Table of Contents
Rigid packaging is a popular choice for certain products due to its excellent support and luxury feel. For this reason, it can also be known as set-up boxes, premium or high-end packaging due to its weight and expense. In this article, we will look in-depth at what this packaging is, how its constructed, the drawbacks and advantages, and explore some successful examples for you to consider.
So without further delay, let’s start with the basics; what is it?
What are Rigid Boxes or Set-up Boxes?
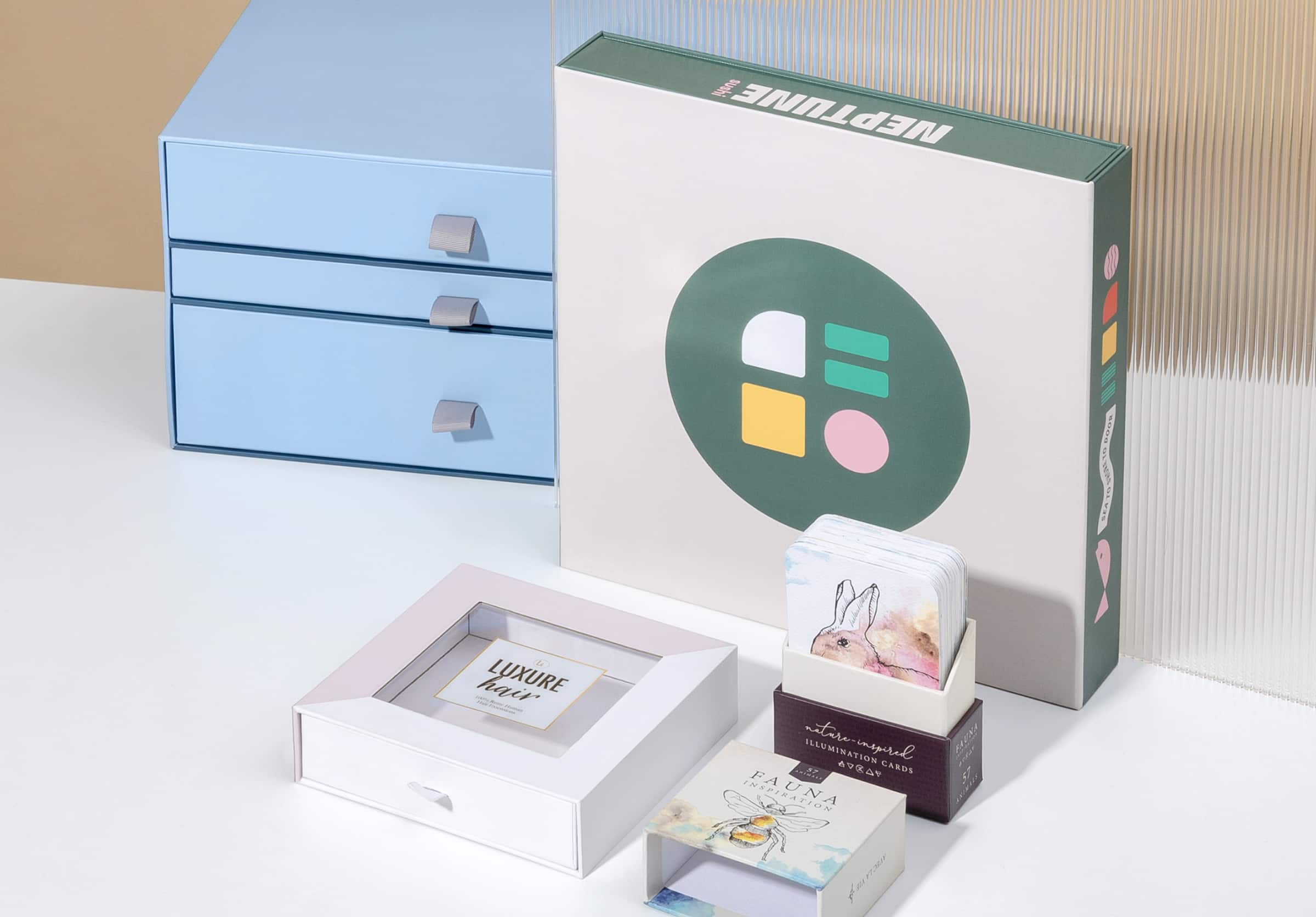
Source: PakFactory
Custom rigid boxes are sturdy paper-based packaging comprising high-thickness (often 2-3mm) chipboard wrapped in decorative specialty paper. As mentioned earlier, they are commonly referred to as set-up boxes or premium packaging due to their luxurious look and feel, which goes perfectly with items such as board games, luxury products like jewelry, or gifts.
Furthermore, these custom boxes offer a premium feel that enhances your customer’s unboxing experience allowing for more opportunities to establish a strong brand narrative. It provides many branding capabilities through printing and finishing options, including;
- Hot stamping
- Embossing/debossing
- Coatings
- Decorative elements
The Difference Between Flexible, Corrugated, Folding Cartons and Custom Rigid Boxes
Now if you have researched and read up on the other different types of packaging that may suit your product, you likely have heard of other options, such as flexible packaging, corrugated boxes and folding cartons. You can probably guess how flexible and rigid diverges by their names, but corrugated and folding cartons may be harder to distinguish. However, to cover all our bases, let’s briefly review each option and how they differ.
For starters, rigid boxes feature sturdy construction and support and are comparatively more luxurious in their look and feel. They are a trending packaging option consisting of thick chipboard and refer to solid packaging that won’t change shape, contrary to flexible packaging, which bends easily.
However, differentiation becomes a little more challenging when looking at the other options, as they are very similar. While rigid boxes are often viewed in a league of their own when it comes to presentation, popular alternatives include folding carton boxes and high-end corrugated packaging because of their cost efficiency and versatility in high-quality printing and finishing capabilities. Let’s look at the differences;
Rigid Boxes | Folded Carton Boxes | Corrugated Boxes | |
---|---|---|---|
Set up | None if not foldable | Needed | Needed |
Sturdiness | High | Low | High |
Product Safety | High | High with the aid of inserts | High |
Cost | Generally High | Depends on printing & finish | Depends on printing & finish |
Appeal | Generally High | Depends on printing & finish | Depends on printing & finish |
Reusable | Yes | Usually not | Yes |
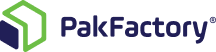
Source: PakFactory
As you can see from the above chart, the options are very similar and deciding which packaging solution to use is entirely up to you! So if you want to know more about the other options available, please read more about folding cartons or corrugated packaging. But if you are confident that this option suits your needs, let’s continue.
Types of Rigid Packaging
There are two different types of custom rigid boxes: partial finish and full finish.
A partial finish is where the wrapping and chipboard are only somewhat complete. The wrapping finishes the box’s outer surfaces, while the chipboard is left visible and bare. Partial finish boxes use a single piece of chipboard with perforated crease lines for folding and wrapping without the additional exterior layer that exposes the kraft or grey chipboard material.
This option is used because it takes much less time to produce due to the fewer materials needed in the construction process.
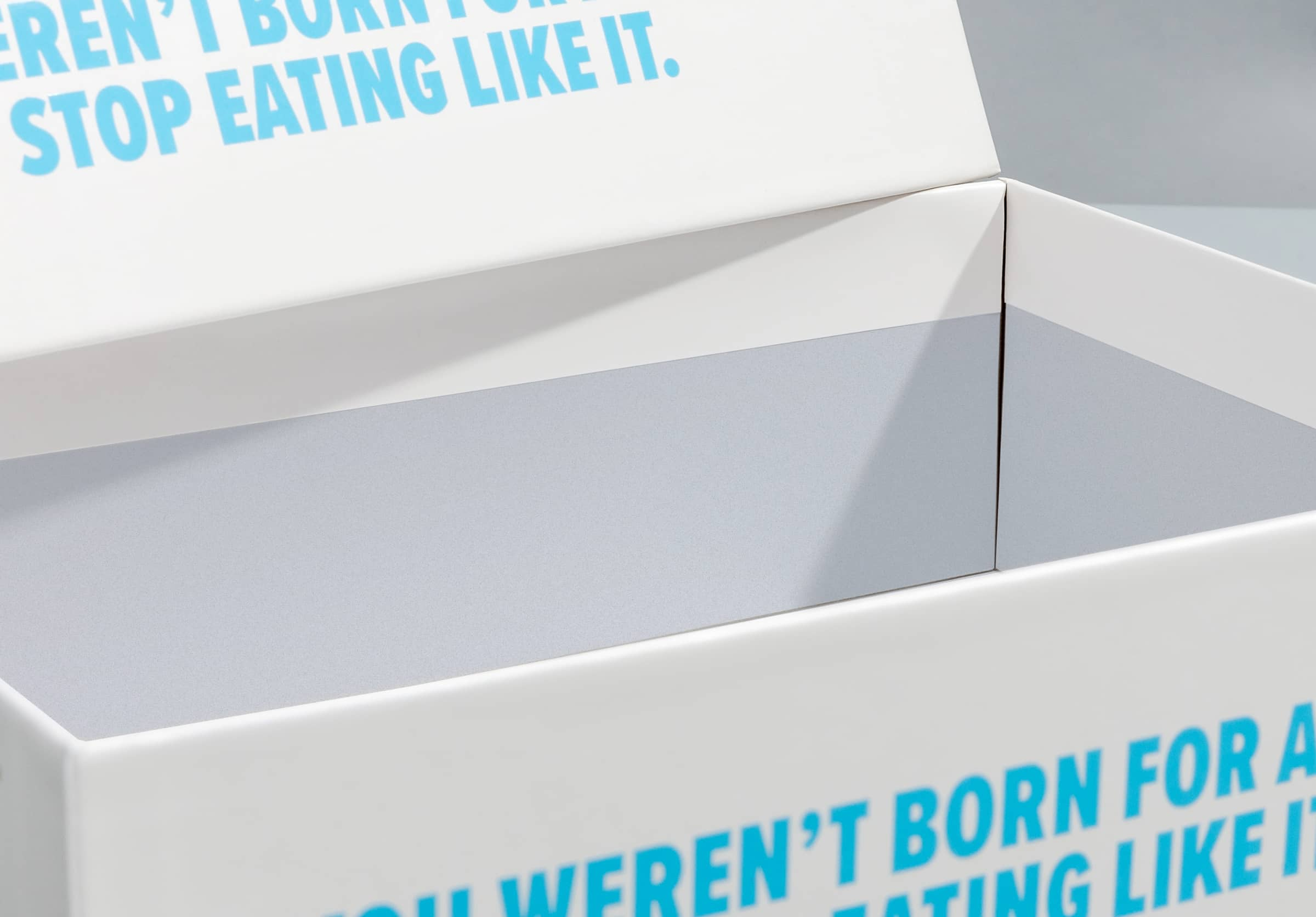
Source: PakFactory
On the other hand, a full finish leaves no chipboard exposed; the wrapping covers the entire box. This option uses a thicker 2-3 mm chipboard, and the inner chipboard is separated into pieces for each side of the box. Lamination is also possible with various finishing options depending on needs.
Full finish packaging also has an additional layer of wrapping, which is white by default or printed.

Source: PakFactory
So, in Summary:
Partial Finish:
- Wrapped only to finish the inner edge of a box
- Chipboard inside is unfinished and visible
- The internal chipboard is one piece with perforated crease lines and folds
- Tape is optional to secure the chipboard before wrapping
- Chipboard finish can come coated on one side using white or kraft
Full Finish:
- Wrapped entirely. No chipboard exposed
- The inner chipboard is in separate pieces for each face of the box
- No tape before wrapping boxes
- Thicker chipboard (or greyboard) at 2 – 3 mm thicknesses
- Laminated with different finishing options
How Is It Made?
But how do rigid boxes reach this finished state? To keep things simple, we have split up the process of constructing one of these high-end boxes into four simple steps that apply to both options:
- Sizing – The box starts as a flat paperboard that is first cut and scored to the correct size.
- Folding – The paperboard is then folded and secured to form the base of your box.
- Printing – A design is printed onto the wrap and laminated. Other add-ons can be included as you desire. The wrap is then glued to the shape of your box.
- Wrapping – The wrap tightly covers your box, and we are done!
If you are still unsure of the process to complete your box, the below figures should help paint a clearer picture:
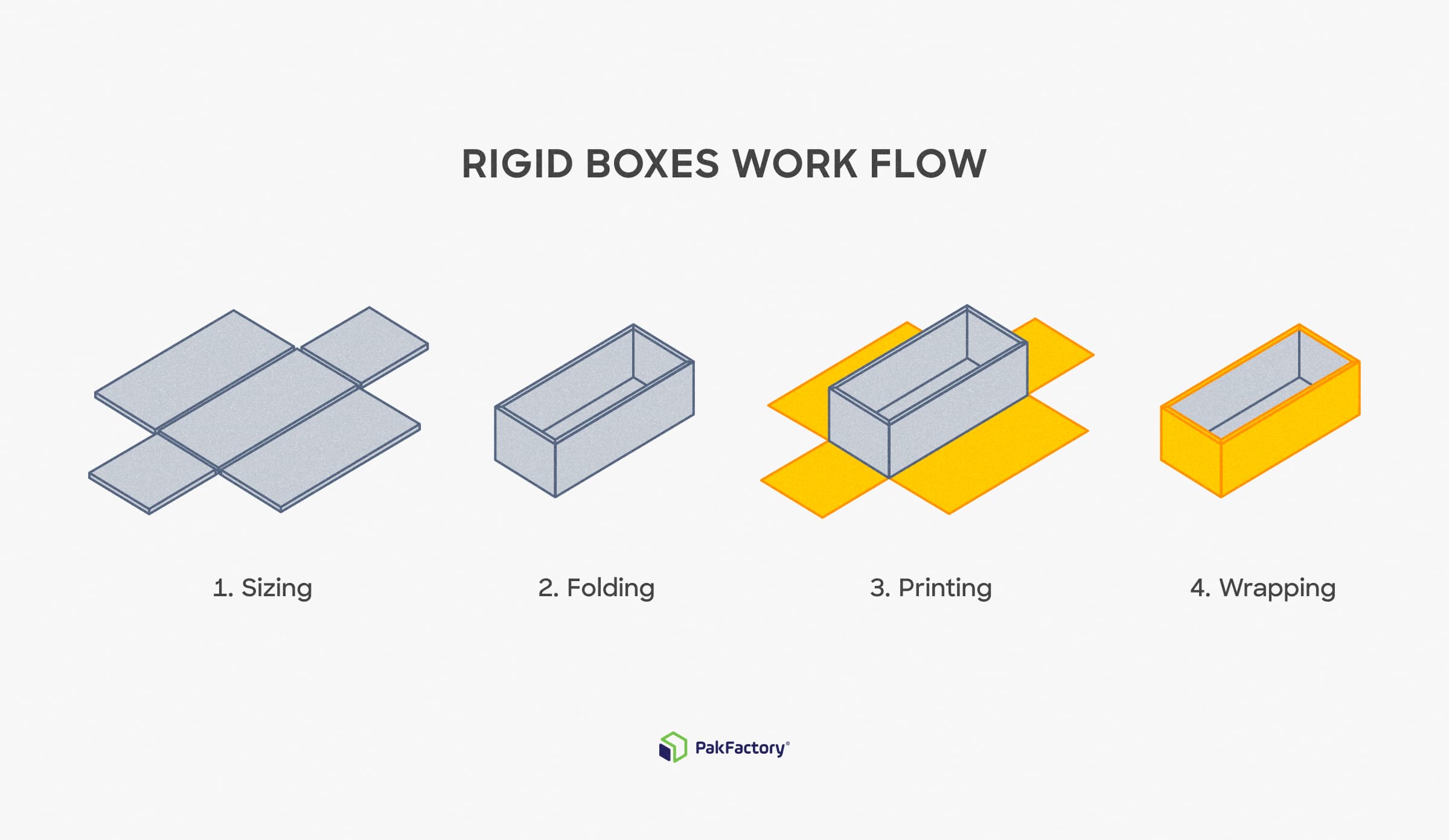
Source: PakFactory
Various High-End Packaging Styles
Not only do custom rigid boxes have two different types available to choose from, but there are also many style options as well! Let’s have a look at some popular options.
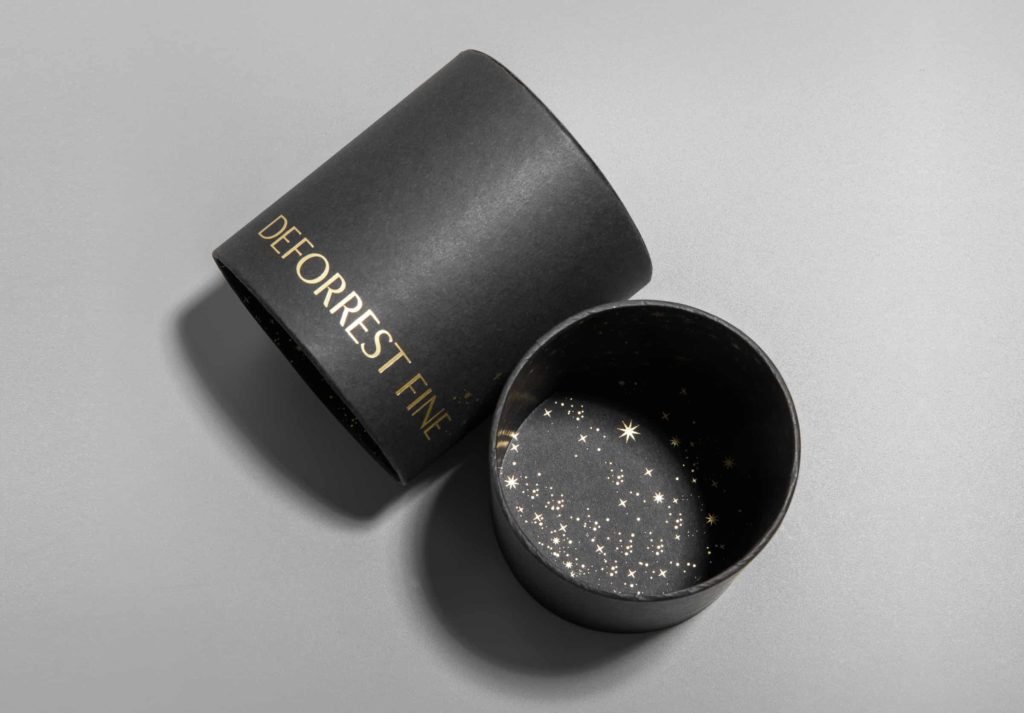
Tube or rolled-edge tube packaging is a cylindrical packaging option. It comes in telescopic or shoulder-neck opening styles, making it ideal for drinks, cosmetics, accessories, and snack containers like Pringle’s cans.
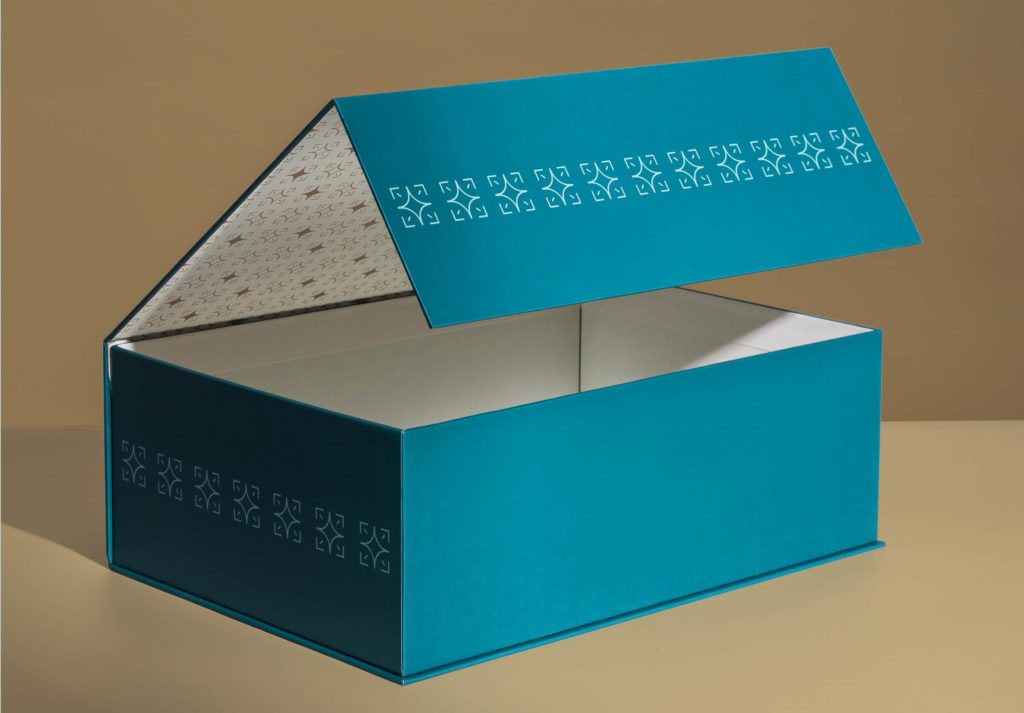
Magnetic closure boxes boast two sturdy magnets that effortlessly seal the box shut, adding a touch of luxury to jewelry and retail products. With their tactile closure, these versatile boxes can also be collapsible for convenient and friendly storage.
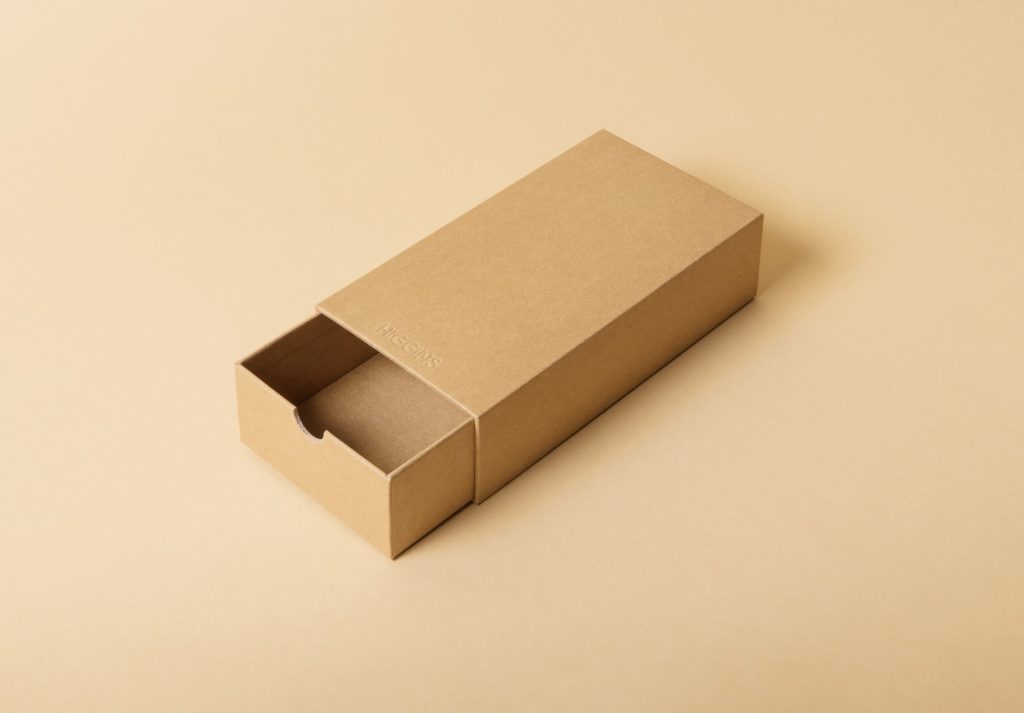
Drawer Style Boxes, as the name suggests, open up like a drawer. They are also known as slipcases, slides or matchboxes.
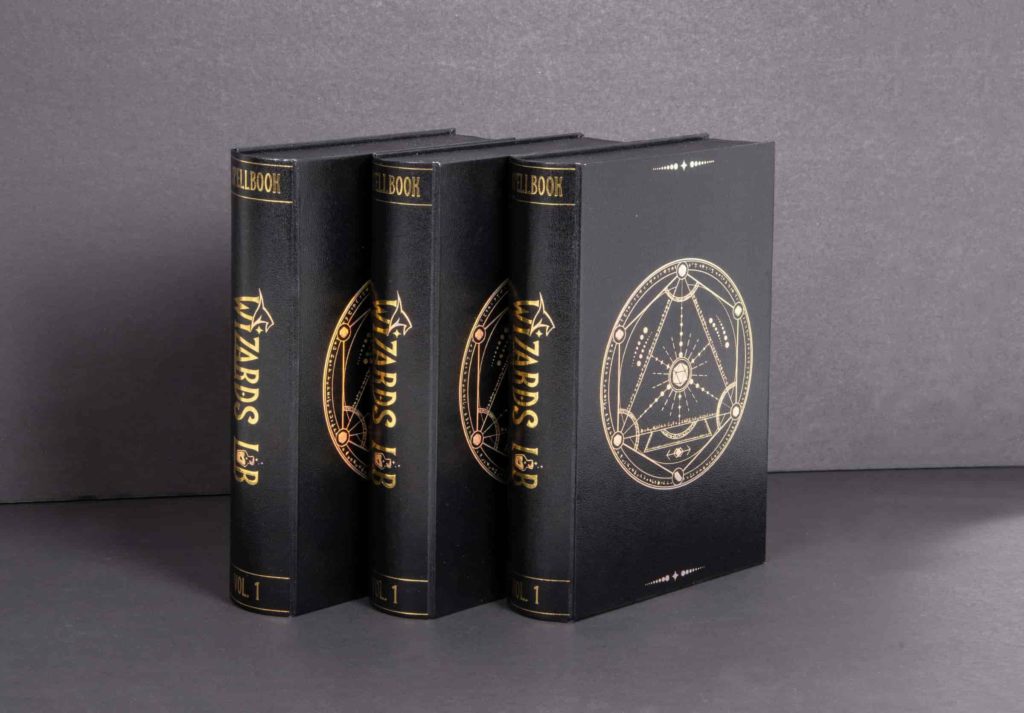
Book Style Boxes open like a hardcover book, adding creativity and innovation. With a straight or rounded spine, they provide a genuine book-like feel. Magnetic attachments can also be combined, creating a luxurious packaging option.
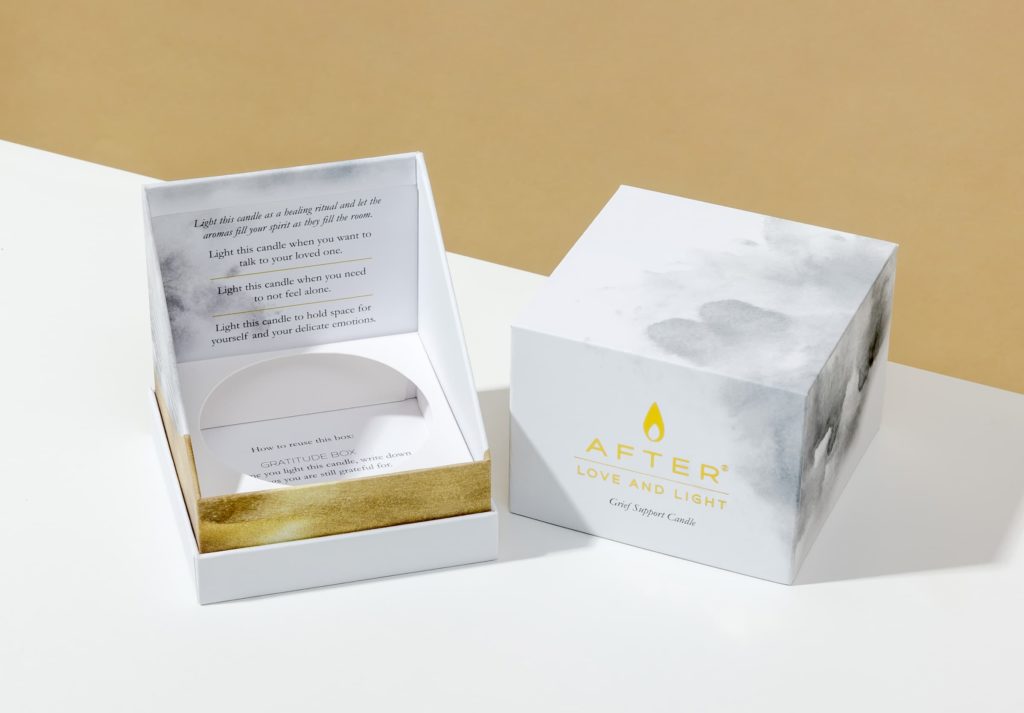
Shoulder Neck Boxes have multiple layers, including a distinct inner layer for the lid to rest on. Perfect for a unique unboxing experience, these boxes can be customized to match your brand’s colors and style.
Browse our full catalog of rigid box packaging here!
Inserts To Compliment Styles
The choices are limitless when it comes to styles of rigid boxes, but once you have decided on the type you prefer, the next step is to think about what inserts will go inside.
Additional packaging materials like box inserts are very popular when designing rigid packaging. Packaging inserts are highly recommended when you’re looking to get the ultimate unboxing experience.
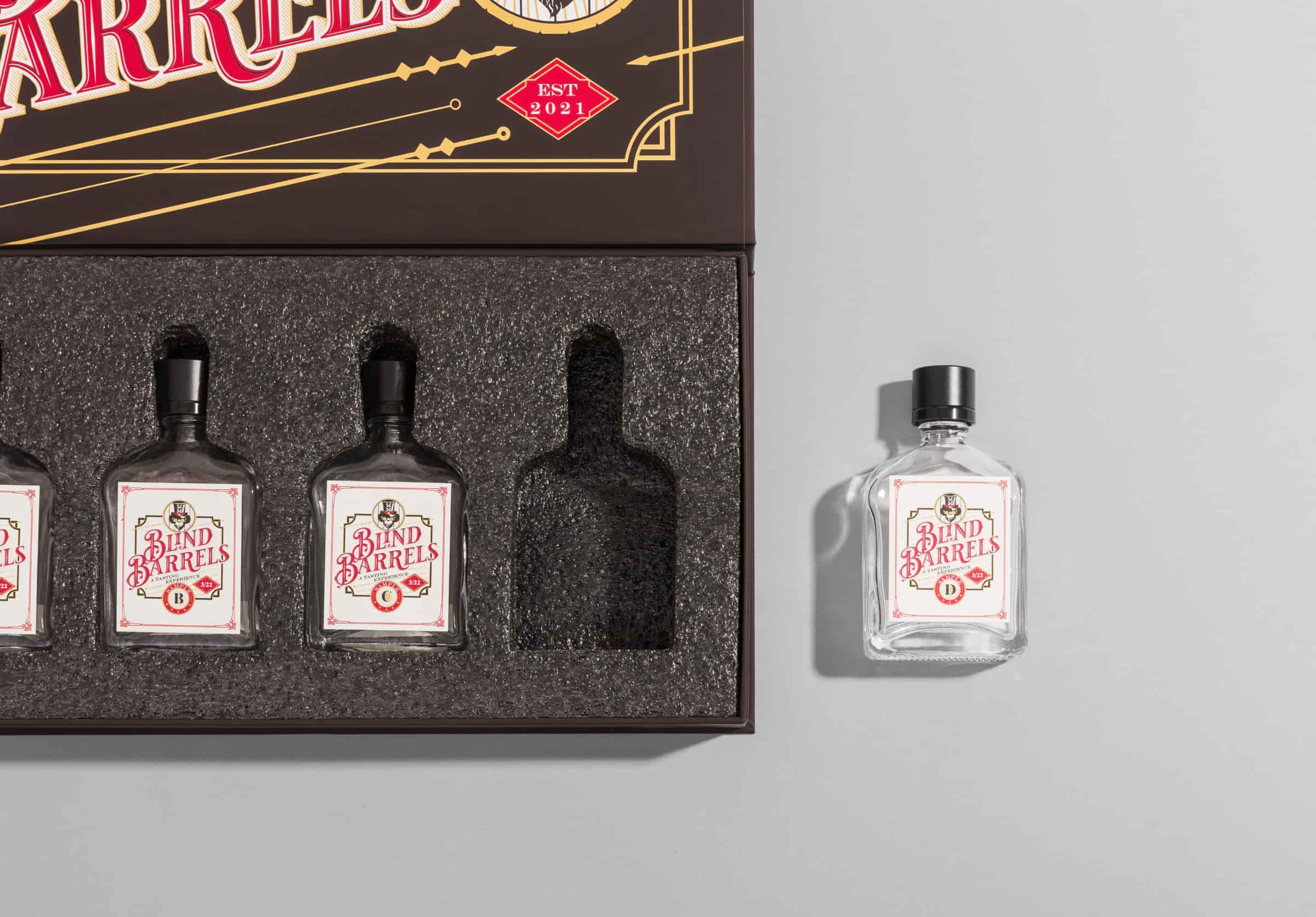
Source: PakFactory
A custom packaging insert is made specifically for your product, helping it stay in place to provide an elevated presentation while offering a high degree of shock protection, even against drops and rough handling.
Custom inserts most commonly come in;
- Paperboard
- Corrugated
- Molded pulp
- Foam
- Plastic
Is It Right For You? The Pros and Cons of Rigid Boxes
So now that we’ve finally covered all the available design choices, why should you choose this option? Well, besides its solid and protective construction, rigid packaging offers an elusive, luxurious and robust look and feel that is unmatched by most other packaging types.
Often paired with a custom insert, this packaging solution keeps products well-protected to withstand harsh handling. It is even made to be reusable and kept by the customer rather than just thrown away after unboxing a product.
With these benefits in mind, rigid packaging boxes build an embedded element to accompany your product, adding significant value to your brand. Customers will no longer view your product as just an individual item but rather consider the package and product as a set when your product is elegantly encased in a rigid box.
It is human nature to enjoy gifts, and rigid gift boxes are currently the gold standard of gift-type packaging. But with any type of packaging option, there are bound to be drawbacks.
While this packaging option is excellent for small to medium product sizes, they can become surprisingly less resilient at extra-large sizes. They are more prone to ripped edges at larger sizes due to increased load on the outer layer of wrapping paper, so it is always recommended to use thicker paper with a laminated finish to increase durability at larger sizes.
But the biggest con for high-end, custom rigid boxes is their price. To be blunt, making one of these boxes is expensive.
The construction of these high-end packages is unlike any other packaging style. Similar to wrapping a gift, custom rigid boxes are made by precisely wrapping paper around solid boards. Each chipboard is individually glued together, and producing these boxes involves an extended process that can take 1-2 weeks longer than other packaging options.
Currently, most production processes for this type of packaging involve some degree of manual assembly and more detailed quality checks to inspect for defects and ensure quality standards are required, making it up to 3 times more costly than folding carton and corrugated packaging.
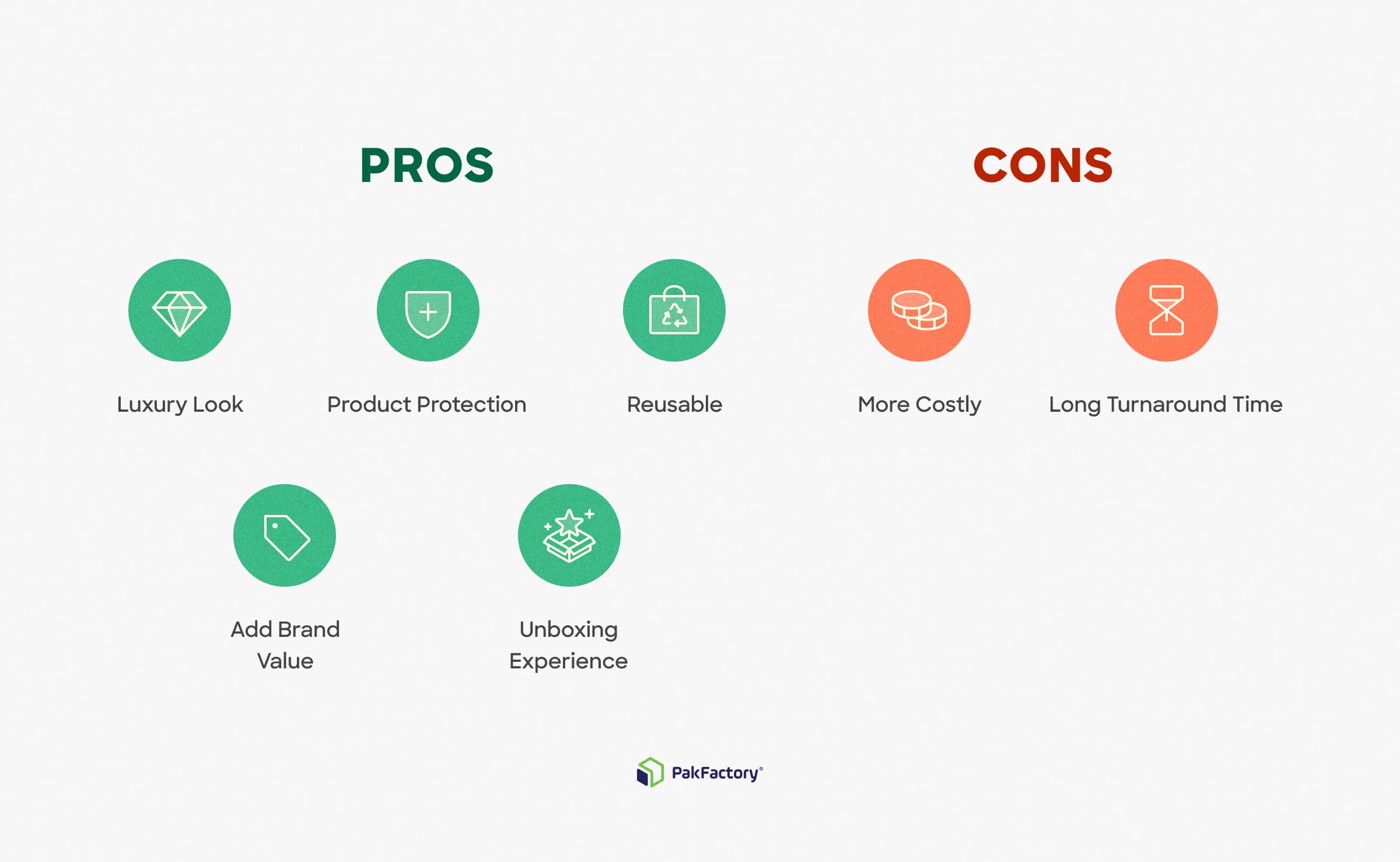
Source: PakFactory
And though the higher price can be readily justifiable to more prominent brands as luxury packaging adds tremendous amounts of perceived value to both the product and brand, we understand that many smaller companies are under budget constraints. For that reason, please check out our other article on how to create affordable luxury packaging and learn the many ways you can cut costs for rigid boxes and other options!
Rigid Box Solutions For Brands Across All Industries
With imagination comes courage, and with courage comes new and exciting ideas. Rigid packaging offers endless options for customization, personalization and luxury to fit any brand in any industry.
Don’t believe us? Check out some more cool rigid box ideas from different brands we’ve worked with!
Coca-Cola: The Taste of Celebration – Telescope Rigid Box with Custom Insert
Contender Brands: Combining Simplicity, Joy, and Laughter – Rolled-edge Rigid Tube Packaging with Custom Insert and Game Cards
Avec La Vie: Healing in a Package – Telescopic shoulder neck rigid box with game cards
Beda Beads: Inspiring the Next Generation of Creators – Magnetic Closure Rigid Box with Custom Insert