Table of Contents
When we talk about packaging, one of the aspects that are less explored is package thickness.
How thick or thin your packaging is can have an impact on its durability, protectiveness, and aesthetic appeal.
Understanding package weight and the different factors that need to be considered can help you design effective packaging that works for your product needs.
We’ll look at key terms used to describe packaging, the unit systems used, how to convert and compare units and weight as well as how that impacts your overall packaging.
We’ll first look at some definitions to help you understand how to determine cardboard thickness for packaging.
What are GSM unit and PT unit?
First things first, the common terms you’ll hear around packaging are PT and GSM so let’s break those down.
PT stands for point and GSM stands for grams per square meter.
If you’re thinking about GSM vs. PT, both terms are used to measure the packaging stock and to determine how much material stock is needed to create packaging tailored to your products’ needs.
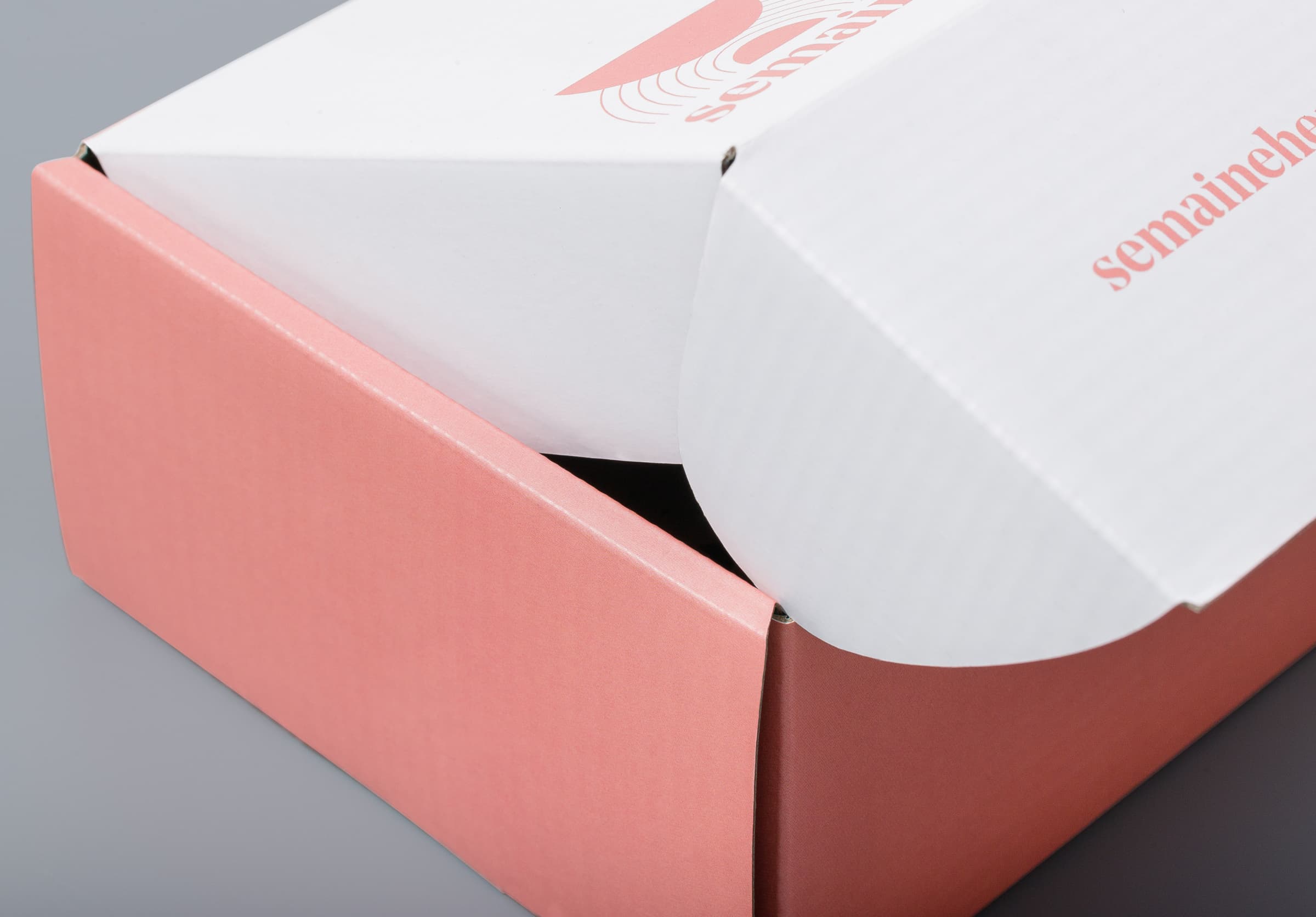
Source: PakFactory
Another measurement you’ll find is lb or pounds of the weight of the paper.
This is measured by using one ream (i.e., 500 sheets) before it is cut.
These are the basic units used in the context of packaging stock.
We’ll now take a closer look at each one individually to help differentiate between GSM and Point.
The Point System (PT)
As we’ve discussed before, points are used as a way to demonstrate the thickness of a sheet of paper, including packaging corrugated paper.
The thickness is measured using calipers, with each point representing 1/1000th of an inch.
As you browse packaging options, you’ll see that many use the point system to describe the thickness, such as 8 point and going up to 16 point.
The measurement that you see can help you determine how thick the stock is and give you a better idea of the protective qualities it has to offer.
The higher the PT the thicker.
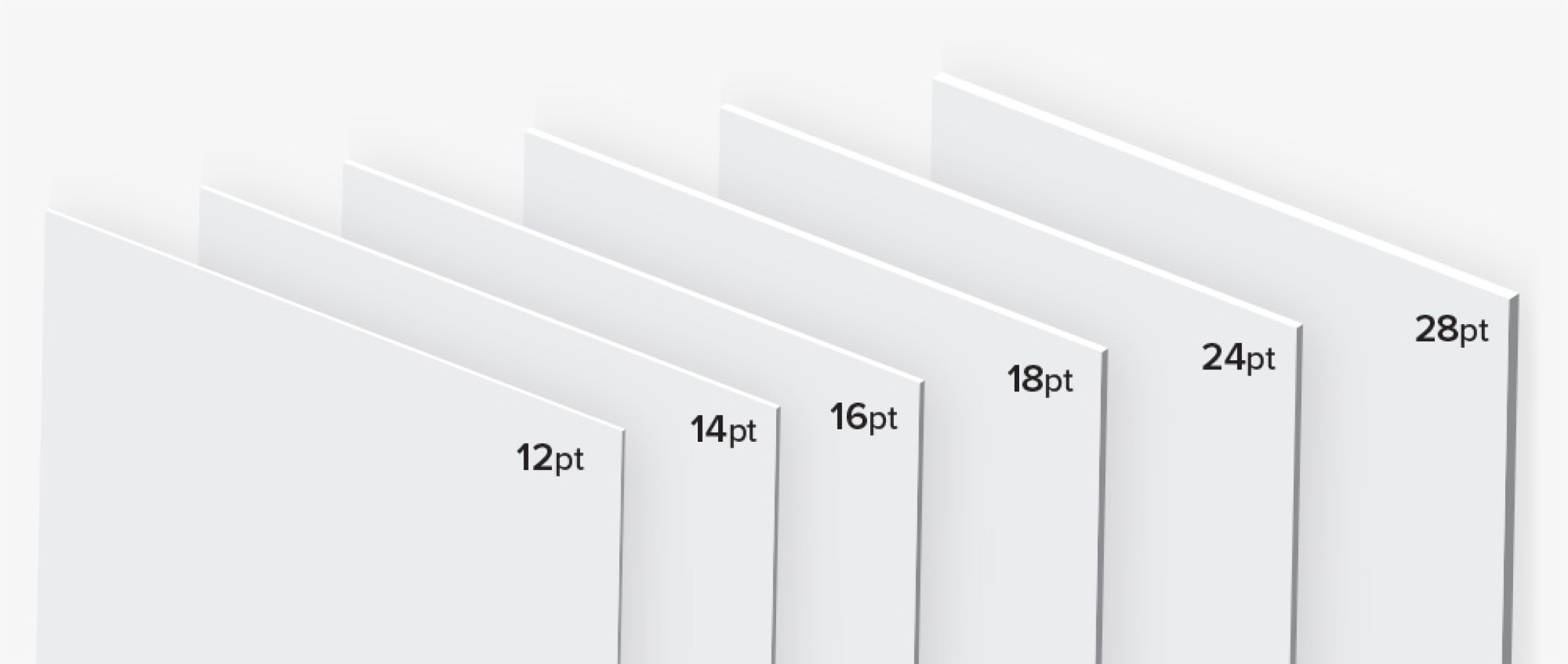
Source: PakFactory
Grams per Square Meter (GSM)
Grams per square meter (GSM) is essentially the metric equivalent of the point system as it uses centimeters and meters for its prime measurement.
It can be confusing as there is no straightforward way to convert measurements from one system to another.
This is because grams per square meter (GSM) looks at paper weight, length, and breadth rather than just the thickness and height.
Bear in mind that some packaging materials may seem thick, but that doesn’t necessarily mean they are heavier.
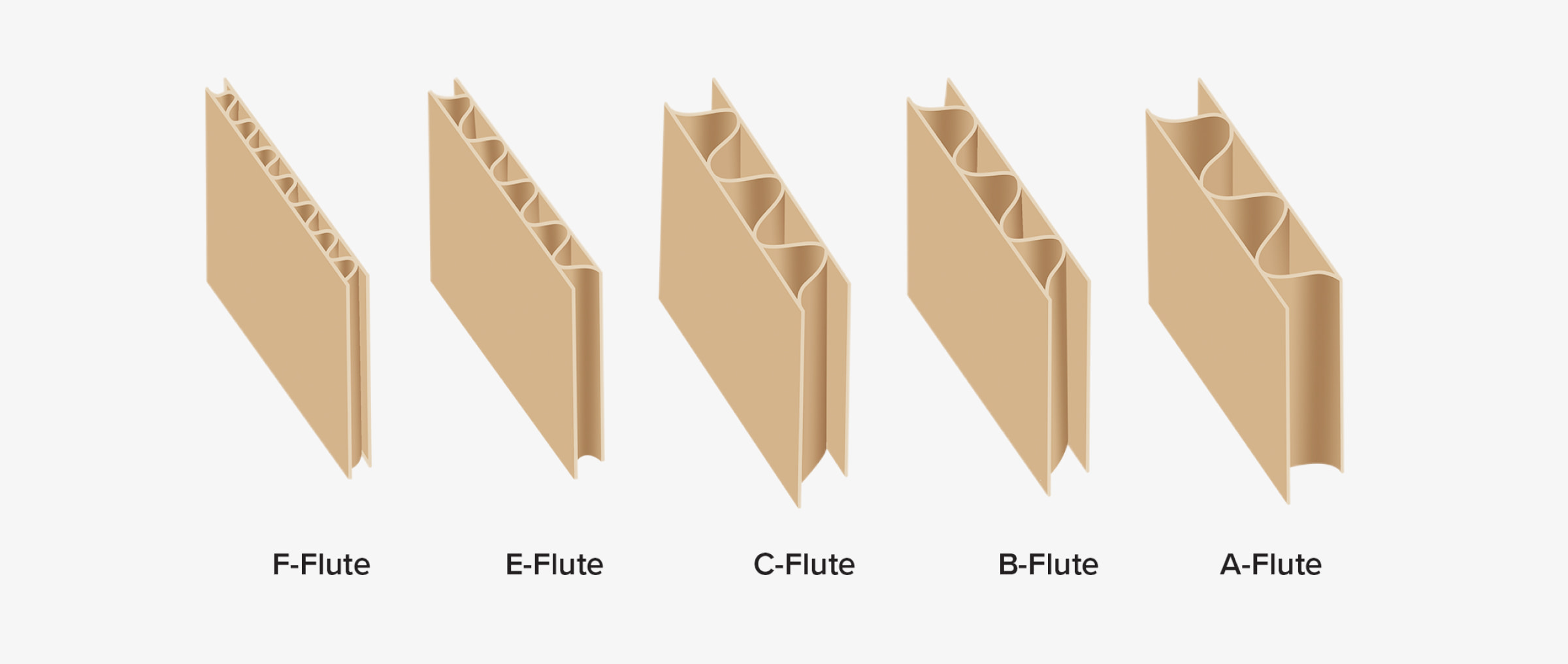
Source: PakFactory
For example, when you think about the corrugated thickness for packaging, you can have a corrugated fiberboard that feels thicker, but it won’t necessarily be heavier.
However, the higher the GSM unit is, the more thick and heavy the paper will be with GSM.
Generally, high-quality paper tends to have a higher GSM since it’s more durable, and images tend to look better when printed on.
Why is the GSM Unit System Important?
GSM is so crucial because it’s what is generally more in use, so it’s easier to communicate with vendors using this system.
Aside from its ease of use, GSM holds more importance because it conveys more information.
It takes paperweight into account, which is a significant factor when considering packaging materials and costs.

Source: PakFactory
It’s also a more precise form of measurement for packaging thickness, enabling you to be more confident in your choice, making the design process more straightforward, and adding less confusion to your packaging journey.
So what are some common measurements you might see when considering GSM?
Understanding Common GSM Paper Thickness
Understanding common GSM paper measurements helps you in your decision-making process.
You can choose the right thickness and heaviness based on your packaging’s look and feel and how durable you need the packaging to be.
35 – 55gsm: This is the paper that most newspapers are printed on. |
90 – 100gsm: This is a normal printer/copier paper. Something more premium, like bond paper, would be in the region of 110-120gsm. |
120 – 140gsm: Flyers and posters tend to be printed on this paper because it is stronger and can resist some wear and tear. |
210 – 300gsm: If you have seen and experienced glossy brochures, you know what this paper feels like. |
350 – 400gsm: Used for mainly packaging & business cards |
So once you know what GSM you’re looking for, you can start to switch between it and the point system if needed. Here’s how.
Converting Between the GSM and PT Unit System
Because GSM is essentially the metric version of the PT system, you can use it for calculating thickness. Because GSM takes weight into account, you cannot use them interchangeably.
Here are conversion charts available to help switch between the two as needed when thinking about the paper in pt vs. gsm and what you need.
Having accurate conversions can be helpful in the design process depending on what your packaging vendor works with, and it helps to provide as much information as possible.
Thickness / Packaging Material | Weight |
13 point Pulp | 200 gsm |
14 point Uncoated | 270 gsm |
16 point C2S / Solid Bleached Sulfate (SBS)* | 350 gsm |
18 point C2S | 400 gsm |
24 point Uncoated | 405 gsm |
24 point C2S / Solid Bleached Sulfate (SBS)* | 460 gsm |
40 point Cotton | 600 gsm |
As you can see, more thickness does not simply translate into more weight. A 17-point uncoated surface packaging material weighs 350gsm, but the thicker 18-point brown Kraft weighs only 315gsm.
Apart from paper, other packaging materials are used, such as corrugated board (there are various types like single face, single wall, double wall, and triple wall – and all of them have different gsm).
Now that you have an idea of the conversion process, we’ll explore comparisons between paper weights and thickness.
How to Compare Paper Weights and Thickness
Although the systems can be confusing between the US and metric, the core thing to remember is that the GSM system includes weight as part of its measurement for paper.
Knowing your packaging material’s weight and thickness is particularly helpful when measuring corrugated paper thickness and cardboard thickness for packaging.
The thickness and weight can help you choose the best packaging thickness that will give your customers a great unboxing experience and is durable enough that it won’t get damaged during long transit and shipping.
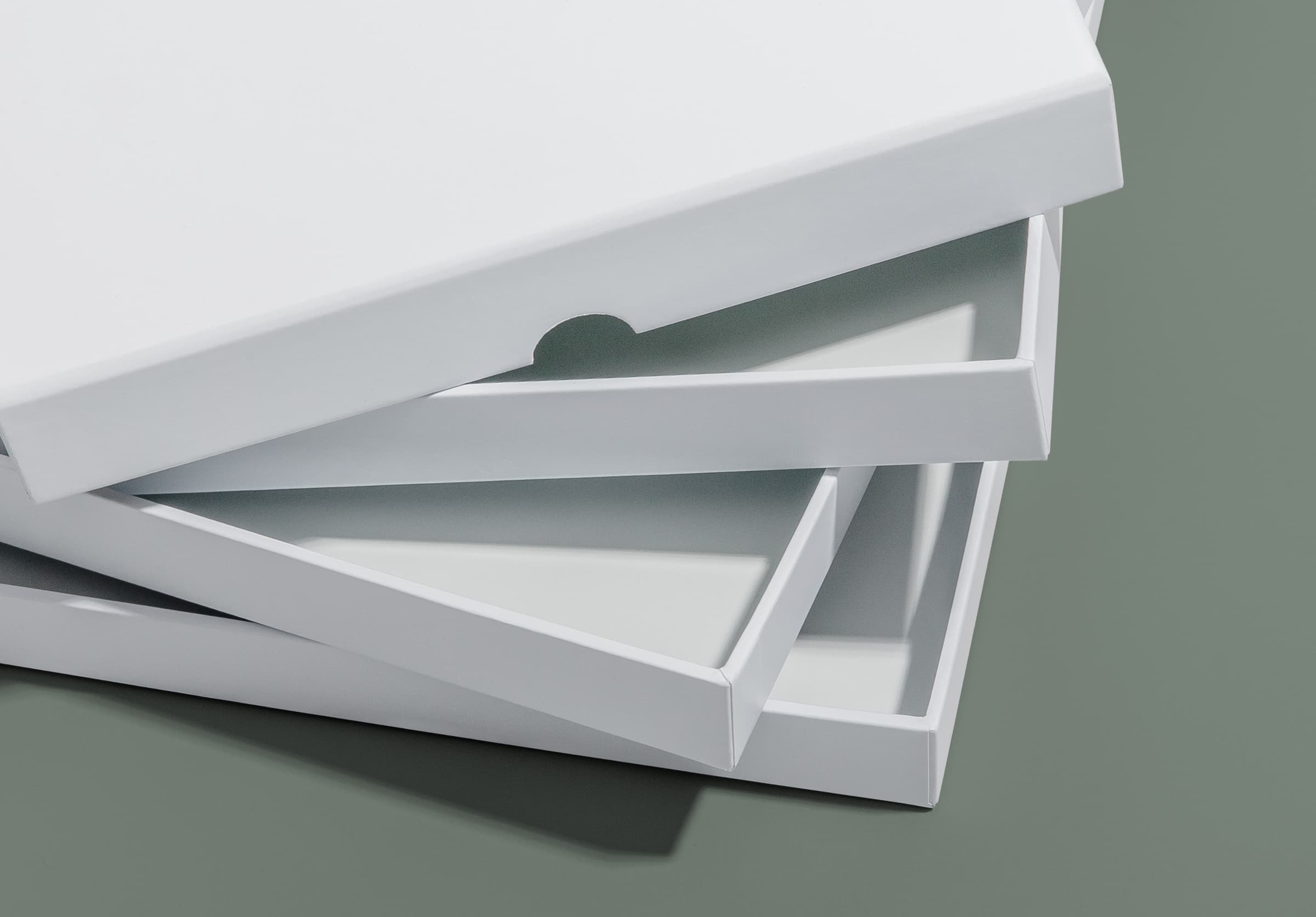
Source: PakFactory
You can work with packaging experts to better understand the pros and cons of different weights and thicknesses and how that will affect your packaging material cost and shipping charges.
For more tips and tricks all about packaging, check out our Essential Guide to Product Packaging and our Beginner’s Guide to Designing E-Commerce Packaging.
We’ll now look at what all of these different measurements mean for your packaging.
The Implications for Packaging
So now that you’ve seen the different ways to measure weight and packaging thickness, how do you implement this in your packaging materials?
The first thing is to differentiate between packaging materials during the design process and look at materials objectively.
The paper thickness pt vs. gsm will help you determine the best packaging for your product that will get to customers intact.
The other vital reason for these measurements is that you begin to get an idea of the final packaging product’s look and feel.
Will it feel thick and heavy when customers receive it, or do you want a lighter, air-like feel?
Will there be images or logos printed on the packaging? You might need a higher GSM as images will print in higher quality due to the surface texture.
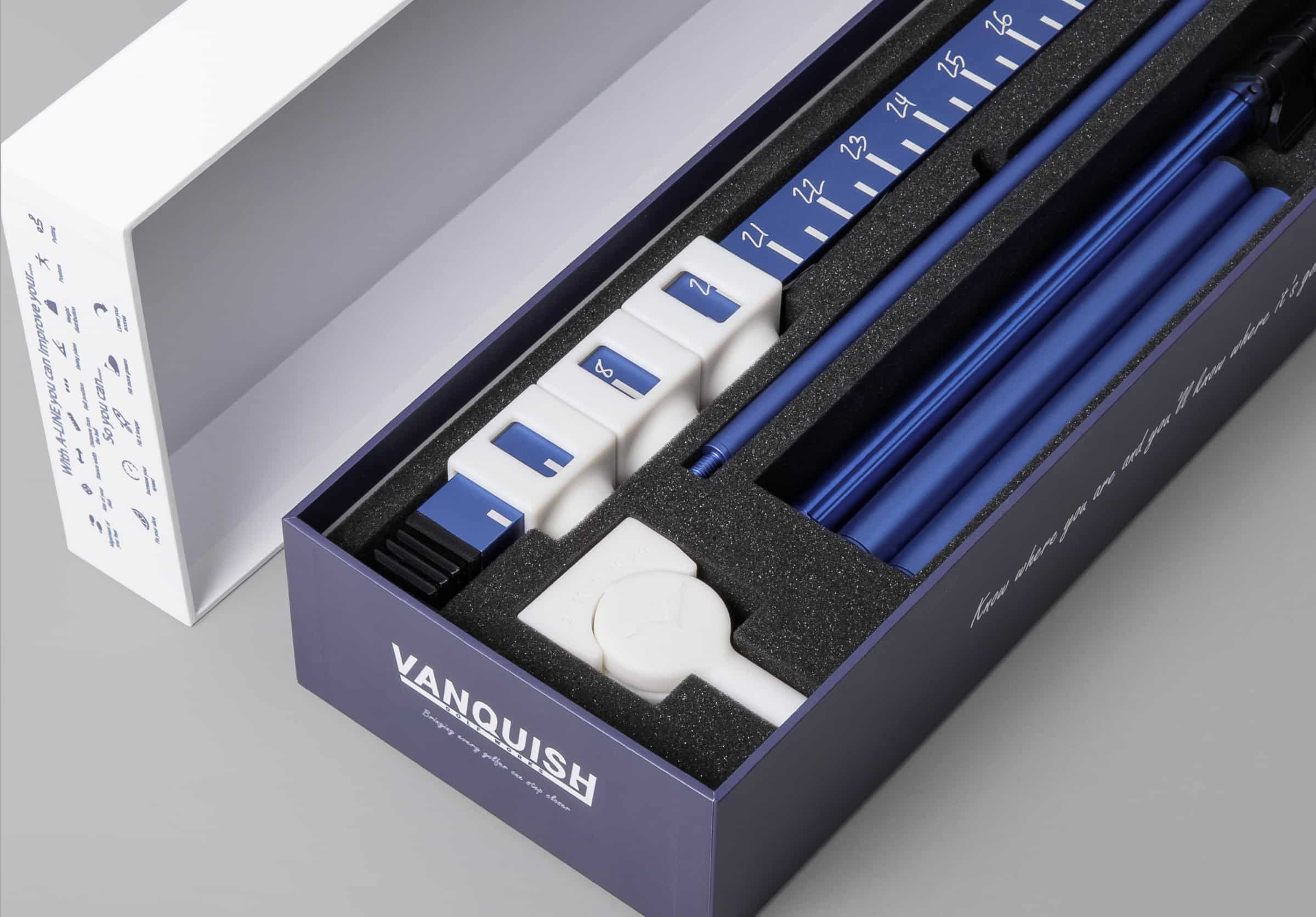
Source: PakFactory
There are also decisions to be made on the finishing of your packaging. Are you going for a matte or glossy finish? This too is dependent on the GSM of your packaging material!
Ultimately, the GSM unit system is a way for you to communicate with design experts and create a packaging experience that is truly authentic to your brand.
If you’re unsure about what works and what doesn’t, talk to a packaging design expert!
They can help break down the GSM system and advise you on choosing your packaging thickness to create a consistently amazing customer experience every time.