Table of Contents
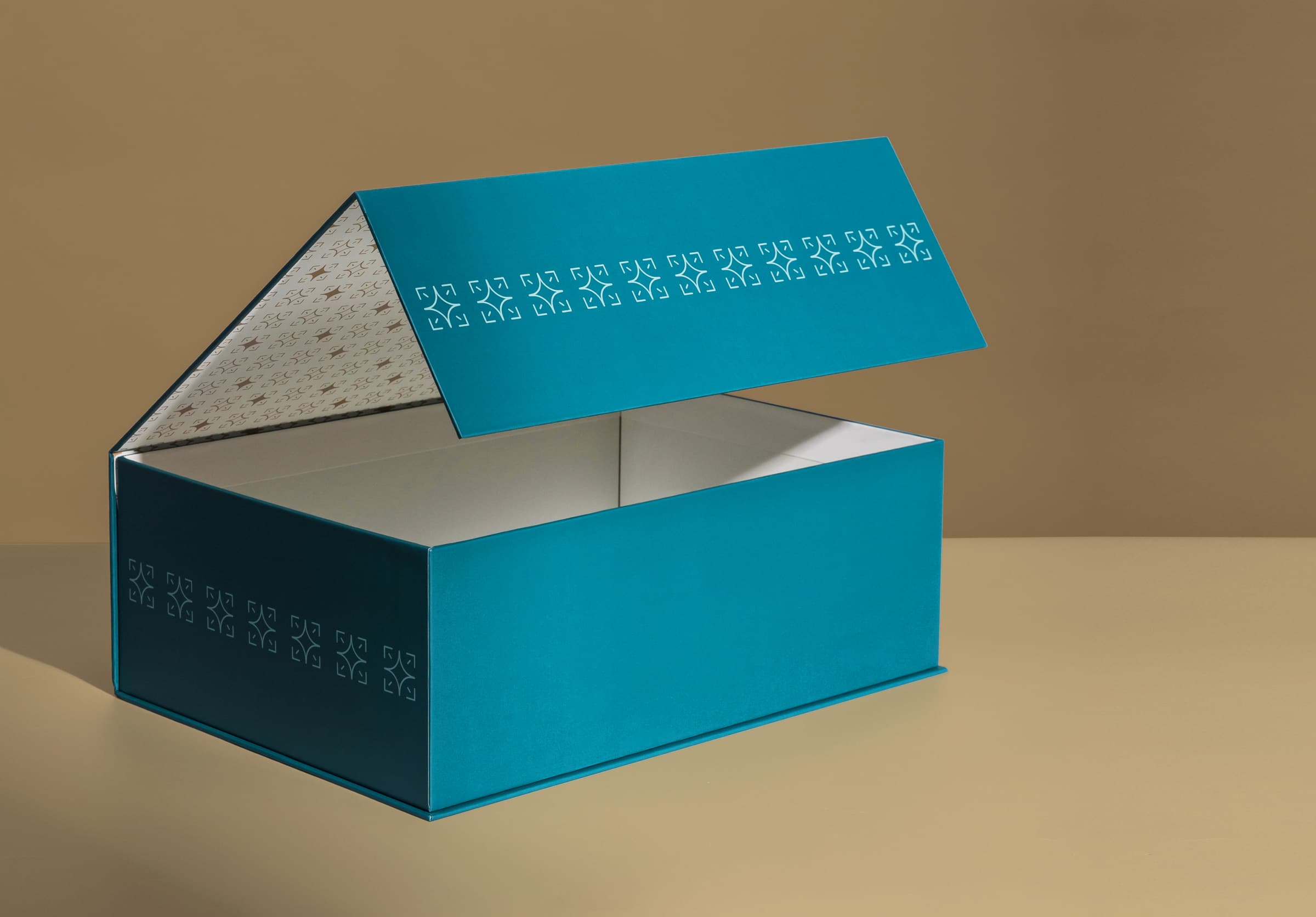
Source: PakFactory
Creating a lasting impression on your target market involves having attractive product packaging with a distinct “wow” factor. In that regard, the print coating is one of the most critical packaging elements you need to be aware of if you want your packaging to look its best despite multiple individuals touching and handling your products.
Whether used for packaging boxes, calendars, manuals, or other applications, the coating impacts the final look and appeal of the product.
And while each company has its own set of needs, to get you started, let’s look at one of the most popular coatings available: Aqueous (AQ) coating. But before we delve deeper into this excellent finishing method, you might wonder why you should apply a print coating to your project.
When to Coat?
Regardless of which coating you’re considering, in most cases, it will help protect and enhance your final product. If you intend to mail your piece, a print coating is necessary. And if you predict many hands will handle your print like a business card or brochure, a print coating is highly recommended for its added protection.
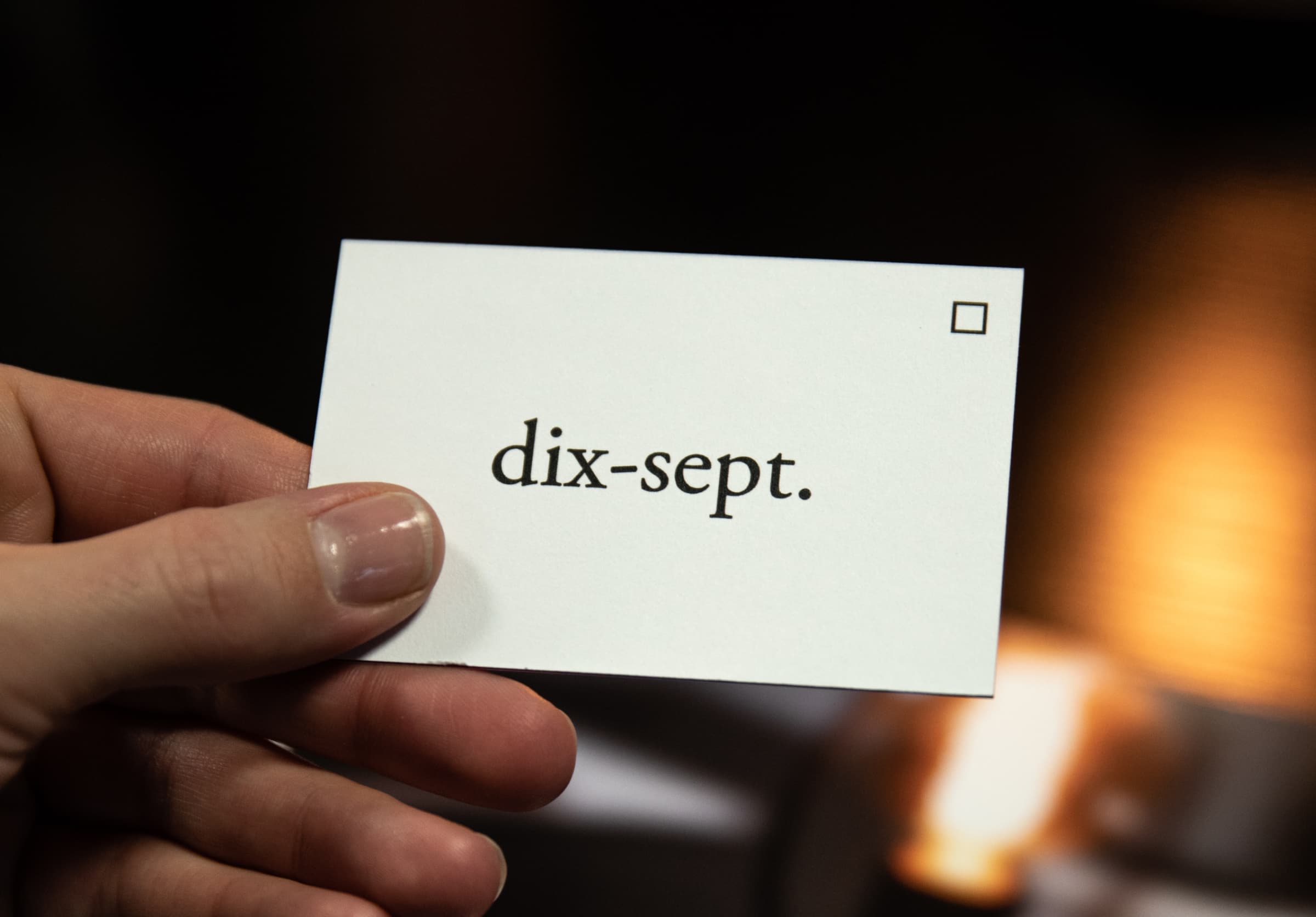
Source: Unsplash
However, sometimes your printed piece might be hindered by a print coating. Greeting cards, for example, do not need a coat, as applying one would make writing on the card challenging, defeating the intended purpose of your greeting cards! Still, if you wish to add a print coating to these items, you must specify with your service provider the areas where a coat should not be applied to avoid this problem.
But now that you know when is a good time to use coatings, let’s get back to the main topic at hand.
What is Aqueous (AQ) Coating?
Unlike UV coating and varnish, AQ coating is water-based and is known as the “default” coating for printing and packaging. It features fast-drying capabilities when used during the printing process, which makes it possible to achieve different appearances, allowing various application methods.
In addition to this versatility, AQ coating is known for being environmentally friendly with its non-toxic, water-based solvent that makes it perfect for applications such as:
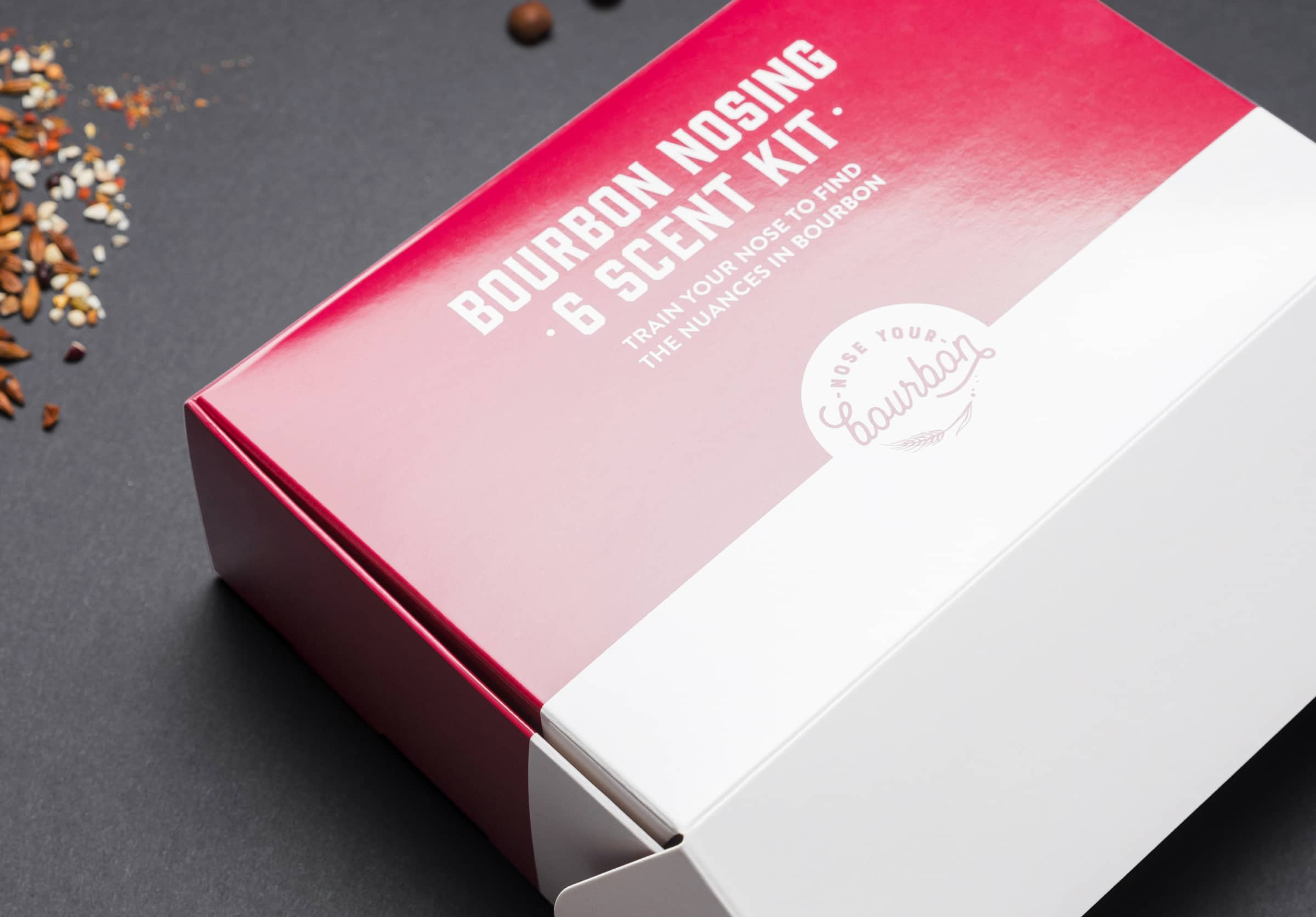
Source: PakFactory
AQ coatings are also resistant to fingerprints and other impurities during handling, and it is also possible to enhance surface durability with a combination of different coat layers. However, the product type will largely determine the suitability of AQ coating for your packaging.
Remember that though this coating is water-based, it does not mean it is waterproof!
Cosmetic products and perfumes, for instance, contain chemicals that may make AQ coating challenging to maintain on the exterior or interior of the packaging due to the risk of leaking, so always consider the product and your needs when deciding on the best print coating for you.
To help you better determine this, we have included some key differences and features between the popular options of AQ coating, UV and varnish.
AQ Coating | UV Coating | Varnish | |
---|---|---|---|
Coating Area | Flood coating only | Flood or spot coating | Flood or spot coating |
Drying Speed | Fast drying | Instant drying | Longest drying time |
Solution Base | Non-toxic water based | Chemical based solvent | Water or chemical based solvent |
Yellowing | Less likely to yellow | Do not yellow | Yellowing may occur |
Finishing | Matte, satin, gloss | Matte, gloss | Matte, satin, gloss |
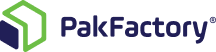
- Aqueous Coating
- It is only available as a flood coating that covers the entire printed material.
- It uses a fast-drying water-based solvent, typically making it the most cost-effective option.
- The non-toxic water-based solvent also makes it environmentally friendlier.
- AQ is durable and provides excellent protection from scratches, fingerprints and scuffs. It is also less likely to yellow than varnish and more flexible than UV coating, which can crack when folded or creased.
- Can have a matte, satin, or glossy finish.
- UV Coating
- Available as a flood or spot coating, which allows highlighting of specific parts of your printing project.
- It uses a chemical-based solvent containing polyethylene (plastic) or calcium carbonate, which is less environmentally friendly than AQ coatings.
- As the name suggests, this option uses ultraviolet light to dry and harden the finish near instantly.
- Like AQ coating, UV can have a matte to glossy finish, but overall, UV coating results in a shinier finish than AQ. Some find the finish too shiny, but this shine can really make images pop.
- UV Coatings are chemical and water-resistant and do not yellow over time. They offer the most protection over the other options.
- Varnish
- Varnish is available to flood or spot coat. However, they are heavier-bodied, meaning they can only be applied to specific areas via press-plate, and detailed artwork must be sent to the service provider prior to the job.
- Uses a clear liquid that can be UV or aqueous-based to cover the surface of printed material in a manner similar to an ink printing press.
- Varnish uses UV light or heat to dry but takes much longer than the other options.
- Varnish is also available in matte, satin, or gloss finishes.
- Varnishes protect your printed piece very well, but yellowing may occur. Areas not varnished are more susceptible to yellowing over time.
If the other options seem more appealing to your printing project needs, please visit our UV coating or varnish articles to learn more. If not, then let’s continue our journey into aqueous coatings!
The Benefits of Aqueous Coating
We’ve briefly mentioned the benefits AQ coating has over the other popular finishing methods, but let’s look at the four main benefits in more detail to understand why so many companies choose this option.

- Non-toxic & environmentally friendly: The treated paper is easily recyclable and does not produce harmful by-products. After applying the aqueous coating, there is minimum solid waste, and the cleaning process does not require toxic cleaning agents.
- Versatile: It is a no-hassle solution when additional finishing is necessary to the print and works well with various printing processes. The coating also makes it very easy to write and print over the coating for more variety in finishes.
- Cost-effective: This water-based coating is mainly used in line with the printing process, delivering significant cost savings.
- Durable and long-lasting: By sealing the ink against exposure to air, the coating maintains the fidelity of metallic inks. Aqueous coating is also less susceptible to yellowing, making it a better alternative to varnish.
Types of AQ Coatings
As mentioned previously, aqueous coatings are available in matte, satin or gloss finishes, but other unique coating types are also available to fit your printing needs! Let’s have a look.
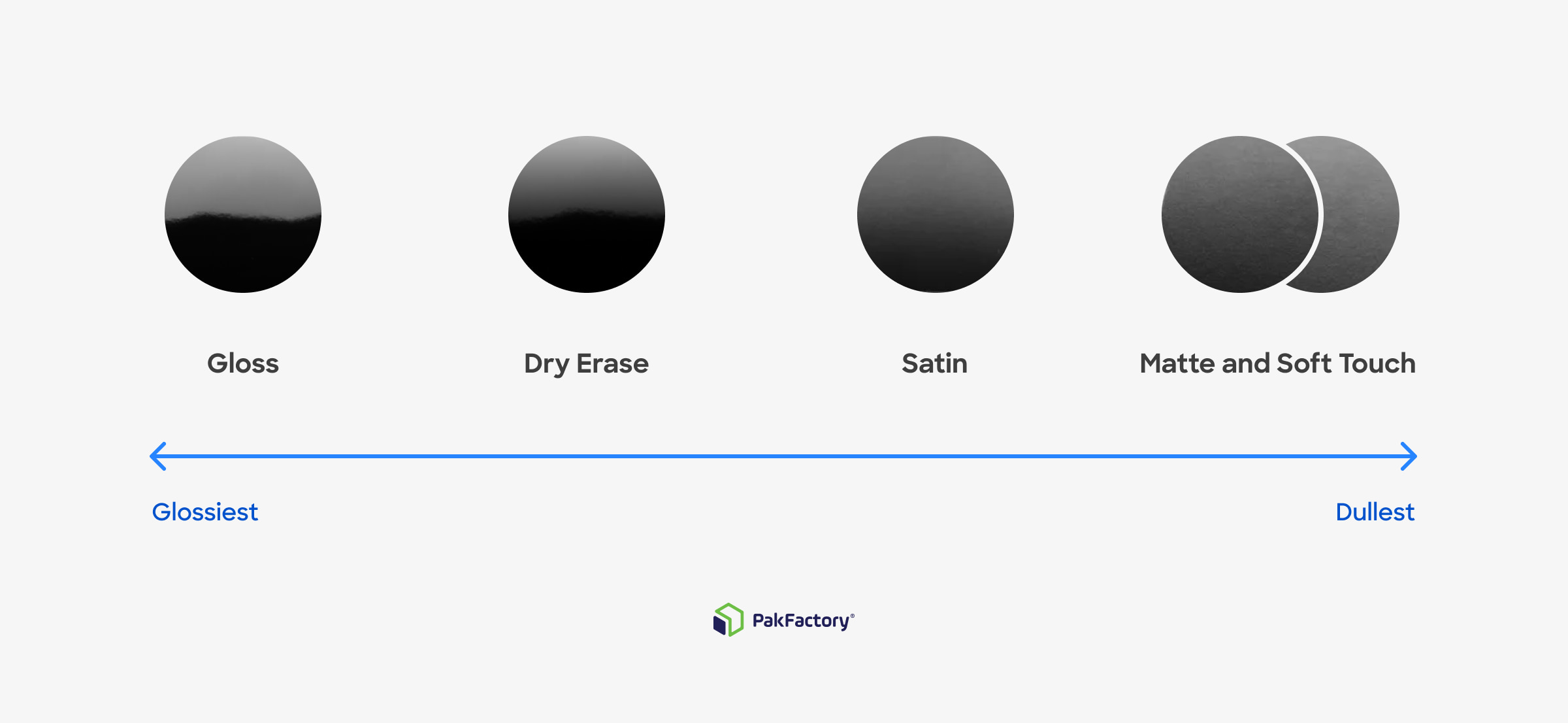
Gloss: A gloss aqueous coating is ideal if you’re looking for a less showy and more muted finish. As mentioned above, UV coating or film laminates are better options if you are looking for a flashier shine.
Dry erase: An alternative to laminate, dry-erase AQ coating achieves a high gloss effect at a low price.
Satin: With an appearance between gloss and matte, a satin aqueous coating offers medium shine and excellent scuff resistance.
Matte: A matte aqueous coating offers minimal shine and depth but a high degree of color intensity.
Soft Touch: Soft touch aqueous coating creates a velvety texture with a soft appearance compared to a glossy finish. Similar to matte coating, it gives a subtle finish with little to no shine.
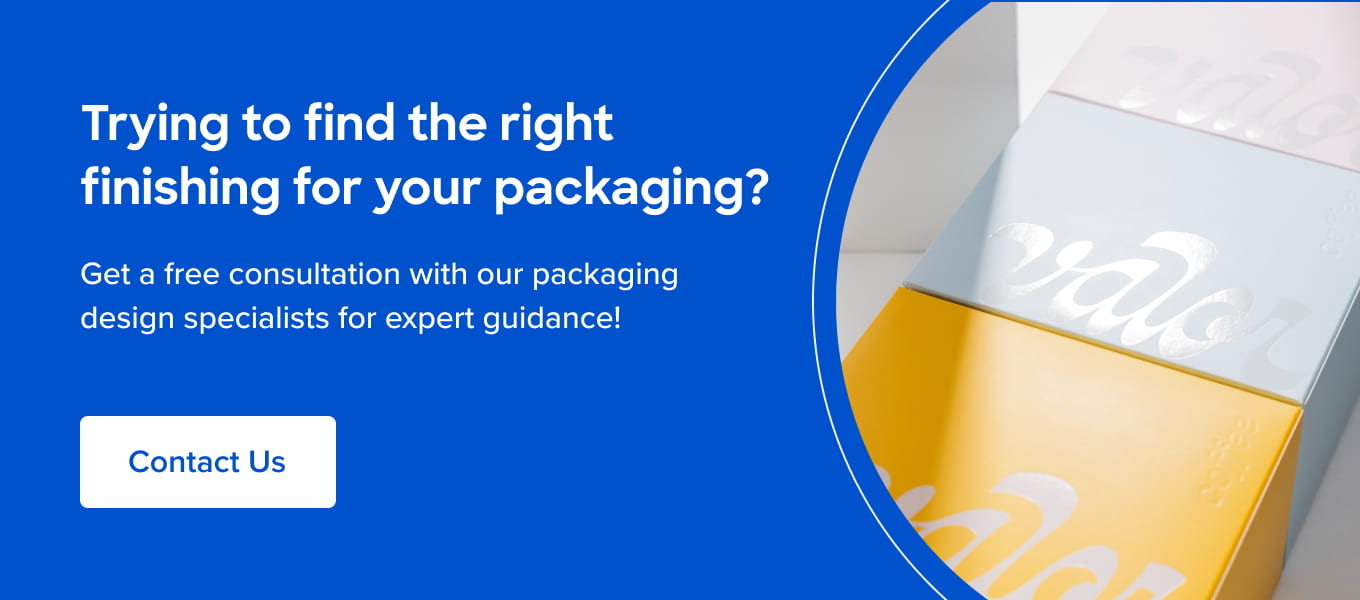
The Aqueous Coating Process
Now that we know the different coating types of this popular print coating method, what is the application process?
Put simply, special machines apply the aqueous coating immediately before printing ink on the sheets. Special care is taken to ensure no wrap, wrinkles, or curls occur on the paper during this process and after the application of the coating, the sheet passes through a heated air system for quick drying.
The video below is a great visual example of how this process is done.
The Final Coat for AQ
Although AQ coating provides several benefits, the chances of chemical burning with aqueous coating and UV coating are higher than other finishes such as varnish.
The solvent resistance of the aqueous coating is lower than that of UV coating and thermal lamination.
Nevertheless, AQ coating is still the most popular choice for print finish options thanks to its reliable and brilliant results.
Looking to learn more about your coating options for packaging?
Contact our product specialists today and get expert advice on finishing and printing options tailored to your product!