Table of Contents
Die-cutting is a popular manufacturing process in the packaging industry.
Chances are if you’re not a packaging expert, you probably don’t have a good idea of what the die-cutting process actually is.
Don’t worry, you’re not the only one!
Die-cutting has its origins in letterpress printing, and it evolved to become a more specific manufacturing process.
The die-cutting process in packaging utilizes a die to to cut materials into an array of different shapes, designs and patterns.
It’s most commonly used for, but not limited to, the manufacturing of folding carton packaging.
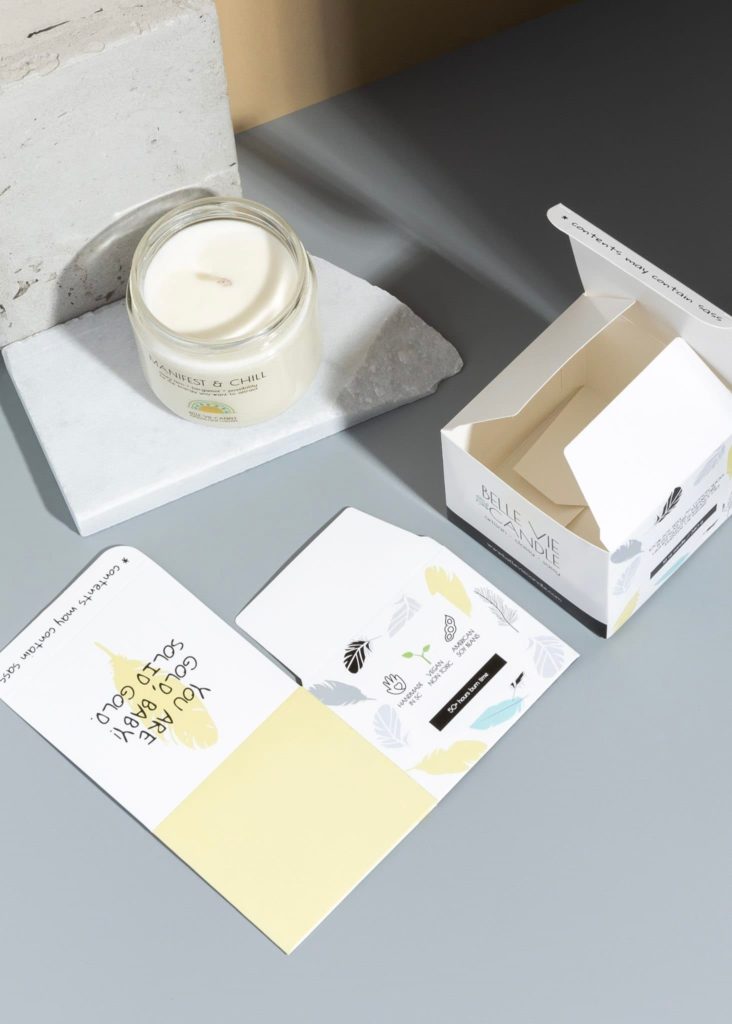
Die-cutting is used by businesses to create unique custom packaging tailored to their brand narratives and customer experience.
It is a very valuable process as it is easier, faster and more cost effective to produce custom packaging in larger quantities, making it a win-win situation for both manufacturers and businesses.
Here we will cover everything you need to know to get a better understanding of the die-cutting process.
What is a Die?
To understand the die-cutting process, it’s important to understand the components used to carry out manufacturing.
So, what exactly is a die?
A die is a specialized tool used to cut and shape packaging materials using a press.
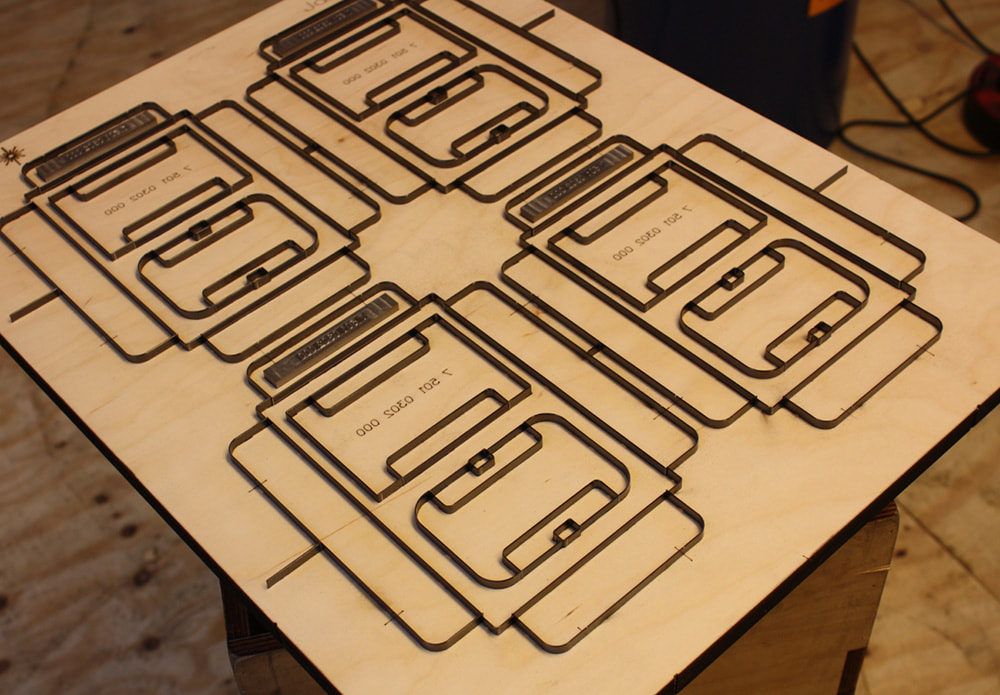
You can think of a die as a ‘mold’ that is shaped in the specific way needed to cut out your custom packaging.
Ultimately the first step to manufacturing your custom packaging is to form your die.
A die is created using tools and die makers to form your custom die before mounting it onto a press.
At this point you want to have your dieline finalized to start die-cutting your first batch of custom packaging.
Can dies be used more than once?
Yes, in fact it is recommended!
Creating dies for each packaging design is quite costly. However, it is a one time payment and outweighs the long term costs tremendously.
Once a die is created it can be used multiple times on the press to producing large volumes of packaging which becomes much more cost effective for your business.
Let’s say you have 3 products all of which come in the same packaging structure but different artwork designs for product differentiation.
You only really need 1 die to create thousands of boxes.
The die-cutting process is very effective in creating unique custom packaging that ultimately becomes a staple for your brand narrative.
While the production of custom dies might be off putting, look at it as an investment that your business can only benefit from!
Understanding the Die-Cutting Process
Think of a die-cutter as a giant cookie cutter that is pressed into your desired material to create your custom packaging.
Developments in technology and manufacturing techniques in the die-cutting process has allowed for more effective and accurate designs of die-cut boxes.
A packaging outline is generally created by Computer-Aided Design (CAD) and allows for digitized drawings of your dieline to be transferred onto the die board which is made from wood.
Your dieline is typically burned into the die board’s surface using laser cutters for more precise outlines.
This is why making sure you get the cut lines, fold lines, bleed lines and safe zones properly mapped out on your die line before moving forward with the die-cutting process.
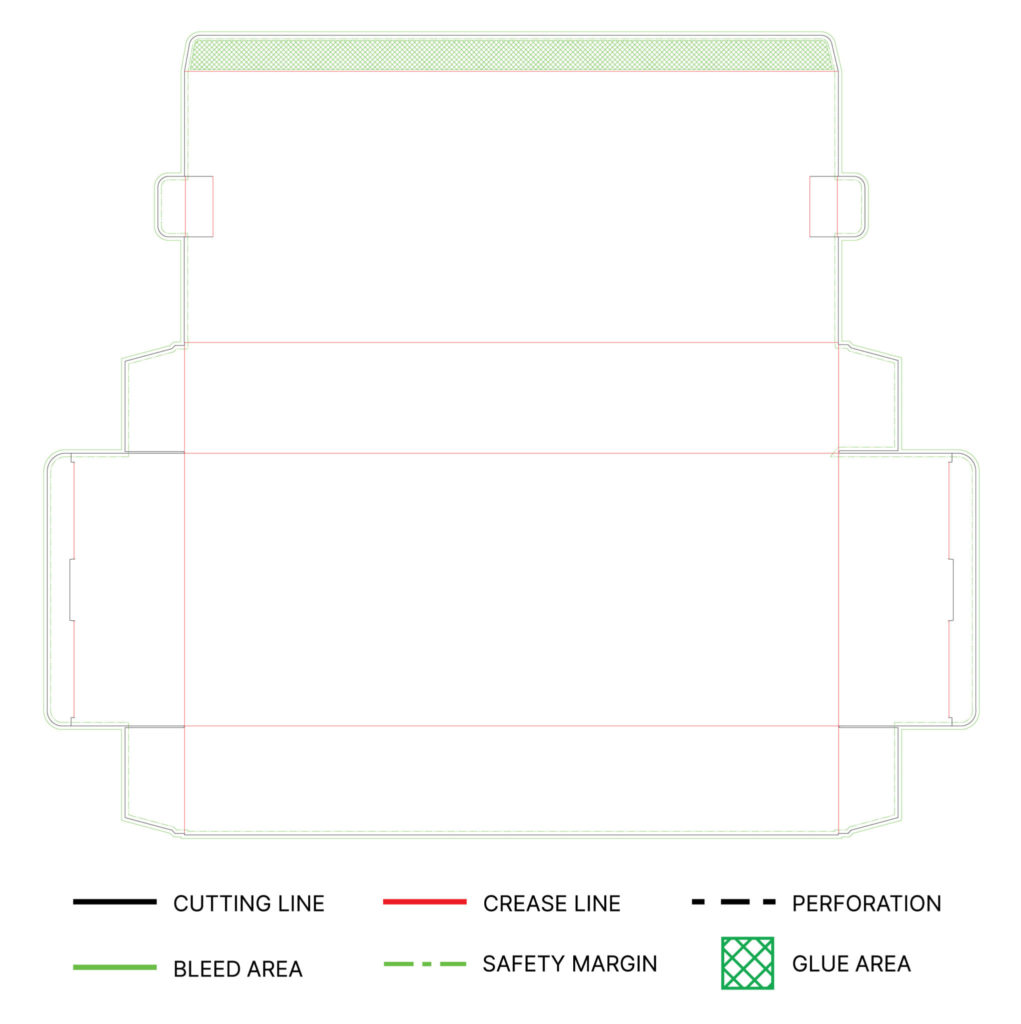
Since the introduction of laser cutters in the process of die-cutting, it has allowed for greater accuracy and precision when preparing die boards.
Die boards sit underneath the material during the die cutting process to ensure minimal movement and accurate placement while cutting for more precision.
Die boards almost act as a guideline for the blade once it’s made a cut through the material keeping the cuts straight and accurate.
While cutting is in the name of this process, die-cutting has many different functions including;
- Through cutting – cuts right through the material
- Scoring – leaves an impression, indent or partial cut on a specified area
- Creasing – creates a fold line for convenient construction
- Perforating – leaves a series of small cuts for easy tearing
Each of these functions serves a purpose for different types of packaging materials and structural designs.
Creasing is especially useful for the construction of corrugated packaging.
Steel rules are hammered into the die board accompanied with an array of foam and rubber pieces to ensure the die bounces off the corrugated board during production.
This ensures the crease lines are prominent and leave a lasting impression for easy folding.
As for the die-cutting process itself, the die-cutting machine firmly presses the die into the material to cut out the shape and perform it’s programmed functions mirrored on the die and die board.
The excess material is then collected and recycled when possible!
Die Cutting Methods
While we covered different functions when reviewing the die-cutting process, it also practices different methods.
These methods open a whole new world of structural design possibilities, and allows for a true custom packaging experience.
There are numerous types of die-cutting methods, including;
- Blanking: Flat material is sliced by clipping it from its exterior edge. Blanking produces an accurate degree of flatness.
- Drawing: Pulls the material to a predetermined length. It is used to create lean and long packaging.
- Forming: Shapes the raw material on a curved surface. It is typically used in tandem with a drawing to construct rounded cylindrical shapes.
- Coining: Makes circular holes in materials through the application of pressurized force to create meticulous and intricate structural design features.
- Broaching: Requires the use of multiple large rows of cutting teeth to cut materials that are usually too hard or thick to be cut by other means.
As seen with the list above, the die-cutting process can be applied to any packaging material you desire!
The Finishing Touches
As previously mentioned, the die-cutting process offers business a unique and truly customized packaging experience.
Luxury packaging, as we all know, communicates a high-end, sophisticated feel, but is expensive to produce.
However, if you have the funds to produce custom premium packaging, consider using the die-cutting process for this too!
The die-cutting process offers the opportunity to choose from a variety of finishing techniques that highlights and elevates your die-cut design.
These include;
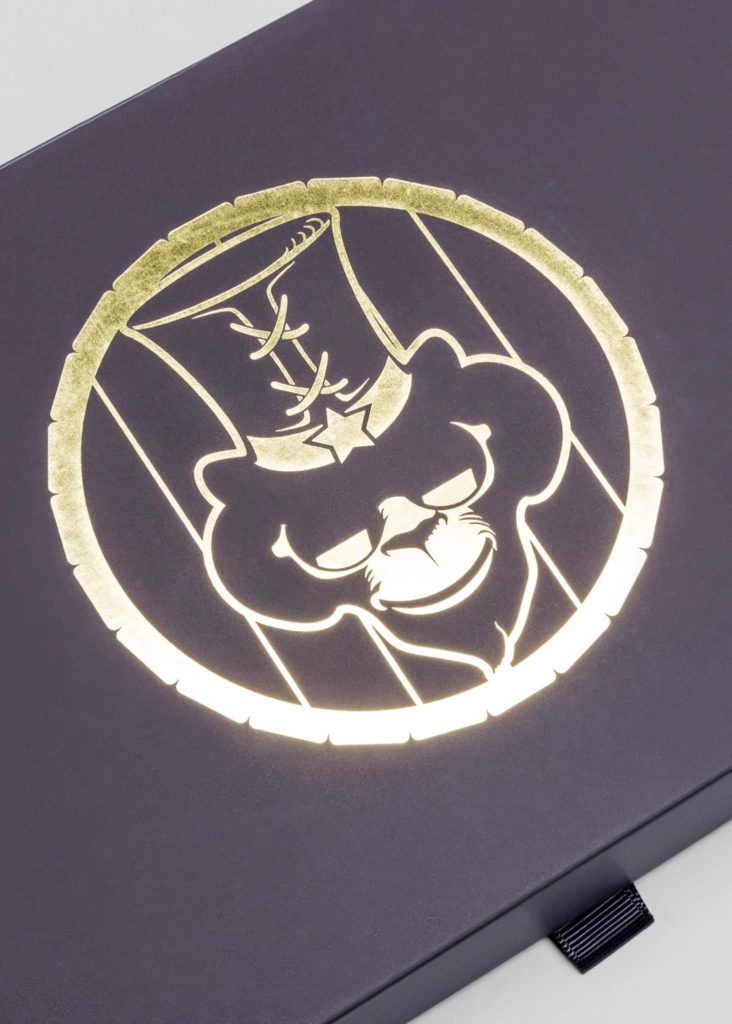
The die-cutting process makes custom packaging more accessible for both manufacturers and businesses. While the set up costs can be quite expensive, this disadvantage is counter acted by never having to pay that fee again for your specific design.
This process offers high quality accuracy in design while producing large volume orders time efficiently!
It also offers such a diverse range of functions and methods to choose from truly separating custom packaging from stock packaging and allowing businesses to really get creative with their packaging.
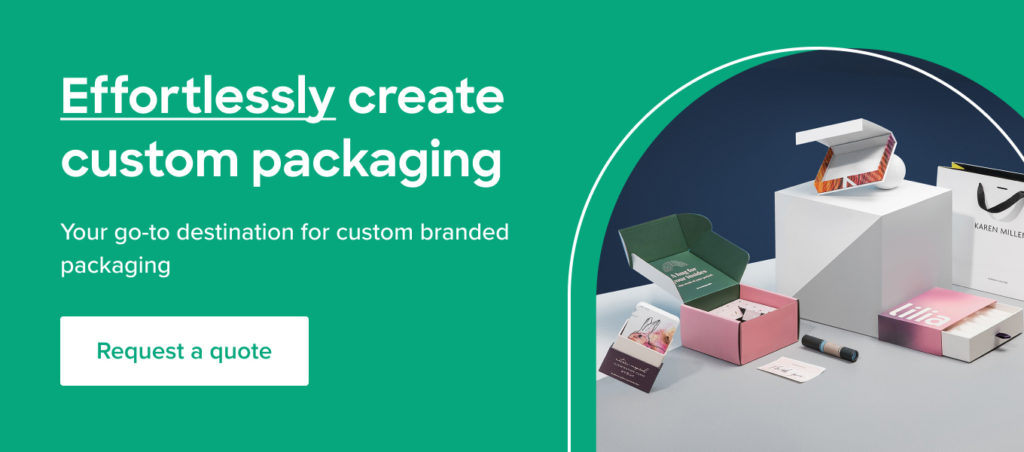