Table of Contents
UV coating is a clear liquid applied to paper substrates and then cured using ultraviolet light for a high gloss-like surface effect.
The UV coating process is done after printing using a UV coating machine.
UV coatings have the capability to bring your artwork designs to life and add a sleeker look to your final packaging design.
Let’s jump into what the UV process entails and how you can implement it into your custom packaging project.
The UV Coating Process
UV coatings are one of the most popular finishing processes for packaging.
It is a clear liquid compound and includes the following ingredients to ensure it is strongly bonded to the surface of the packaging.
- Calcium
- Carbonate
- Kaolinite
- Polyethylene
The liquid compound is applied using a silkscreen or a roller to generously distribute the coating across a surface.
Once the wet coating is applied, it is cured using ultraviolet light, and in a matter of seconds, the coating is completely dry.
UV coatings are water-resistant, making them a common choice for protecting the durability of packaging surfaces.
The UV coating can be applied to all box surfaces or only to specified surfaces; the choice is yours!
What is Spot UV?
Spot UV printing uses the same liquid compound as the UV coating would.
The only difference is that rather than generously applying the coating to the surface of packaging, it is only applied to specified areas.
This could include, logos, text or images.
Spot UV helps bring more dimension to packaging designs by highlighting important elements.
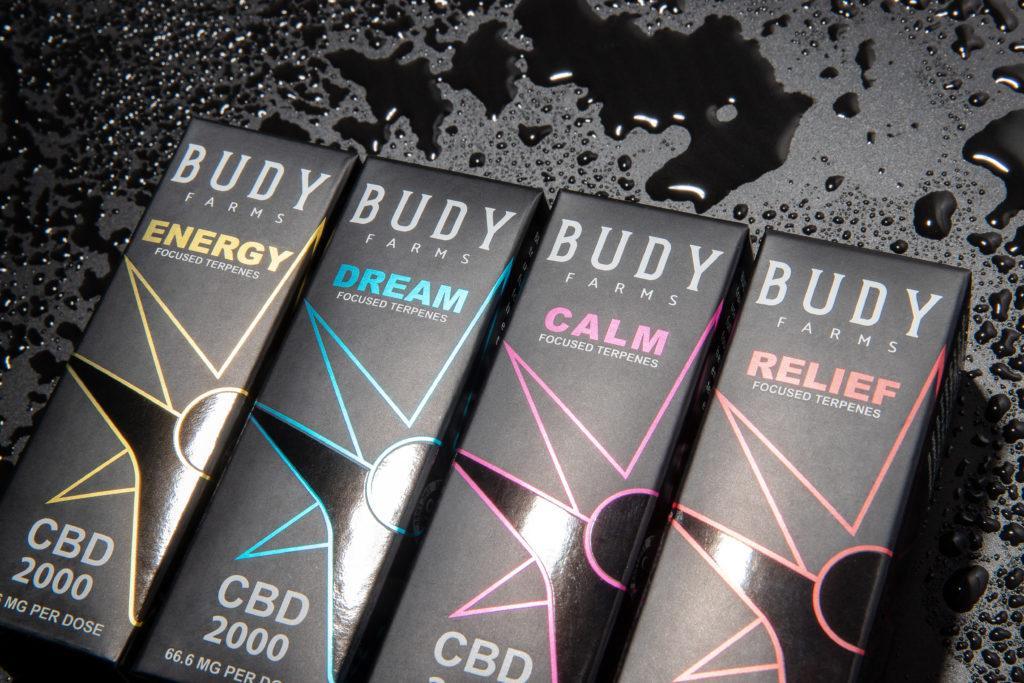
What Are the Common Uses of UV Coating?
UV coatings are a versatile technique utilized for all types of paper products.
However, it works best for thicker and heavier weights of paper such as rigid set-up boxes and corrugated packaging.
UV coatings do a wonderful job at enhancing art work designs and really bringing them to life.
That’s why you’ll most likely see this finish applied to luxury packaging for an added high-quality feel.
Similarly, the e-commerce industry have been using this coating technique more often to enhance the tensile strength of their packaging in transit.
Types of UV Coating
Depending on the appearance and feel you wish to produce with your UV coated printed boxes, you can consider the following solutions:
Gloss UV
Gloss UV, as the name suggests, provides the glossiest of all coatings.
If you’re looking for brilliant gloss and a beautiful patina, gloss UV is a good option.
To avoid creating a highly reflective (and therefore less legible) surfaces and an over-the-top shine, you may want to reserve gloss UV coatings for spot UV printing.
Matte UV
Matte finishing gives off a feeling of elegance and luxury.
Matte spot UV can be applied to specific areas that you wish to highlight as well.
Alternatively, you can opt for flood protective UV, which covers the entire sheet and imparts a rich, vivid effect.
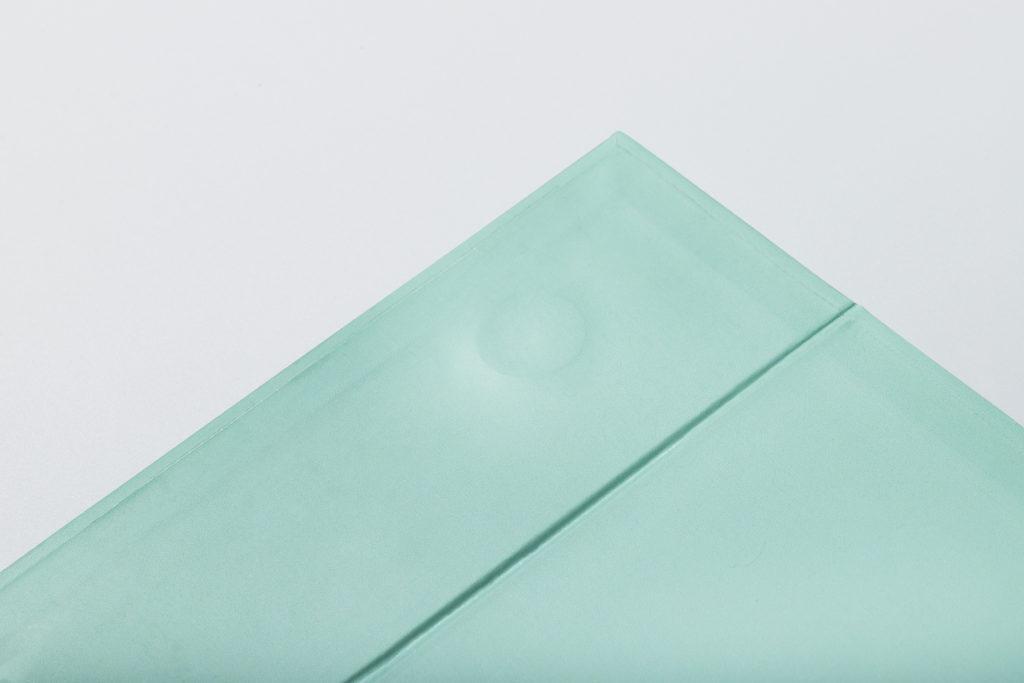
However, as matte UV is prone to fingerprints, it may not be the right choice for all products.
Pearlescent UV
This type of coating provides a lustrous pearlescent glow.
It combines Gloss UV coatings with metal flecks in different colors to achieve this effect.
It gives off an iridescent finish commonly used for cosmetics packaging.
Orange Peel UV
Combining a raised design with a textured finish, orange peel UV creates visual interest and unique tactile experience.
The textured finish adds a sensory element to your packaging that is not only eye catching but fun to handle.
Advantages and Disadvantages of UV Coating
There are several advantages and disadvantages of using UV coating:
Advantages
- Striking & bold: The ultraviolet coating creates a high gloss, vibrant finish that can significantly enhance the visual appeal and perceived value of the packaging or product.
- Scuff resistant: It also offers a higher level of scuff resistance in comparison to aqueous coatings and varnishes. UV coated items resist abrasion quite impressively, though the type of coating will also influence the smudge resistance.
- Fast drying: Quick-drying helps ensure a reduction in lead time and a more efficient process overall.
Disadvantages
- Chemical burning: Depending on the PMS color used, UV coating can be susceptible to chemical burning.
- Compromised quality and appearance: If the process of printing is not set-up properly, the output of the print may come out a bit defective.
Overall, UV coating provides a sleek and premium appearance to the print quality of your product and is an excellent choice if you want to make a striking first impression.
For alternative coating options, you can also check out: Varnish & AQ coating or discuss your options with our product specialist and get expert advice on your packaging solutions.