Table of Contents
Varnish is a popular finishing technique used in the packaging and printing industry to provide an additional layer of protection and enhance the visual appeal of printed materials.
It is a clear liquid that is applied to the surface of printed materials, offering a barrier against external factors such as dust, dirt, and moisture.
Varnish also improves the tensile strength of paper-based packaging, making it more durable during shipping and handling.
With various types of varnishes available, each with unique properties and benefits, it is a versatile and essential tool for designers and printers to elevate the quality and durability of packaging and printing materials.
Types of Varnish
When it comes to choosing the right varnish for your packaging, it’s important to understand the different types available in the market.
Each type of varnish has unique properties that can affect the look and feel of your packaging, as well as its level of protection.
Here are most varnishes used in packaging:
Gloss Varnish
Gloss varnish is a popular choice for packaging designers because of its ability to create a high-gloss finish that enhances the overall aesthetic of the packaging.
This type of varnish is typically applied to the entire surface of the packaging or selectively to specific areas to highlight certain design elements.
The glossy finish can make colors appear more vibrant and can give the packaging a luxurious, premium feel.
One advantage of using gloss varnish is its ability to protect the packaging from damage, such as scratches or scuffs.
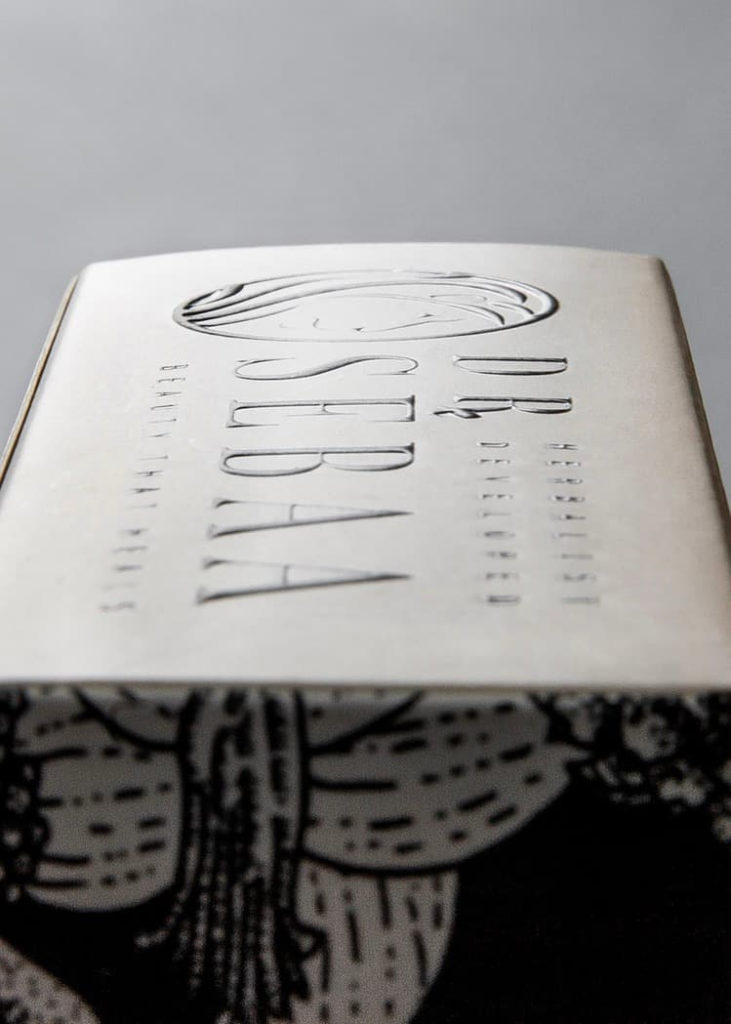
This is especially important for packaging that will be handled frequently or transported over long distances.
The varnish creates a protective barrier that can help to extend the life of the packaging, ensuring that it looks great throughout its entire use.
Gloss varnish is also a versatile option because it can be applied to a wide range of substrates, including paperboard, plastic, and metal.
It can be used for various packaging applications, such as food and beverage packaging, cosmetic packaging, and electronic packaging.
However, one downside of gloss varnish is that it can sometimes create unwanted reflections or glare, making it difficult to read text or see images on the packaging.
It may not be the best option for packaging that needs to be legible or easily visible under bright lights.
Matte Varnish
Matte varnish is a popular alternative to gloss varnish because it creates a non-reflective finish that gives packaging a more subdued, understated look.
It is a great option for designs that require a softer, more muted appearance. Matte varnish provides a protective barrier to the packaging, making it less susceptible to scratches, smudges, and other types of damage.
One of the benefits of using matte varnish is that it can be used to create contrast and depth in packaging designs.
It works well when combined with other finishes, such as gloss or spot varnish, to create visual interest and highlight specific design elements.
Additionally, matte varnish can be used to create a tactile effect by creating a textured finish on the packaging.
Another advantage of matte varnish is its ability to reduce glare and reflections, which can be helpful when the packaging needs to be viewed under different lighting conditions.
For example, matte varnish is often used on packaging for consumer electronics to reduce glare and make the product more visible in store displays.
Matte varnish is also a versatile option that can be used on a variety of substrates, including paperboard, plastic, and metal.
It can be used for various packaging applications, such as food and beverage packaging, cosmetic packaging, and luxury goods packaging.
However, one downside of matte varnish is that it can sometimes be prone to scuffing and may not hold up as well over time as gloss varnish.
Additionally, matte varnish can be more challenging to apply consistently than gloss varnish, which can make it more expensive.
Soft-Touch/Satin Varnish
Soft-touch varnish, also known as velvet or suede varnish, is a specialty type of varnish that creates a luxurious, tactile finish that is soft to the touch.
It is a popular choice for packaging designers looking to add a premium feel to their packaging and create a memorable unboxing experience for the consumer.
Soft-touch varnish is often used for high-end cosmetic, fragrance, and fashion products, where the packaging is an essential part of the overall brand experience.
One of the key benefits of soft-touch varnish is its ability to create a tactile sensation that engages the senses of the consumer.
The velvety finish creates a pleasant and memorable unboxing experience that can leave a lasting impression on the consumer.
This effect is particularly important for luxury brands that want to create a sense of exclusivity and sophistication.
Soft-touch varnish can be applied to a variety of substrates, including paperboard, plastic, and metal, making it a versatile choice for many packaging applications.
It is also available in a range of colors, from neutral tones to vibrant hues, allowing packaging designers to create unique and eye-catching designs.
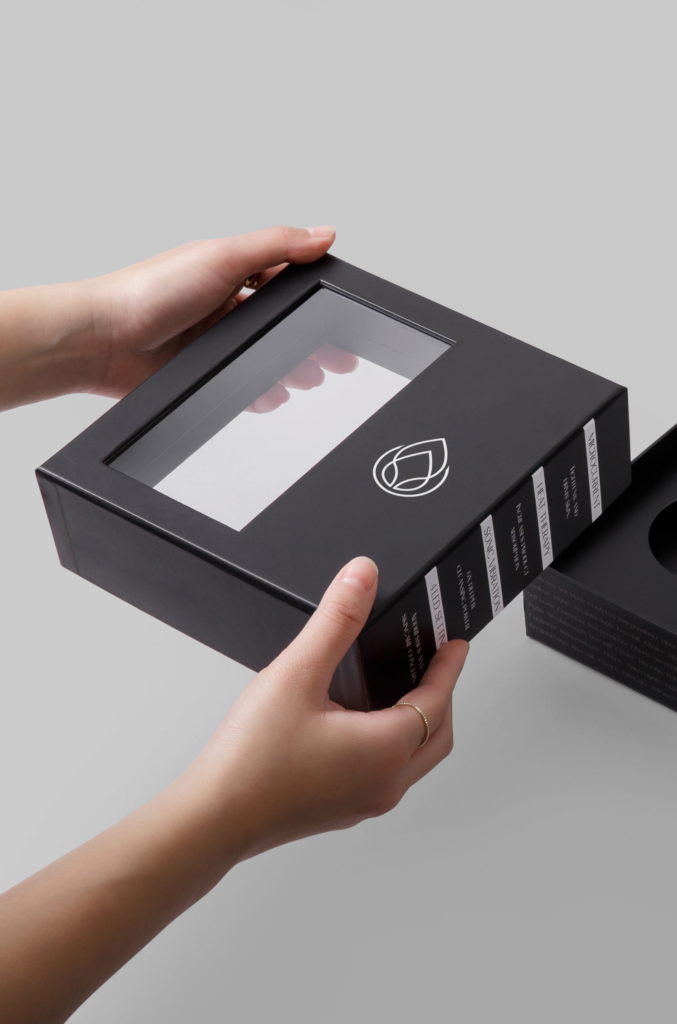
In addition to its aesthetic benefits, soft-touch varnish also provides a protective layer to the packaging, making it more resistant to scratches and other types of damage.
It can also improve the durability of the packaging by providing additional strength and rigidity.
However, one drawback of soft-touch varnish is that it can be more expensive than other types of varnish, which can be a concern for some packaging designers.
Additionally, it can be more challenging to apply consistently, which can result in variations in the finish.
The Varnish Process
The varnish process in packaging involves several steps to ensure a smooth and even application.
First, the packaging material is printed with the desired design using ink. Once the ink is dried, the varnish is applied using a printing press or a varnishing machine.
The varnish is spread over the surface of the printed material using a roller or spray nozzle, depending on the type of varnish used.
The varnish is then cured or dried, usually using heat or UV light. This process hardens the varnish and creates a protective layer on the packaging material, enhancing its durability and longevity.
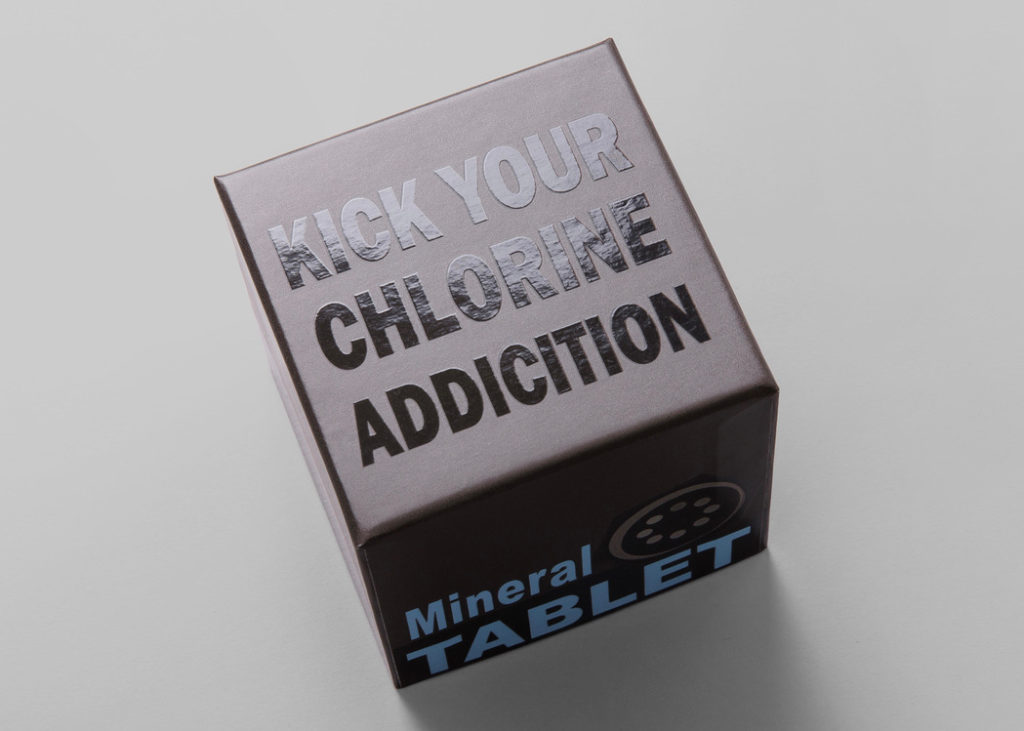
The end result is a beautifully finished product that is not only visually appealing but also offers protection against environmental factors such as water, scratches, and smudges.
Advantages and Disadvantages of Varnish
Advantages:
- Longevity: Varnish provides an added layer of protection to printed materials and packaging, making it more resistant to wear and tear, scratches, and other forms of damage. This ensures that the packaging remains in excellent condition throughout its lifespan.
- Resistance to environmental factors: Varnish is resistant to water and other environmental factors, making it suitable for packaging that may be exposed to moisture or varying weather conditions.
- Cost-effective: Varnish provides a high-quality finish at a relatively lower cost compared to other finishing options, making it an economical choice for businesses looking to enhance their packaging.
- Versatility: Varnish can be applied to various substrates, including paper, cardboard, plastic, and metal, making it suitable for a wide range of packaging materials. This versatility allows designers to create customized and visually appealing packaging solutions to meet their specific needs.
Disadvantages:
- Limited range of finishes: While varnish can provide a range of finishes, such as glossy, matte, and soft-touch, it may not offer the same range of finishes as other finishing options, such as lamination.
- Longer drying time: Varnish requires a longer drying time compared to other finishing options, such as UV coating. This may slow down the production process and increase lead times.
- Difficulty in repairing: Once applied, varnish cannot be repaired or corrected. Any mistakes made during the application process may require the entire packaging to be redone.
- Not suitable for all applications: Varnish may not be suitable for all types of packaging or printing applications. For example, it may not be appropriate for packaging that requires a high level of flexibility or stretch
Considerations for Using Varnish
When using varnish in packaging and printing, there are several considerations to keep in mind.
One of the most important is compatibility with other printing and finishing methods. Some varnishes may not work well with certain inks or printing techniques, so it’s important to test the compatibility beforehand.
When considering the use of varnish in packaging, sustainability is a critical factor that should not be overlooked.
Sustainable Varnish Considerations
As consumers become more environmentally conscious, brands are looking for ways to reduce their environmental impact and meet consumer expectations.
Here are some considerations for using varnish on packaging, with a focus on sustainability:
- Use eco-friendly varnishes: Some varnishes are made with sustainable and biodegradable materials, making them a better choice for the environment. Look for varnishes that are certified by organizations like the Forest Stewardship Council (FSC) or use plant-based materials.
- Minimize varnish usage: Using varnish on the entire surface of the packaging is not always necessary. Consider using spot varnishing, which only applies the varnish to specific areas, reducing the amount of varnish used and the environmental impact.
- Choose recycled materials: Varnish is often used on paper-based packaging. Using recycled materials for packaging reduces the demand for new materials and helps to conserve natural resources.
- Avoid over-packaging: Over-packaging not only wastes resources, but it also requires more varnish to protect the product. Opting for minimalistic packaging designs can help reduce the need for excessive varnish and other finishing methods.
- Proper disposal: Disposing of varnish can be harmful to the environment. Ensure that the varnish is properly disposed of, and avoid releasing it into the environment.
- Consider alternative finishing methods: While varnish is a popular finishing method for packaging, other options such as water-based coatings or laminates can provide similar benefits with a lower environmental impact.
It is important to consider the environmental impact of using varnish, and take steps to minimize any negative effects.
By using eco-friendly varnishes, minimizing usage, choosing recycled materials, avoiding over-packaging, properly disposing of varnish, and considering alternative finishing methods, we can create more sustainable packaging solutions that meet the needs of both consumers and the environment.
In conclusion, varnish is a versatile and essential tool in the packaging and printing industry that provides an added layer of protection and enhances the visual appeal of printed materials.
There are several types of varnishes available, each with its own unique properties and benefits.
Using varnish in packaging and printing has several advantages, such as increased durability and longevity, resistance to water and other environmental factors, cost-effectiveness compared to other finishing options, and versatility in application.
However, it’s important to consider the potential disadvantages, such as the need for proper handling and storage to avoid contamination, compatibility with other printing and finishing methods, and potential health hazards associated with varnish application and use.
With the right considerations and safety measures in place, it can be a cost-effective and versatile finishing option for a wide range of packaging and printing applications.
