sustainable packaging solutions. It comes in different grades, thicknesses, and finishes, ranging from uncoated to coated and matte to glossy.
Paperboard vs Cardboard
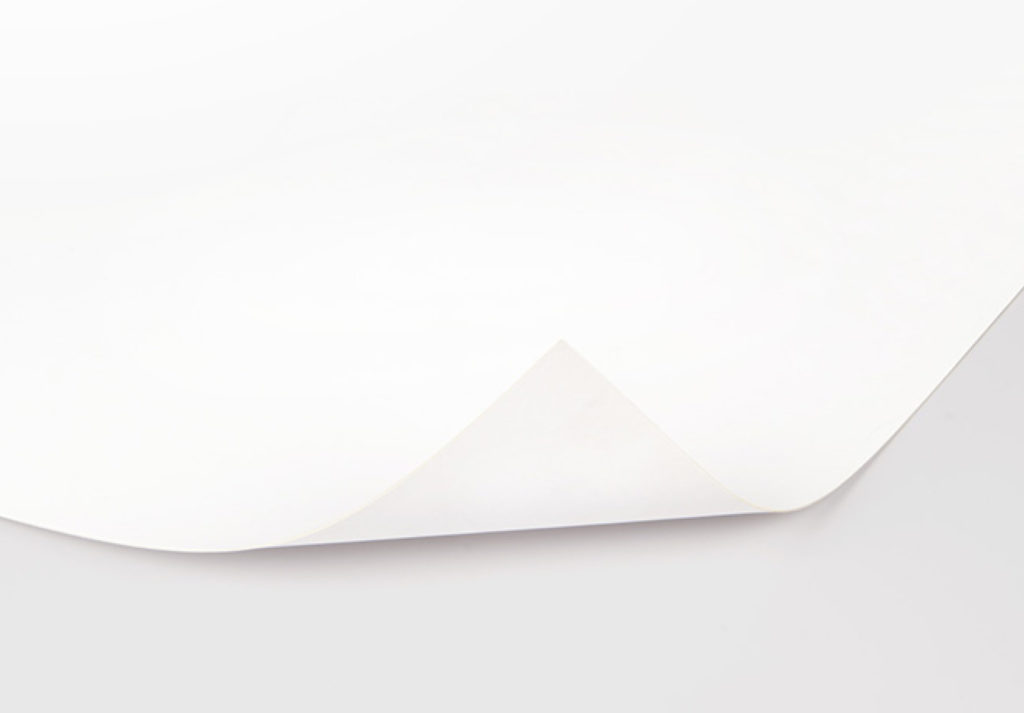
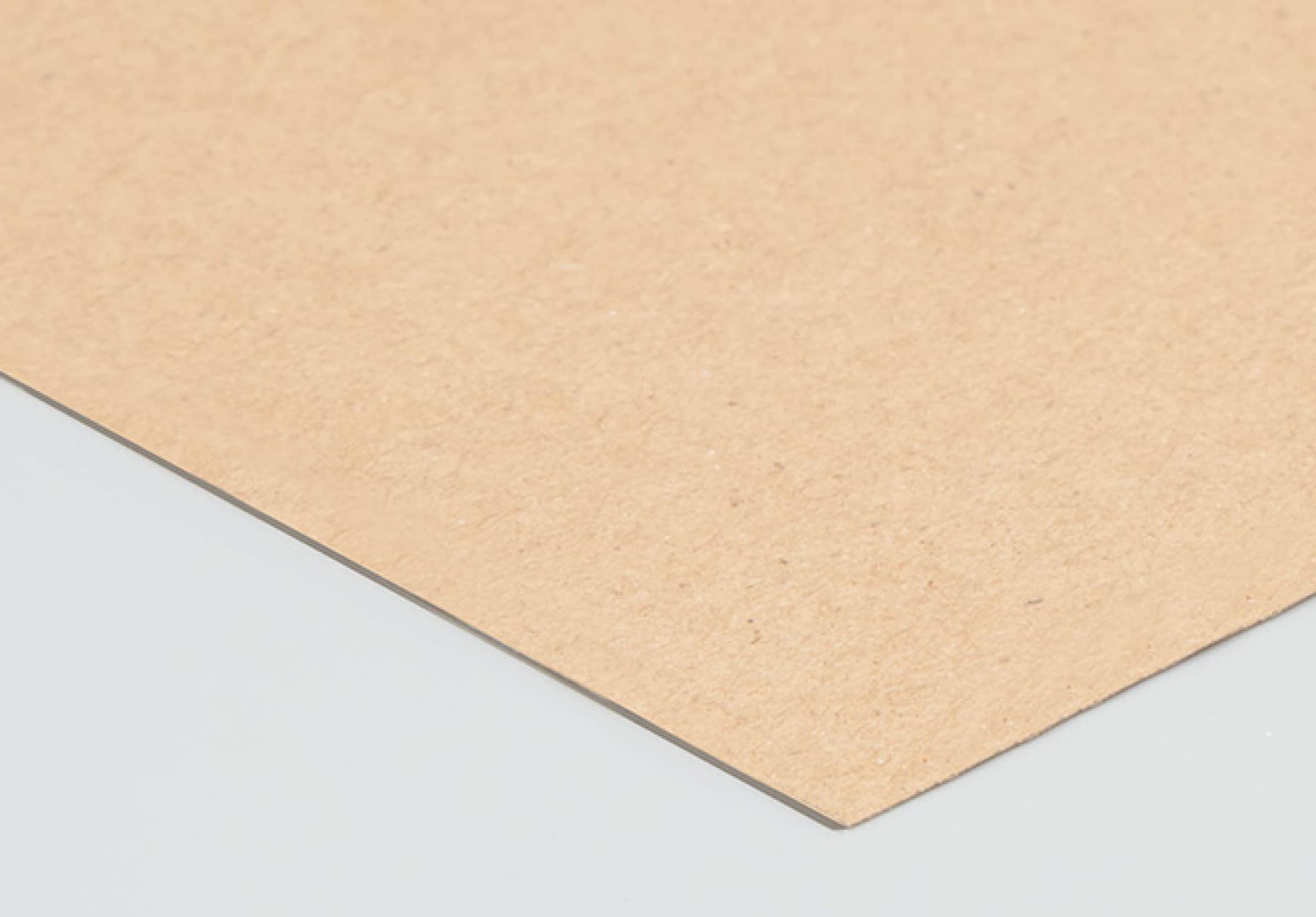
Paperboard and cardboard are two types of packaging materials commonly used in various industries. While they may appear similar, there are some key differences between the two.
Paperboard is a thick, lightweight, and durable material made of compressed paper fibers. It is commonly used for food packaging, cosmetics, and pharmaceuticals.
Cardboard, on the other hand, is a thicker and stiffer material made of multiple layers of paper and sometimes includes additional materials like plastics. The multiple layers commonly will feature 2 liner boards and one corrugated board,
Paperboard and cardboard are two packaging materials commonly used in various industries. While they may appear similar, the two have some key differences.
As explained earlier, paperboard is a thick, lightweight, and durable material made of compressed paper fibers.
On the other hand, Cardboard is a thicker and stiffer material made of multiple layers of paper and sometimes includes additional materials like plastics. The multiple layers commonly feature two liner boards and one corrugated board, which makes cardboard more suitable for applications requiring greater structural strength.
While paperboard and cardboard offer their own set of specific benefits, businesses need to consider factors such as product weight, shipping distance, and durability when choosing between them. Ultimately, the choice of packaging material will depend on your specific needs and requirements.
The Popular Paperboard Grades
Now that you know what paperboard is and how it differs from cardboard, we can explore the four popular types of paper grades for packaging. Each type of paper grade offers unique advantages regarding strength, durability, and cost-effectiveness, making them suitable for different packaging applications.
Understanding the characteristics and benefits of each type of paper grade is crucial for businesses to choose the most suitable packaging material for their products.
Clay Coated News Backboard (CCNB)
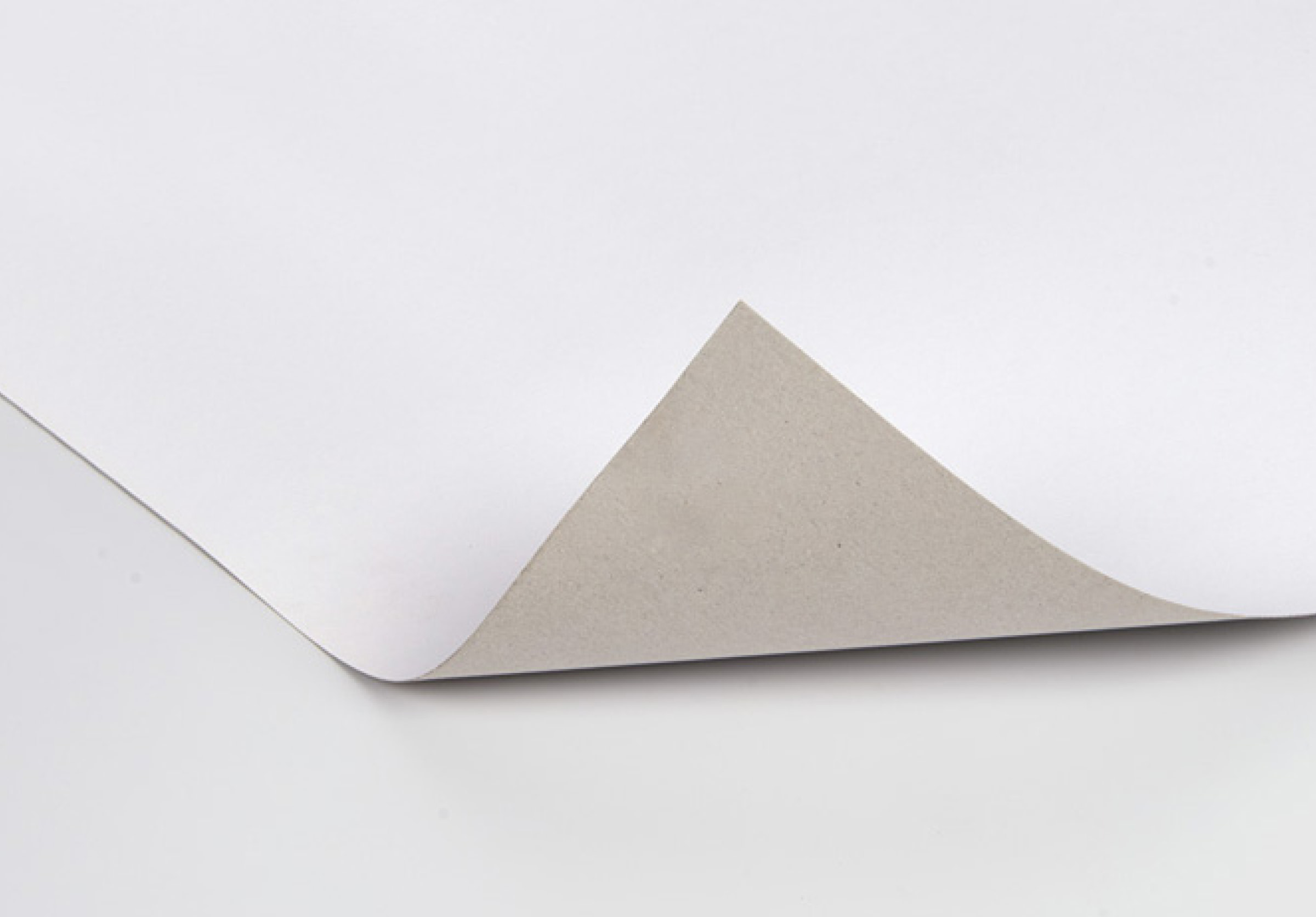
Source: PakFactory
Clay Coated News Backboard (CCNB) is a paperboard made from a blend of recycled newsprint, mixed secondary paper, and old corrugated containers. Due to its lower tensile strength and printing output, CCNB is commonly used for low-cost folding carton packaging for products such as dry food, pet food, laundry detergent, and other non-food items.
However, when exposed to wet conditions, CCNB paperboard boxes absorb large amounts of water, making them unsuitable for products requiring higher moisture resistance or weight capacity. But despite this disadvantage, CCNB remains a cost-effective option and is frequently used by budget cereal brands for cereal boxes.
CCNB is also eco-friendly for businesses looking to reduce their environmental impact. Since it consists of recycled materials, CCNB minimizes the need for new virgin paperboard production, which can lead to deforestation and other environmental issues. Additionally, using recycled materials in CCNB reduces the amount of waste in landfills, contributing to a more circular economy.
Still, it is important to note that while CCNB is a recycled material, the clay coating can make recycling difficult. Some recycling facilities may not have the capability to separate the clay from the paperboard, leading to the contamination of other recycled materials.
Nevertheless, businesses can still positively impact the environment by using CCNB and other recycled paperboard grades while exploring alternative sustainable packaging materials and practices.
Solid Bleached Sulfate (SBS)
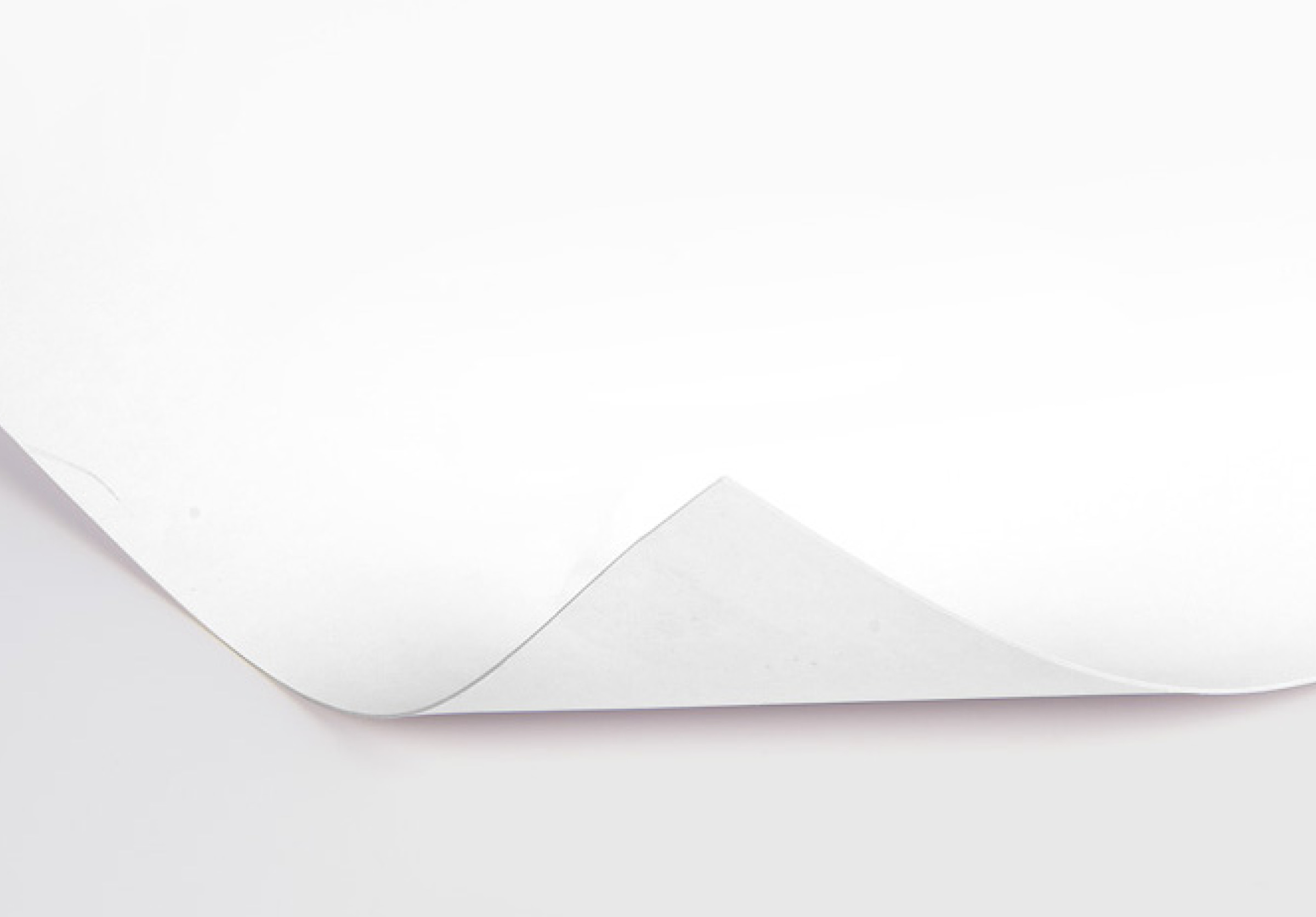
Source: PakFactory
Solid Bleached Sulfate (SBS) is a high-quality paperboard grade widely used in the packaging industry. According to Statista, 71% of the world’s supply of SBS comes from North America and is used for packaging retail products.
Making SBS involves chemically pulping fibers and then bleaching them to achieve a pure white color. The bleached wood pulp is then refined and formed into boxes.
SBS is the best for product packaging thanks to its superior strength, durability, and white surfaces on both the inside and outside of the box, making it optimal for printing since SBS can be coated on one side (C1S) or both sides (C2S), offering businesses flexibility in terms of their packaging design and printing needs. The quality of SBS also allows for special processes such as embossing and debossing, hot foil stamping, or spot UV printing.
SBS boxes are particularly trendy for cosmetics and personal care items due to their elegant and high-end appearance. Still, these boxes are also popular in industries such as food, pharmaceuticals, confectionery, baked items, tobacco, and more.
However, one major disadvantage of SBS is that it is not an eco-friendly option. The production of SBS involves a significant amount of bleaching, which can release harmful chemicals into the environment. Additionally, SBS is typically made from virgin fibers, meaning this type of paperboard grade contributes to the significant environmental issue of deforestation.
Another disadvantage of SBS is its relatively high cost compared to other paperboard grades, making it less accessible to small businesses or those on a tight budget.
SBS is also unsuitable for packaging products exposed to moisture or wet conditions, as it has poor water resistance. And though SBS is high-quality, it might not be suitable for products requiring heavy-duty protection. Other grades, like a corrugated board, are a better choice in such cases.
Folding Box Board (FBB)
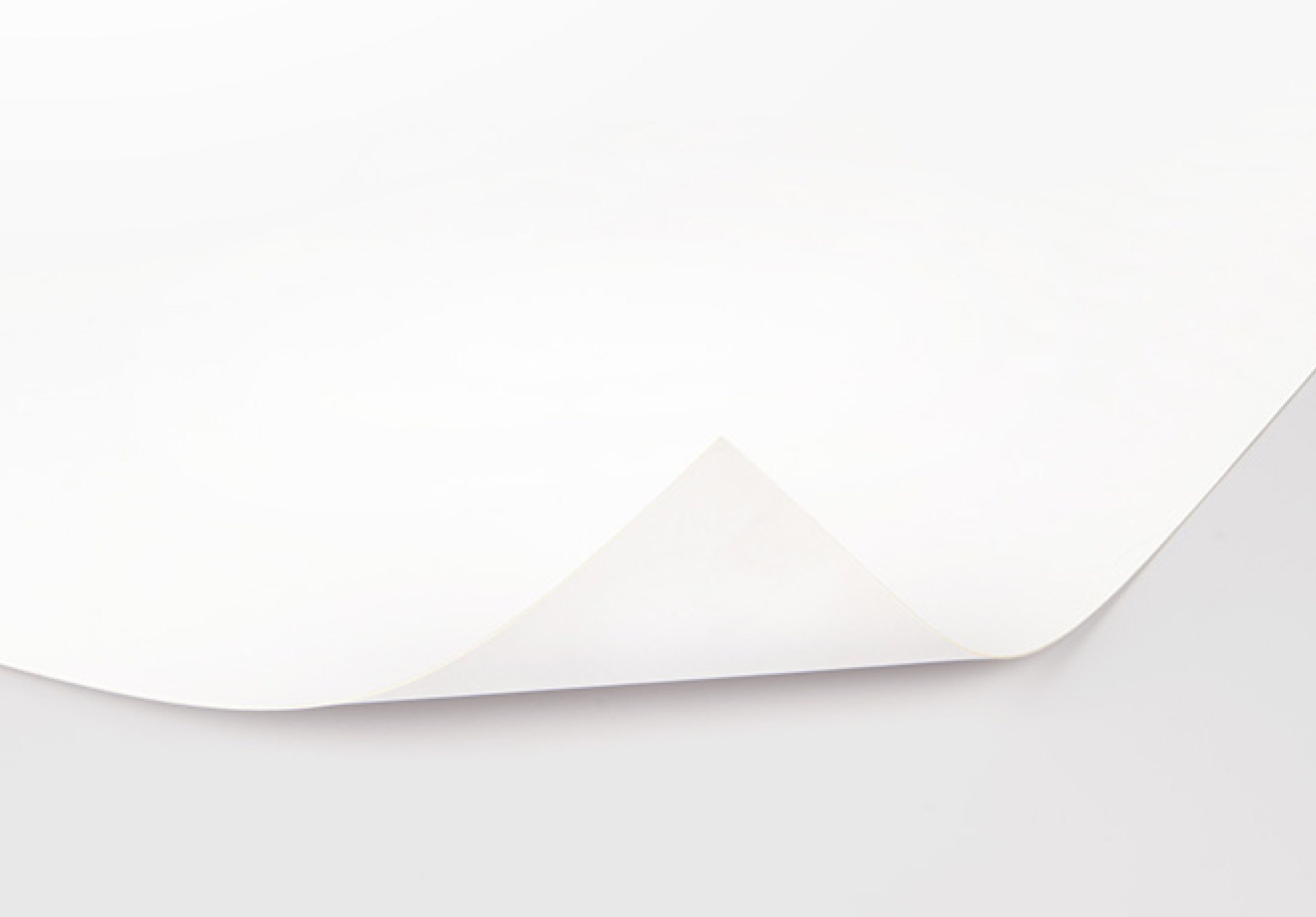
Source: PakFactory
Folding Box Board (FBB) is a high-quality paperboard grade chemically and mechanically manufactured using multi-ply paper pulp materials, making it strong and durable.
Unlike SBS, the mechanical pulp composition of FBB provides a stiffer composition, making FBB a popular choice for businesses that require packaging that can withstand wear and tear during transportation and storage. Additionally, the smooth surface of multi-ply FBB also provides optimal opportunities for high-quality printing using offset technology.
FBB boxes are versatile and excellent for a wide range of industries, including food, cosmetics, and pharmaceuticals, and are widely used in India as the primary packaging substrate by businesses.
But while the Folding Box Board is an excellent choice for product packaging due to its durability and smooth printing surface, it does come with a few disadvantages. Firstly, FBB is more expensive than other paper grades due to its high-quality production process.
Additionally, due to the use of virgin fibers, FBB is not as environmentally friendly as other paper grades, such as recycled paper. But though FBB requires virgin fibers, many FBB manufacturers are beginning to use sustainable forest management practices and offer recycled paper content options, lessening this environmental impact.
Another environmental disadvantage of FBB is that it can be challenging to recycle due to its multi-layered composition. While many recycling facilities can handle FBB, recycling may require more energy compared to other paper grades, which can impact its overall environmental footprint.
But despite these disadvantages, many businesses continue to use FBB for their product packaging due to its strength, durability, and high-quality printing capabilities for custom-printed paper.
Natural Kraft (SUS) and Coated Unbleached Kraft (CUK)
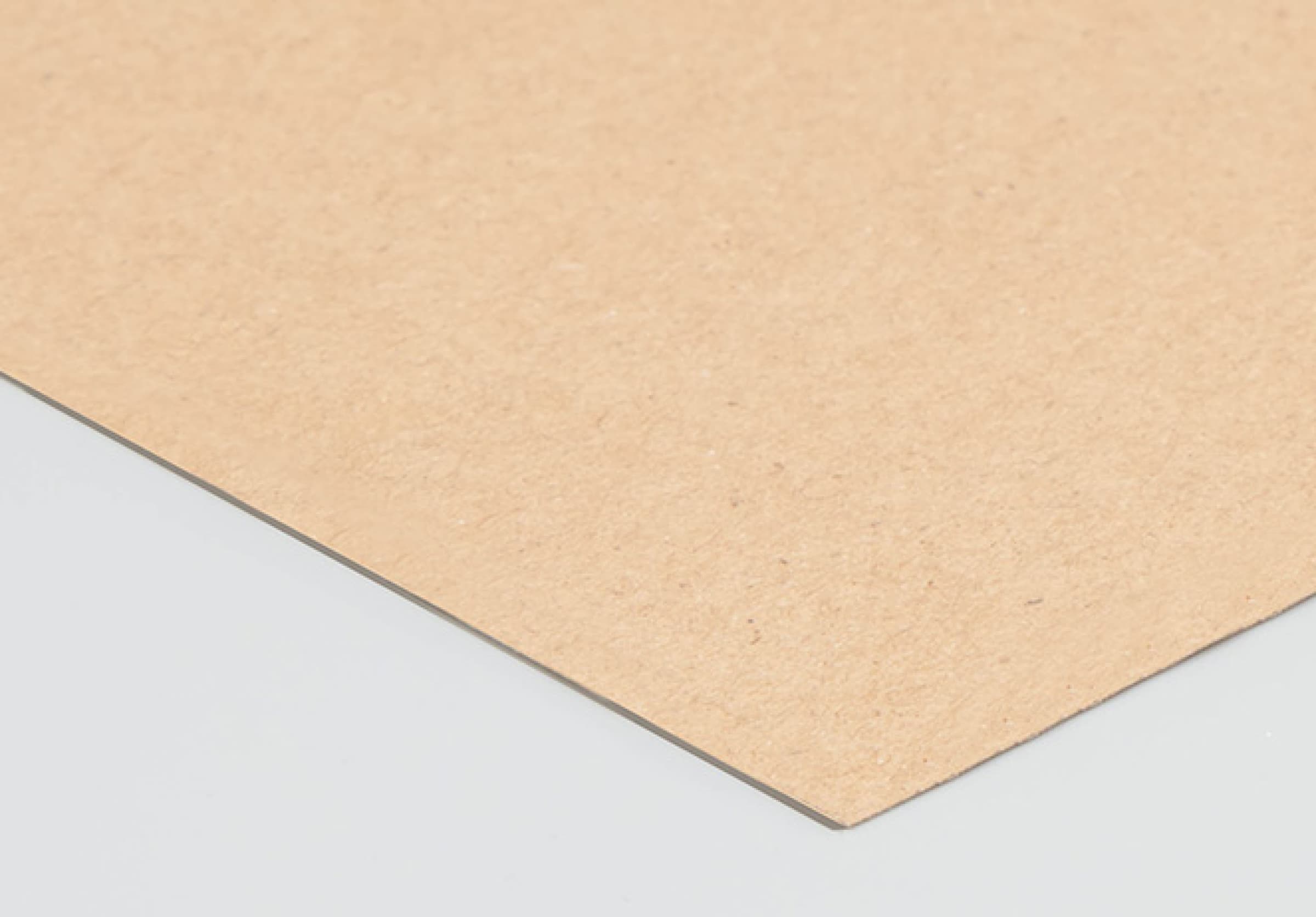
Source: PakFactory
Natural Kraft (SUS) and Coated Unbleached Kraft (CUK) paperboard are becoming increasingly popular in the packaging industry as eco-friendly paperboard grades that offer a more natural look and feel.
These paperboard grades are manufactured from recyclable materials, such as unbleached wood pulp. Using unbleached pulp and recycled materials makes SUS and CUK an ideal choice for companies looking for sustainable packaging solutions, as the uncoated papers also make this material very convenient to recycle.
One of the key features of these paperboard grades is their natural brown color, which gives a distinct aesthetic appeal. However, the natural color can also be a limitation, as it may not be suitable for products that require more vibrant colors.
Despite this, SUS and CUK offer many advantages, making them the preferred choice for many packaging applications.
SUS is often coated with a naturally occurring clay coating that provides a smooth surface ideal for printing. This coating also offers some degree of water resistance, which makes it an ideal choice for packaging products that may be exposed to moisture.
Alternatively, CUK is usually coated with a layer of polyethylene (PE) resin, which offers the paperboard some tear resistance, durability, and water/grease resistance.
But while these paperboard grades offer some tear resistance, they are less durable than other grades like SBS or FBB. Additionally, these paperboard grades’ more natural and textured appearance may not be suitable for special processes such as embossing, debossing, or foil stamping.However, even with these disadvantages, SUS and CUK are still great choices for companies that require food-safe packaging or those looking to promote a more natural look and feel.
Popular Finishes for Paper Packaging
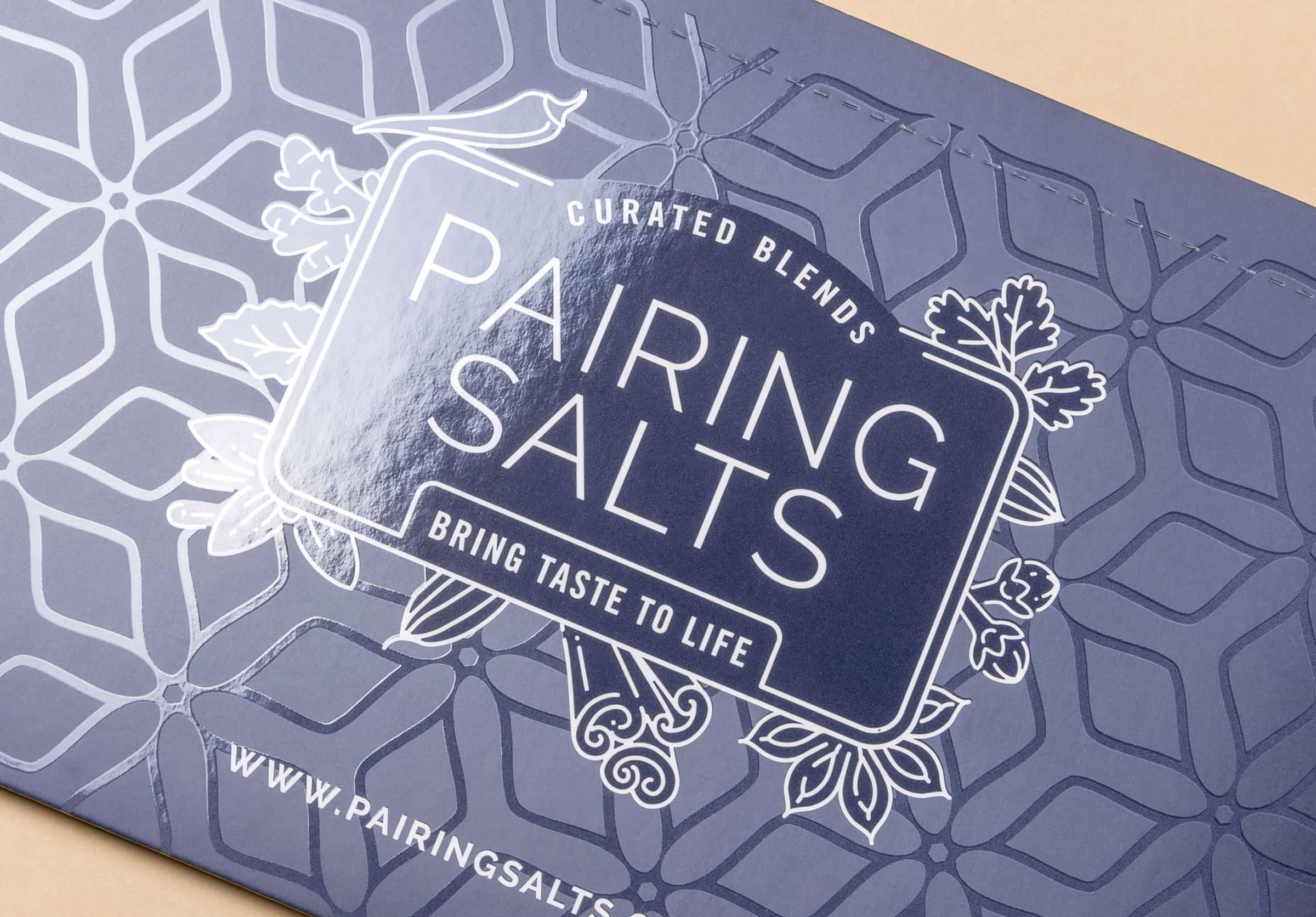
Source: PakFactory
Regarding paperboard packaging, finishes play an equally essential role as the chosen paper grade. Below are some of the popular finishes used in paper packaging:
Matte Finish: Matte finish paper packaging has a non-glossy and soft appearance, providing a sophisticated and premium look. It is often used in luxury packaging, including cosmetics, perfumes, and high-end food products.
Gloss Finish: Gloss finish paper packaging has a shiny and reflective surface, providing a sleek and modern appearance. It is commonly used in advertising, magazine covers, and retail packaging.
Embossed Finish: Embossed finish paper packaging features a raised or recessed texture, creating a three-dimensional effect. It adds depth and texture to packaging, making it more eye-catching and memorable.
Foil Stamping: Foil stamping involves applying metallic or colored foil to paper packaging, creating a luxurious and elegant look. It is often used in premium packaging for chocolates, wines, and other high-end products.
Spot UV Coating: Spot UV coating involves applying a high-gloss finish to specific areas of the paper packaging, creating a contrast between the glossy and matte finish. It highlights particular packaging areas, such as logos, text, or images.
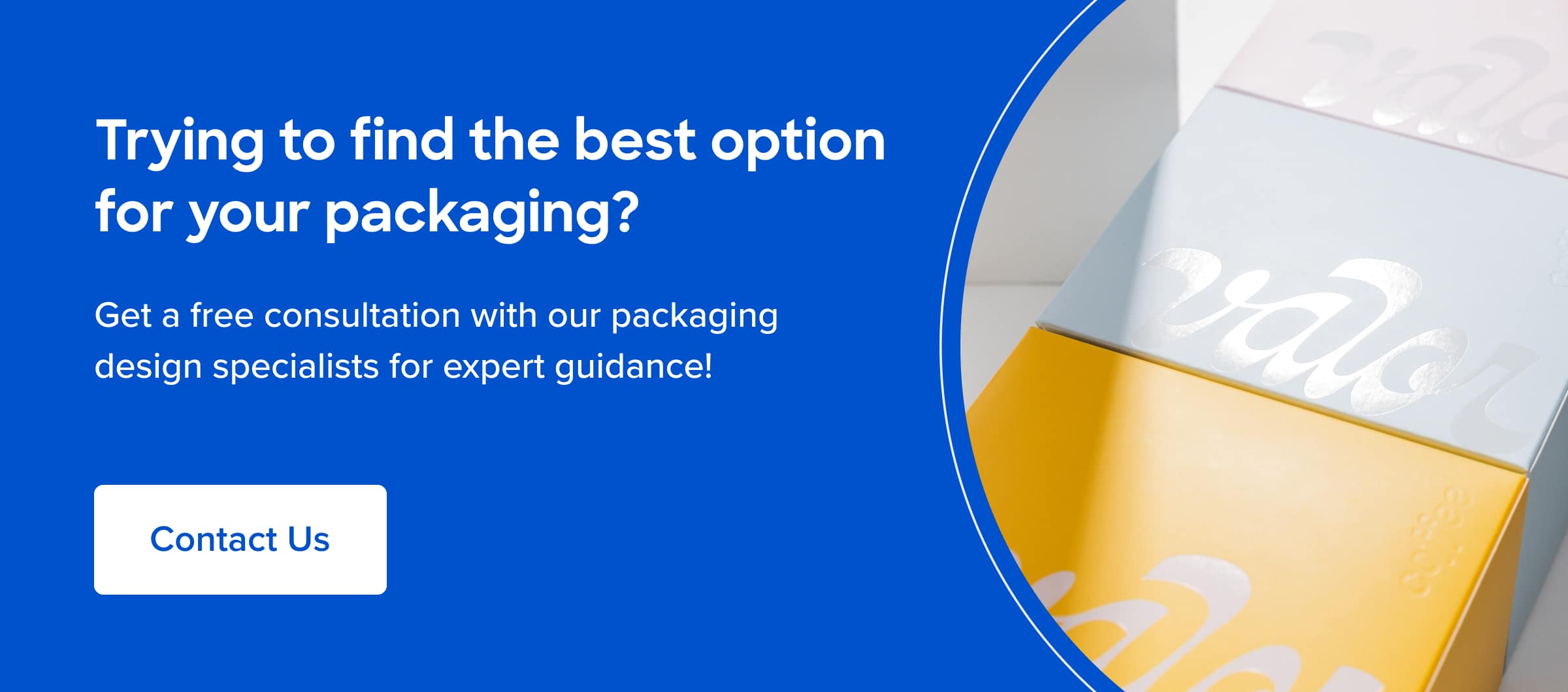
It Doesn’t End There…
To further understand the ideal paper grade for your packaging, it is crucial to understand the material’s durability, strength, and thickness. Understanding these specs will help create a suitable box based on the product’s weight and the structural design of the packaging.
Measuring the thickness of the paperboard is done by determining the PT/GSM of the material. Essentially, the higher the GSM/PT Unit, the thicker the material and the more weight it can carry.
Need help determining what material best fits your packaging and product? Contact one of PakFactory’s product specialists. We are more than happy to provide the help you need!