Table of Contents
There are lots of options for standard and specialty finishes available today for packaging box designs.
And the truth is it can be confusing, overly technical and overwhelming, especially for startups and new entrepreneurs.
Luckily, in this guide, you will learn how to choose the right coatings based on the compatibility with your overall packaging specifications (material, design, and cost).
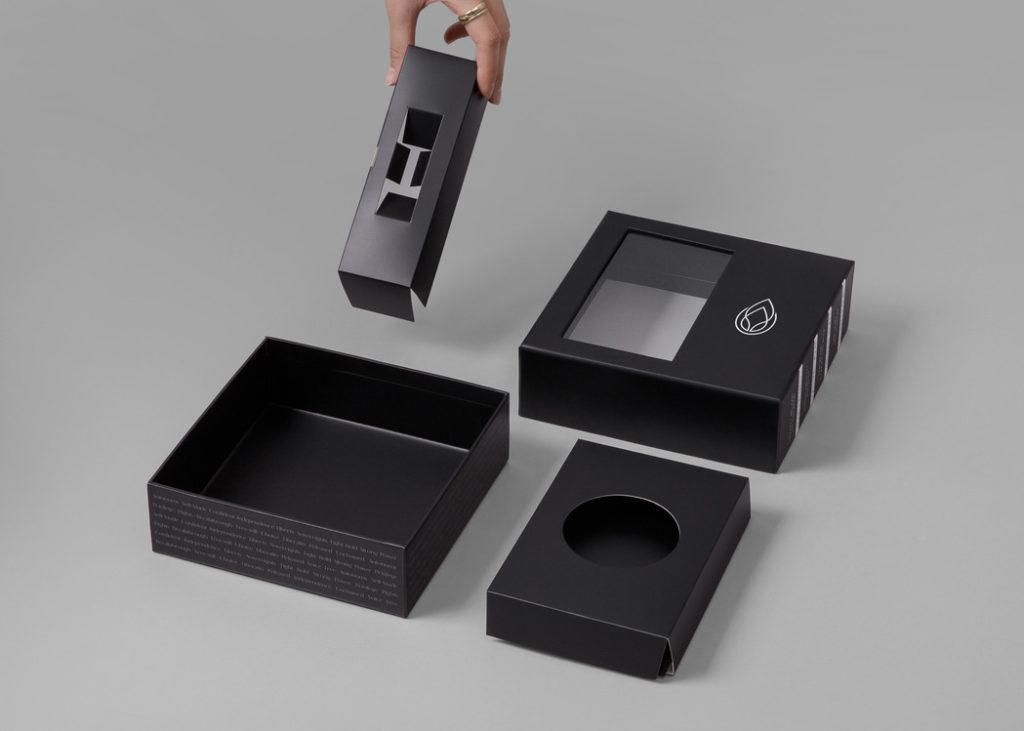
We’re here to arm you with all the information you need before you make your decision!
So before you decide on a coating for your packaging, we suggest you read these tips below.
Paperboard (Retail) Coatings
Since paperboard is flexible, versatile, and usually used for packaging products in retail stores, designers tend to be a little more creative with the finishing to create strong shelf impact.
Here are the popular coatings for paperboard packaging:
Lamination
Laminated paperboard boxes are widely regarded to have the best quality, but are typically more expensive due to its highly protective properties.
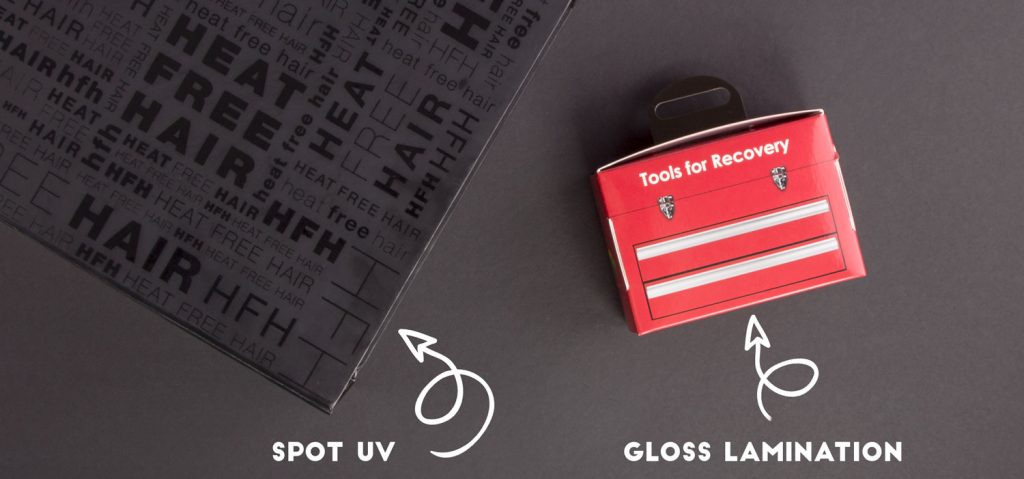
Compared to other coating types, lamination provides the best protection from moisture.
Long-run projects also typically prefer to use lamination due to their longevity and dust resistance.
It makes sense since you’ll be storing thousands of boxes that may not be used instantly.
Another advantage of lamination is its artwork output.
When you see that beautiful matte box in Sephora, the chances of it being laminated is quite high.
Luxury packaging tends to use matte lamination to achieve a simple yet elegant look and use gloss lamination to produce a vibrant and striking appearance.
UV & AQ Semi-Gloss Finishing
If you’re looking for a less expensive option, you might want to consider low gloss AQ coating.
Since AQ Semi-Gloss is water-based, it is a food-safe alternative. (please check with your manufacturer to verify their FDA compliant AQ coating).
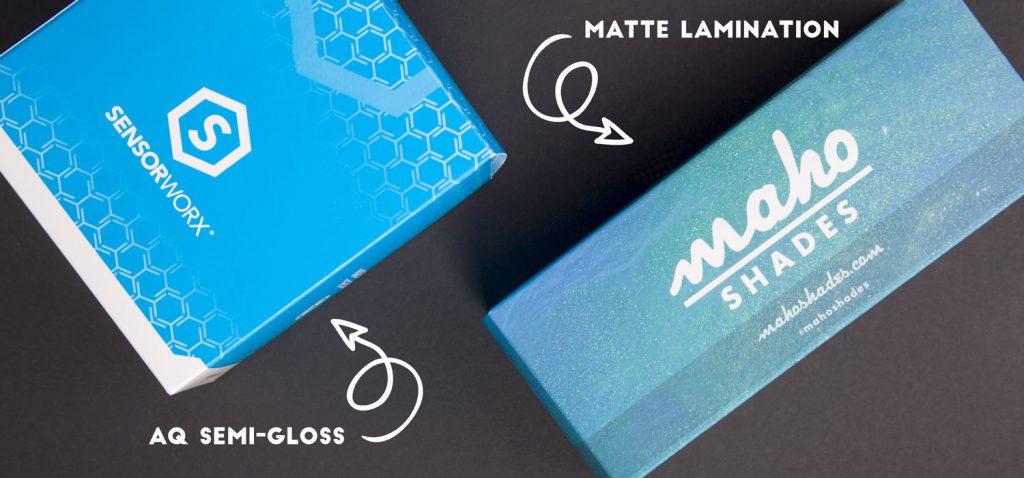
AQ is often the default of all coatings because of its price and effectiveness.
It provides a low gloss sheen that gives a bit of texture to the packaging but not too much that it distracts the eyes.
Ultraviolet Coatings (or UV coating), on the other hand, generates a glossy appearance just like gloss lamination.
Lamination or UV Coating?
Lamination is more tear-resistant. It is a better option to protect the packaging during shipping.
UV coating is much more eco-friendly but it doesn’t match the strength and protection that lamination provides.
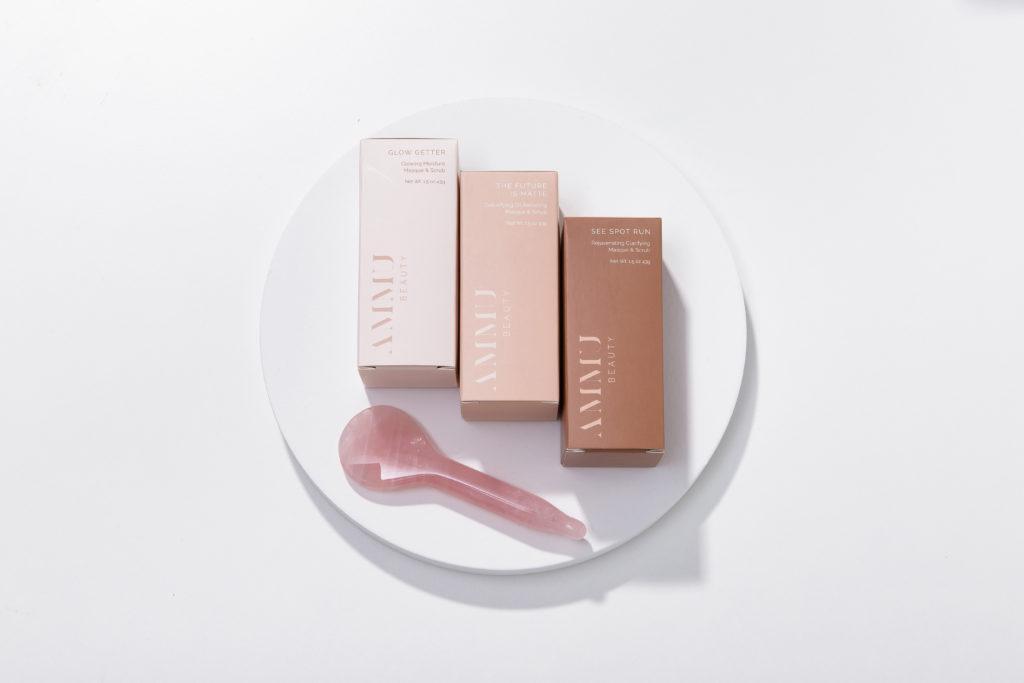
However, it adds maximum vibrancy to the packaging, it is quick to produce and has a lower cost per unit.
Corrugated (E-Commerce) Coatings
Companies often prefer to use corrugated cartons for shipping and e-commerce packaging because of its thicker and sturdier material.
These types of packaging can be coated similarly to paperboard (with the exclusion of AQ Semi-Gloss).
Let’s take a closer look at what is available.
Gloss Varnish (Little Gloss) / No-Coating
Particularly for low to medium-runs, these are the best options.
Why?
Digital printing for packaging is typically used to print small to medium-sized projects for corrugated packaging to increase production efficiency, generate a faster turnaround time and, overall lower unit cost.
As these boxes are mainly for shipping and transporting, it is rare to apply embellishments and expensive coating on the packaging.
However, this is changing, due to the phenomenon of unboxing experience videos.
Businesses are becoming more inclined to add more design elements to their shipping boxes to leverage marketing opportunities.
In addition, because the thickness of the corrugated material is enough to protect the products inside, the additional coating may not be needed.
Depending on the complexity or simplicity of your color, artwork, and branding, you could still produce a high-quality packaging box with low gloss varnish or no coating at all.
Lamination
Similarly to paperboard packaging, a laminated coating provides your box with the ultimate protection of your artwork.
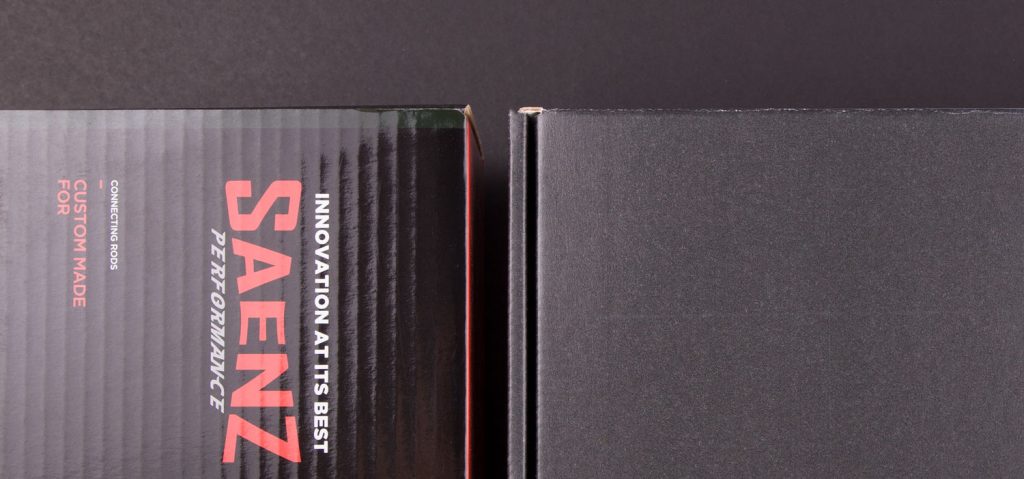
Businesses that use lamination on their shipping boxes are usually ones with very intricate details on their packaging and use it as a means to fully maximize their artwork appearance that digital printing simply can’t do.
The only disadvantage with gloss lamination or UV coating is that the ripples of the material are rather prominent.
Luxury (High End) Coatings
Simplicity, minimalist, luxury, and expensive is the typical characteristic of rigid box packaging.
It is a no-brainer that matte lamination is the most popular choice for this type of packaging.
Matte Lamination
Matte lamination is the most recommended coating for luxury boxes.
For one, the appearance of this particular finishing is widely known for its elegance (which is typically what most luxury brands want to achieve).
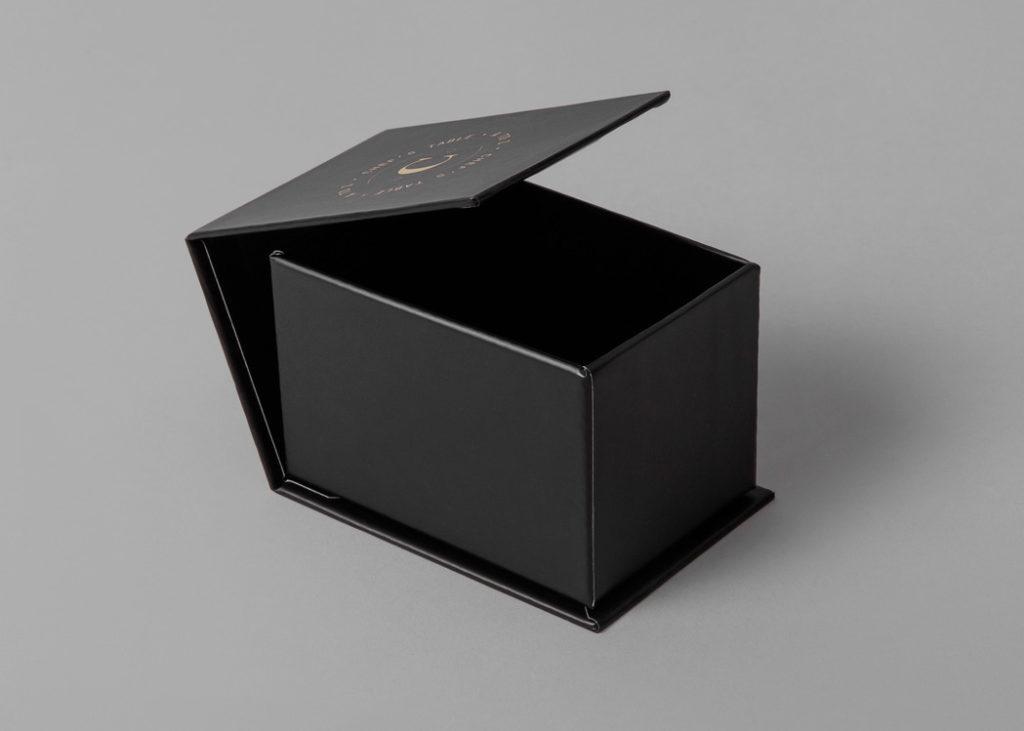
It is also the best coating to use when incorporating special processes into your boxes such as embossing, foil stamping, and spot UV.
Specialty Coating
If you simply have more than enough budget to invest in your packaging design that requires more unique elements, you can also opt for special coatings.
These types of coating are recommended for long-run orders due to its extra costs. However, if budget isn’t a problem, why not!
- Pearlized coating
- Glittered
- Reticulated
- Scented
Choosing the best coating for your product’s box packaging requires your time and attention.
You still have to do your homework and continue to communicate with your manufacturer or packaging expert to find the best fit for your packaging.
Remember, a well-prepared plan for your packaging will make your life a lot easier.
Have a solid idea of what your brand, your objective, and your budget is first.
From there, you can have a better sense of the overall packaging, including the coating and additional finishing that is right for your packaging!
Require more assistance and need more clarification on the different types of coating? Contact us at PakFactory anytime!